Packed bed reactors (PBRs) are widely used in chemical, petrochemical, and environmental engineering due to their unique design and operational advantages. Unlike fluidized bed reactors, PBRs consist of a fixed bed of solid catalyst or packing material through which reactants flow. This design offers several benefits, including high surface area for reactions, efficient heat and mass transfer, and scalability for industrial applications. PBRs are particularly advantageous for processes requiring precise control over reaction conditions, such as catalytic reactions, gas purification, and wastewater treatment. Their ability to handle high-pressure and high-temperature conditions makes them versatile for a wide range of applications.
Key Points Explained:
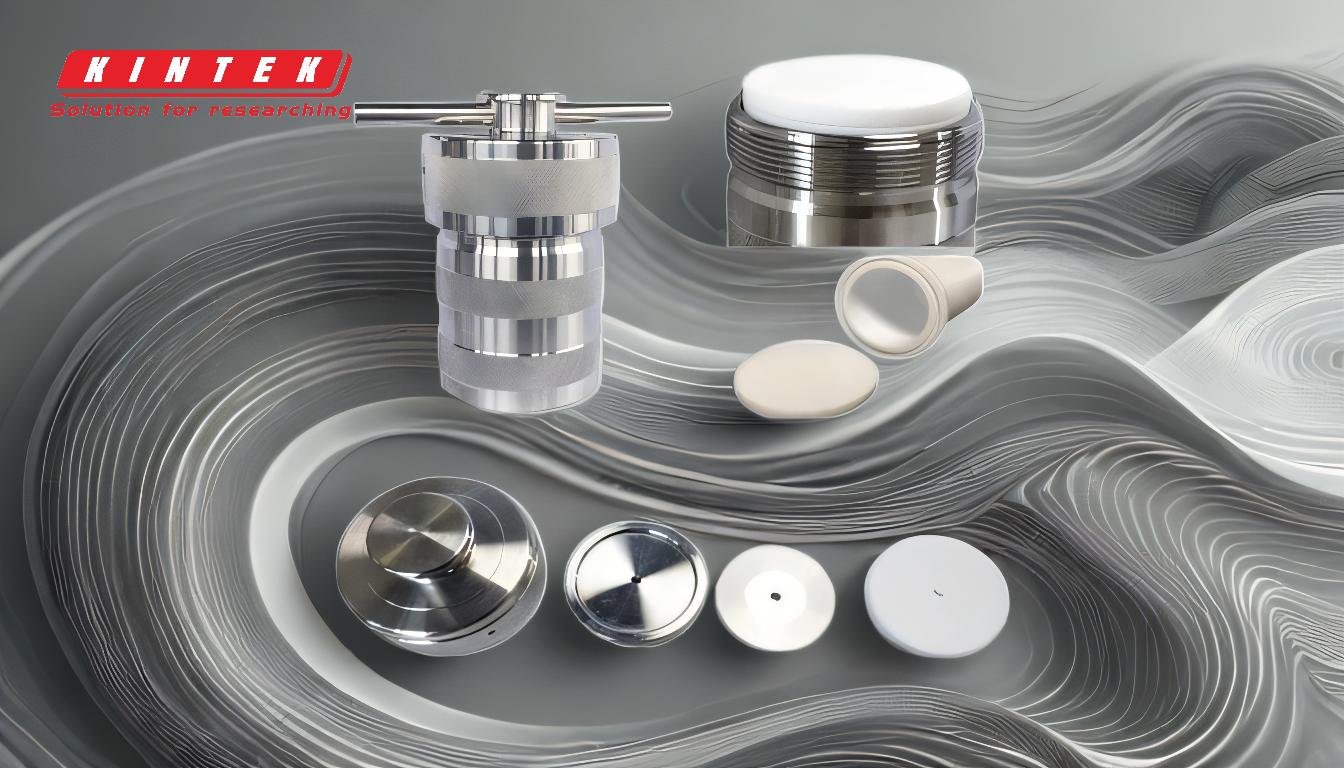
-
High Surface Area for Reactions
- Packed bed reactors are filled with solid catalyst particles or packing material, providing a large surface area for reactions to occur.
