When designing a vacuum system, particularly for specialized applications like a vacuum hot press, several critical factors must be considered to ensure optimal performance and efficiency. These include the system's pressure requirements, temperature control, material compatibility, safety features, and the specific application needs. By carefully evaluating these aspects, one can design a vacuum system that meets both operational and safety standards while achieving the desired outcomes.
Key Points Explained:
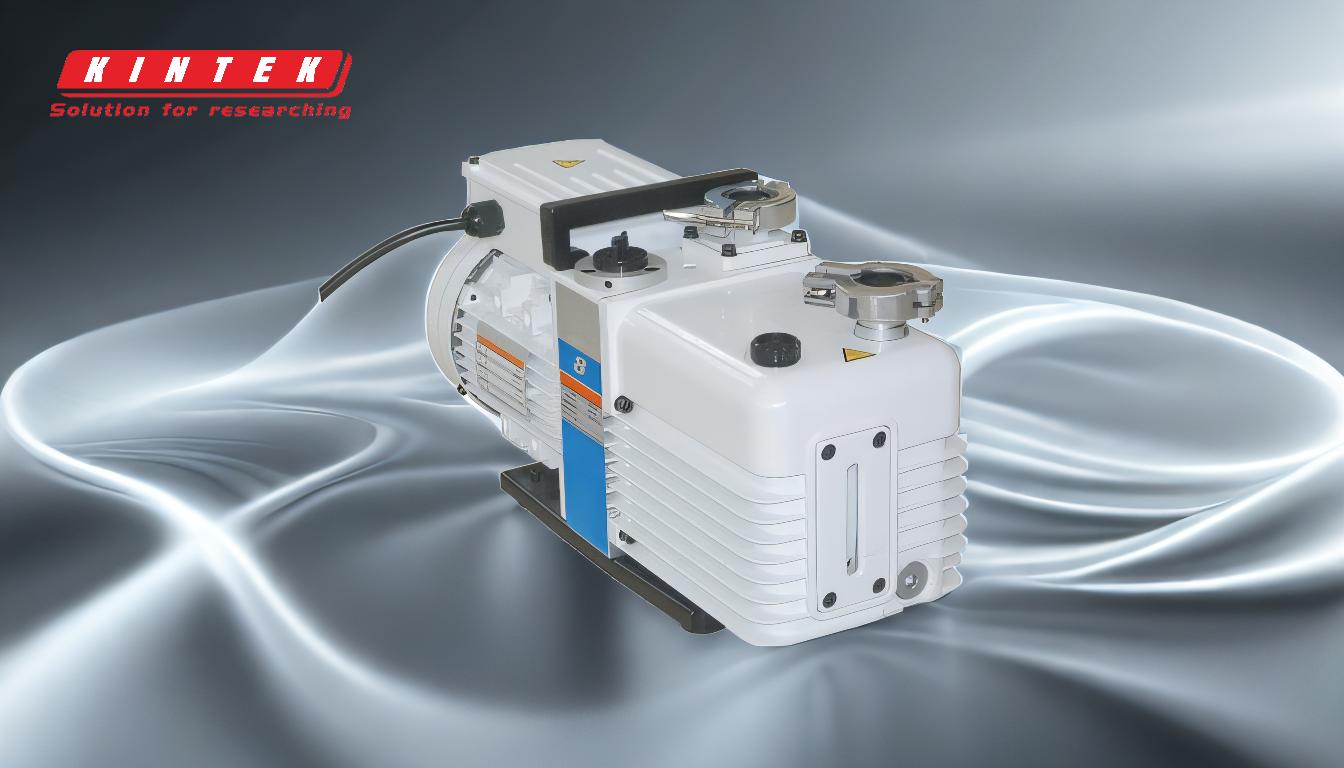
-
Pressure Requirements:
- The vacuum system must be capable of achieving and maintaining the required pressure levels for the specific application. For a vacuum hot press, this typically involves high vacuum levels to ensure proper material processing and bonding.
- The choice of vacuum pumps (e.g., rotary vane, diffusion, or turbomolecular pumps) depends on the desired pressure range and the volume of the chamber.
-
Temperature Control:
- Precise temperature control is crucial, especially in applications like a vacuum hot press where materials are heated under vacuum conditions. The system should include reliable heating elements and temperature sensors to maintain consistent temperatures.
- Consideration should be given to the thermal conductivity of the materials used in the system to minimize heat loss and ensure uniform heating.
-
Material Compatibility:
- The materials used in the construction of the vacuum system must be compatible with the operating environment, including high temperatures and vacuum conditions. Common materials include stainless steel, ceramics, and specific alloys that resist oxidation and outgassing.
- Seals and gaskets should be made from materials that can withstand the vacuum and temperature conditions without degrading.
-
Safety Features:
- Safety is paramount in vacuum system design. Features such as pressure relief valves, auto-cut-off sensors, and emergency shutdown mechanisms should be incorporated to prevent accidents and equipment damage.
- Regular maintenance and monitoring of the system are essential to ensure long-term safety and reliability.
-
Application-Specific Considerations:
- The design of the vacuum system should be tailored to the specific application. For a vacuum hot press, this includes considerations like the size and shape of the press, the materials to be processed, and the required pressure and temperature profiles.
- Integration with other equipment and systems, such as cooling systems or automation controls, should also be considered to enhance overall efficiency and functionality.
By addressing these key points, one can design a vacuum system that not only meets the technical requirements of the application but also ensures safety, reliability, and efficiency. This structured approach helps in making informed decisions and selecting the right components and configurations for the vacuum system.
Summary Table:
Key Considerations | Details |
---|---|
Pressure Requirements | Achieve and maintain required pressure levels; choose appropriate vacuum pumps. |
Temperature Control | Ensure precise heating with reliable elements and sensors for uniform results. |
Material Compatibility | Use materials resistant to high temperatures and vacuum conditions. |
Safety Features | Incorporate pressure relief valves, auto-cut-off sensors, and emergency shutdowns. |
Application-Specific Needs | Tailor design to application requirements, including size, shape, and integration. |
Need help designing a vacuum system for your application? Contact our experts today!