Evaporation under vacuum conditions offers several significant benefits, particularly in industrial and scientific applications such as thin-film deposition and material purification. The primary advantage is the creation of a contamination-free environment, ensuring high-purity results. In a vacuum, unwanted vapors and gases are removed, allowing evaporated particles to travel directly to the target without interference. This improves deposition quality, enhances control over the process, and enables the use of various source materials. Additionally, vacuum evaporation is cost-effective, allows for precise rate control, and supports the use of masks or shutters for selective deposition. These benefits make it a preferred method for producing durable, high-quality layers with long service life and high dimensional accuracy.
Key Points Explained:
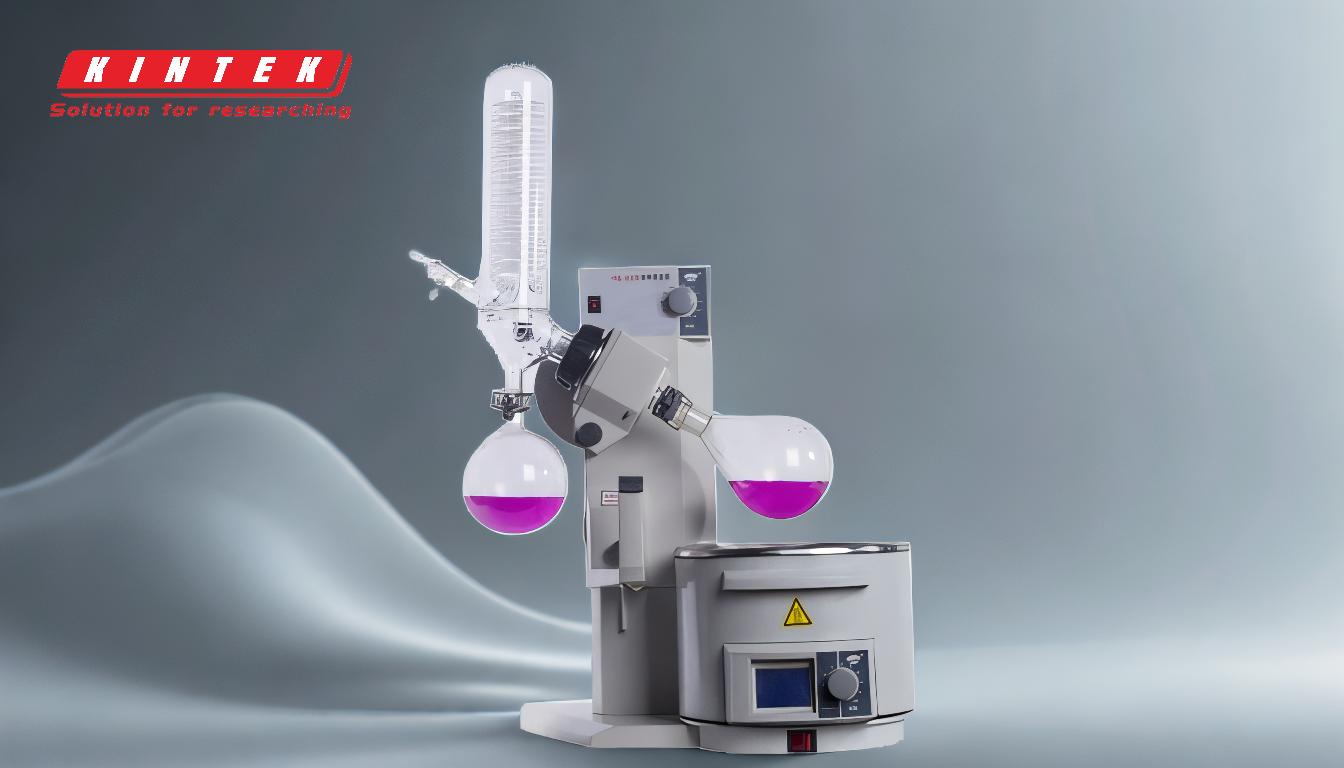
-
Contamination-Free Environment
- Evaporation in a vacuum removes unwanted vapors and gases, ensuring that only the source material is deposited.
- This minimizes impurities and contamination, which is critical for applications requiring high-purity thin films, such as in semiconductor manufacturing or optical coatings.
-
Improved Deposition Quality
- In a high vacuum, evaporated particles travel directly to the target without colliding with background gas molecules.
- This reduces scattering and ensures a uniform, high-quality deposition, resulting in films with better adhesion, density, and surface finish.
-
Enhanced Process Control
- Vacuum conditions allow precise control over pressure and evaporation rates.
- This enables operators to achieve specific deposition rates without excessively raising the temperature, which can degrade sensitive materials or cause uneven evaporation.
-
Versatility with Source Materials
- Vacuum evaporation can utilize solid materials in any form (e.g., pellets, wires, or powders).
- This flexibility makes it suitable for a wide range of applications, from depositing metals to creating complex multi-layer structures.
-
Cost-Effectiveness
- The process is relatively economical compared to other deposition techniques, as it requires minimal consumables and can be easily scaled for industrial use.
- The ability to reuse masks and shutters further reduces costs.
-
Use of Masks and Shutters
- Vacuum evaporation systems can incorporate masks and shutters to define specific deposition areas.
- This is particularly useful for creating patterned thin films or depositing materials selectively on a substrate.
-
High-Purity Films
- The process ensures that only the source material is deposited, resulting in films with exceptional purity.
- This is essential for applications in electronics, optics, and other high-tech industries where material purity directly impacts performance.
-
Long Service Life and Durability
- Films produced through vacuum evaporation are known for their durability and long service life.
- This makes them ideal for applications requiring high wear resistance, such as protective coatings or industrial tools.
-
High Dimensional Accuracy
- The controlled environment of vacuum evaporation allows for precise control over film thickness and uniformity.
- This ensures high dimensional accuracy, which is critical for applications like microelectronics and precision optics.
-
Improved Solvent-Product Separation
- In processes like solvent evaporation, vacuum conditions enable controlled and even evaporation, improving the separation of solvents from products.
- This is particularly useful in chemical and pharmaceutical industries for purifying substances or concentrating solutions.
By leveraging these benefits, vacuum evaporation has become a cornerstone technology in industries requiring high-quality, precise, and contamination-free material deposition. Its versatility, cost-effectiveness, and ability to produce durable, high-purity films make it an indispensable tool for modern manufacturing and research.
Summary Table:
Benefit | Description |
---|---|
Contamination-Free Environment | Removes unwanted vapors and gases, ensuring high-purity deposition. |
Improved Deposition Quality | Uniform, high-quality films with better adhesion, density, and surface finish. |
Enhanced Process Control | Precise control over pressure and evaporation rates for consistent results. |
Versatility with Source Materials | Works with solids in any form (pellets, wires, powders) for diverse applications. |
Cost-Effectiveness | Economical process with minimal consumables and reusable masks/shutters. |
Use of Masks and Shutters | Enables selective deposition for patterned or localized thin films. |
High-Purity Films | Ensures exceptional material purity for electronics, optics, and more. |
Long Service Life and Durability | Produces durable films ideal for wear-resistant applications. |
High Dimensional Accuracy | Precise control over film thickness and uniformity for critical applications. |
Improved Solvent-Product Separation | Controlled evaporation for better separation in chemical and pharmaceutical processes. |
Ready to enhance your thin-film production? Contact us today to learn more about vacuum evaporation solutions!