- This high surface area enhances the contact between reactants and catalysts, improving reaction rates and efficiency.
- For example, in catalytic processes like ammonia synthesis or hydrogenation, the increased surface area ensures higher conversion rates.
-
Efficient Heat and Mass Transfer
- The fixed bed design allows for effective heat transfer, which is crucial for exothermic or endothermic reactions.
- Heat can be managed through external cooling or heating systems, preventing temperature gradients and ensuring uniform reaction conditions.
- Mass transfer is also optimized due to the close contact between the fluid phase and the solid catalyst, reducing diffusion limitations.
-
Scalability for Industrial Applications
- Packed bed reactors are easily scalable, making them suitable for both laboratory research and large-scale industrial processes.
- Their modular design allows for customization based on the specific requirements of the reaction, such as flow rate, pressure, and temperature.
- This scalability is particularly beneficial in industries like petrochemicals, where large volumes of reactants are processed.
-
Handling High-Pressure and High-Temperature Conditions
- PBRs are designed to withstand extreme conditions, making them ideal for processes that operate under high pressure or temperature.
- For instance, in hydrocracking or hydrotreating processes in the petroleum industry, PBRs can handle the harsh conditions required for breaking down heavy hydrocarbons.
-
Precise Control Over Reaction Conditions
- The fixed bed design allows for precise control over parameters such as flow rate, residence time, and temperature.
- This control is essential for optimizing reaction yields and selectivity, especially in complex catalytic reactions.
- For example, in selective hydrogenation processes, precise control ensures the desired product is obtained without unwanted byproducts.
-
Versatility in Applications
- Packed bed reactors are used in a wide range of applications, including:
- Catalytic reactions (e.g., ammonia synthesis, methanol production).
- Gas purification (e.g., removal of pollutants like SO₂ and NOₓ).
- Wastewater treatment (e.g., biological filtration and adsorption processes).
- Their versatility stems from the ability to use different types of packing materials and catalysts tailored to specific processes.
- Packed bed reactors are used in a wide range of applications, including:
-
Cost-Effectiveness
- PBRs are generally more cost-effective than other reactor types due to their simple design and lower maintenance requirements.
- The absence of moving parts reduces wear and tear, leading to longer operational lifespans.
- Additionally, the use of solid catalysts can be more economical compared to liquid-phase catalysts in other reactor designs.
-
Environmental Benefits
- Packed bed reactors are often used in environmental applications, such as air and water purification.
- Their ability to efficiently remove pollutants and contaminants makes them a sustainable choice for industries aiming to reduce their environmental footprint.
- For example, in flue gas desulfurization, PBRs effectively remove sulfur dioxide emissions, contributing to cleaner air.
In summary, packed bed reactors offer a combination of high efficiency, scalability, and versatility, making them a preferred choice for many industrial and environmental processes. Their ability to handle extreme conditions and provide precise control over reaction parameters ensures optimal performance across a wide range of applications.
Summary Table:
Advantage | Description |
---|---|
High Surface Area for Reactions | Enhances contact between reactants and catalysts, improving reaction efficiency. |
Efficient Heat and Mass Transfer | Ensures uniform reaction conditions and reduces diffusion limitations. |
Scalability for Industrial Use | Easily customizable for lab research or large-scale industrial processes. |
Handles High Pressure/Temperature | Ideal for extreme conditions like hydrocracking and hydrotreating. |
Precise Control Over Reactions | Optimizes yields and selectivity in complex catalytic processes. |
Versatility in Applications | Used in catalytic reactions, gas purification, and wastewater treatment. |
Cost-Effectiveness | Simple design, low maintenance, and long operational lifespan. |
Environmental Benefits | Efficiently removes pollutants, contributing to cleaner air and water. |
Learn how packed bed reactors can optimize your industrial processes—contact our experts today!