Sputtering deposition is a highly versatile and efficient thin-film deposition technique with numerous advantages over other methods. It offers better adhesion, higher kinetic energy of deposited atoms, and the ability to deposit materials with high melting points. The process is reproducible, automatable, and compatible with a wide range of materials, including plastics, organics, glass, and metals. Sputtering allows for molecular-level precision, enabling pristine interfaces and tunable film properties. Additionally, it supports reactive deposition, epitaxial growth, and simultaneous double-sided coating, making it suitable for advanced applications. Its cost-effectiveness, low-temperature operation, and maintenance-free nature further enhance its appeal for industrial and research applications.
Key Points Explained:
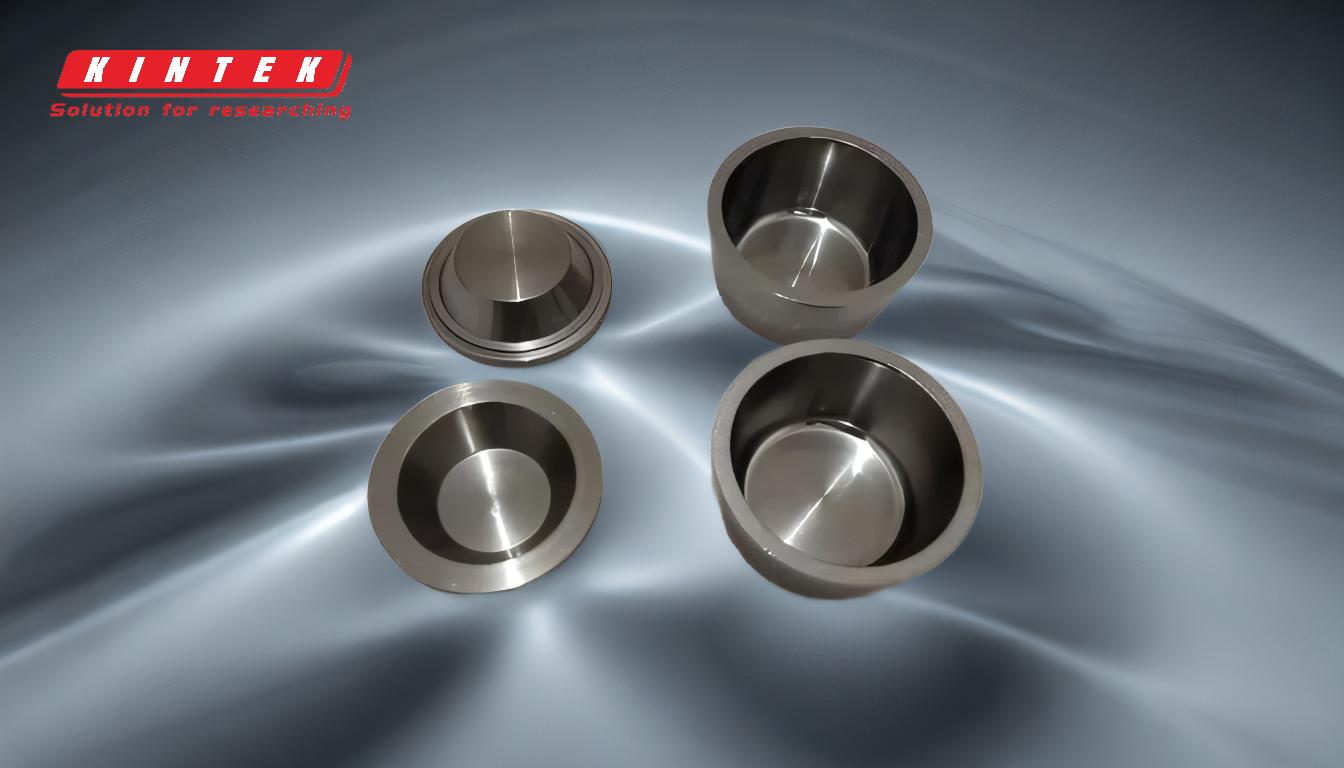
-
Superior Adhesion and Kinetic Energy:
- Sputter-ejected atoms possess significantly higher kinetic energy compared to evaporated materials, resulting in stronger adhesion to substrates. This ensures durable and reliable thin films, even on challenging surfaces.
