Selecting the right vacuum pump involves evaluating multiple criteria to ensure it meets the specific requirements of your application. Key considerations include the intended use, which dictates the pump's technology, lubrication, chemical resistance, vacuum level, and flow rate. Additionally, factors such as the pump's maximum vacuum, flow rate, motor speed, horsepower, noise level, hose barb size, and net weight are crucial. Other important attributes include the type of pump (oil-free or oil-sealed), gas type application, volume size, life expectancy, and system location. Balancing these factors ensures optimal performance, cost-effectiveness, and longevity of the vacuum pump.
Key Points Explained:
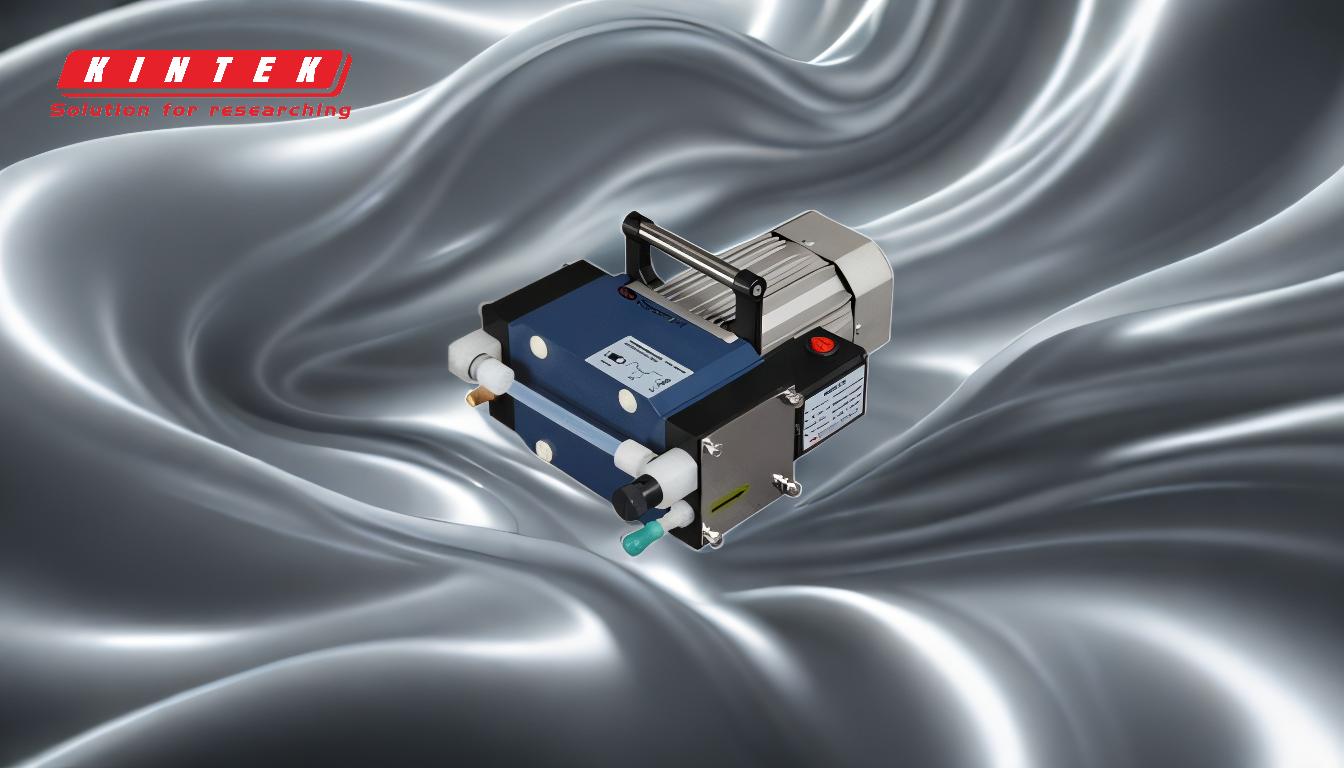
-
Intended Use and Application:
- The primary purpose of the vacuum pump determines the type of technology required. For example, a laboratory setting might need a high-vacuum pump, while an industrial application might require a pump with high flow rates.