-
Versatility in Deposition Orientation:
- Sputtering can be performed in both bottom-up and top-down configurations, providing flexibility in coating complex geometries and ensuring uniform coverage.
-
Deposition of High-Melting-Point Materials:
- Materials with very high melting points, which are difficult or impossible to evaporate, can be easily sputtered. This expands the range of materials that can be deposited, including refractory metals and ceramics.
-
Reproducibility and Automation:
- Sputter deposition offers excellent reproducibility and simpler process automation compared to methods like E-Beam or thermal evaporation. This makes it ideal for high-volume manufacturing and consistent film quality.
-
Reactive Deposition for Optical Films:
- By oxidizing or nitriding sputtered metal ions, sputtering can produce oxide or nitride film layers with precise compositions, making it suitable for optical coatings and other specialized applications.
-
Low-Temperature Operation:
- Sputtering can coat a wide range of materials, including plastics and organics, at reduced temperatures. This minimizes thermal damage to sensitive substrates.
-
Molecular-Level Precision:
- The process allows for atomic-level control, enabling the creation of pristine interfaces between materials and the ability to fine-tune film properties through precise control of process parameters.
-
Strong Film Adhesion and Step Coverage:
- Sputtered films exhibit strong adhesion and excellent step or via coverage, making them suitable for microelectronics and semiconductor applications.
-
Double-Sided Coating:
- With appropriate mechanical configurations, sputtering can perform simultaneous double-sided coating, enhancing process efficiency and throughput.
-
Compatibility with Reactive Gases and Ultrahigh Vacuum:
- Sputtering is compatible with reactive gases and can be performed in ultrahigh vacuum conditions, enabling advanced processes like epitaxial growth and high-purity film deposition.
-
Cost-Effectiveness:
- Compared to other deposition methods, sputtering is relatively inexpensive, making it an attractive option for both research and industrial applications.
-
Uniform Films and High Packing Density:
- Sputtered films are more uniform and have higher packing densities, even at low temperatures, ensuring consistent performance and durability.
-
Broad Material Compatibility:
- Sputtering works well with a wide range of materials, including diverse mixtures and alloys, offering greater flexibility in material selection compared to thermal evaporation.
-
Maintenance-Free Operation:
- The process is maintenance-free, reducing downtime and operational costs, and ensuring long-term reliability.
-
Enhanced Process Efficiency:
- Features like load lock chamber entry and exit improve process efficiency, making sputtering a practical choice for high-throughput environments.
In summary, sputtering deposition stands out as a highly adaptable, precise, and cost-effective method for thin-film deposition, offering numerous advantages that cater to a wide range of applications, from microelectronics to optical coatings and beyond.
Summary Table:
Advantage | Description |
---|---|
Superior Adhesion | Higher kinetic energy ensures strong adhesion, even on challenging surfaces. |
Versatility in Deposition Orientation | Can coat complex geometries in bottom-up or top-down configurations. |
High-Melting-Point Materials | Deposits materials like refractory metals and ceramics with ease. |
Reproducibility and Automation | Ideal for high-volume manufacturing with consistent film quality. |
Reactive Deposition | Produces precise oxide or nitride layers for optical coatings. |
Low-Temperature Operation | Coats plastics and organics without thermal damage. |
Molecular-Level Precision | Enables pristine interfaces and tunable film properties. |
Strong Step Coverage | Suitable for microelectronics and semiconductor applications. |
Double-Sided Coating | Simultaneous coating enhances efficiency and throughput. |
Compatibility with Reactive Gases | Supports advanced processes like epitaxial growth and high-purity deposition. |
Cost-Effectiveness | Affordable compared to other deposition methods. |
Uniform Films | Ensures consistent performance and durability. |
Broad Material Compatibility | Works with diverse mixtures and alloys, offering flexibility in material selection. |
Maintenance-Free | Reduces downtime and operational costs. |
Enhanced Process Efficiency | Load lock chamber entry and exit improve throughput in high-volume environments. |
Ready to leverage sputtering deposition for your projects? Contact us today to learn more!