- Consider the specific tasks the pump will perform, such as degassing, drying, or material handling, to ensure compatibility with the application.
-
Vacuum Level and Flow Rate:
- Vacuum Level: The maximum vacuum a pump can achieve is critical. Different applications require different vacuum levels, from rough vacuum to ultra-high vacuum.
- Flow Rate: The volume of gas the pump can move per unit of time is essential for applications requiring rapid evacuation or handling large volumes of gas.
-
Pump Type:
- Oil-Sealed vs. Oil-Free: Oil-sealed pumps are typically more robust and can achieve higher vacuum levels, but they require regular maintenance. Oil-free pumps are cleaner and require less maintenance but may have limitations in terms of vacuum level and flow rate.
- Rotary Vane, Diaphragm, Scroll, etc.: Each type of pump has its advantages and disadvantages, depending on the application. For example, rotary vane pumps are durable and can handle a wide range of pressures, while diaphragm pumps are oil-free and ideal for cleanroom environments.
-
Chemical Compatibility:
- The materials used in the pump must be compatible with the gases or vapors they will encounter. For example, corrosive gases require pumps made from chemically resistant materials like stainless steel or PTFE.
-
Lubrication and Maintenance:
- Lubrication: Some pumps require oil for lubrication, which can be a consideration in environments where contamination is a concern.
- Maintenance: The frequency and complexity of maintenance should be considered, especially in applications where downtime is costly.
-
Motor Speed and Horsepower:
- Motor Speed: The speed at which the pump operates can affect its performance and longevity.
- Horsepower: The power of the motor determines the pump's ability to handle demanding applications.
-
Noise Level:
- The noise generated by the pump can be a critical factor, especially in laboratory or office environments where low noise levels are preferred.
-
Hose Barb Size and Net Weight:
- Hose Barb Size: The size of the hose barb must match the system's requirements to ensure proper airflow.
- Net Weight: The weight of the pump can be a consideration in portable or space-constrained applications.
-
Gas Type and Volume Size:
- The type of gas being pumped (e.g., air, vapor, or corrosive gases) and the volume of gas to be handled are critical factors in pump selection.
-
Life Expectancy and System Location:
- Life Expectancy: The expected lifespan of the pump should align with the application's requirements to avoid frequent replacements.
- System Location: The environment where the pump will be installed (e.g., cleanroom, outdoor, or hazardous area) can influence the choice of pump.
-
Cost and Budget:
- The initial cost of the pump, as well as ongoing maintenance and operational costs, should be considered to ensure the pump is economically viable for the application.
By carefully evaluating these criteria, you can select a vacuum pump that not only meets your technical requirements but also aligns with your operational and budgetary constraints.
Summary Table:
Criteria | Key Considerations |
---|---|
Intended Use | Determines pump technology (e.g., high-vacuum for labs, high flow rates for industry). |
Vacuum Level & Flow Rate | Match vacuum level and flow rate to application requirements. |
Pump Type | Oil-sealed vs. oil-free; rotary vane, diaphragm, scroll, etc. |
Chemical Compatibility | Ensure materials resist gases/vapors (e.g., stainless steel for corrosive gases). |
Lubrication & Maintenance | Oil-lubricated or oil-free; maintenance frequency and complexity. |
Motor Speed & Horsepower | Speed and power affect performance and longevity. |
Noise Level | Low noise preferred for labs or offices. |
Hose Barb Size & Weight | Match hose size and consider weight for portability. |
Gas Type & Volume Size | Handle specific gas types and volumes effectively. |
Life Expectancy & Location | Align lifespan and installation environment (e.g., cleanroom, outdoor). |
Cost & Budget | Balance initial cost, maintenance, and operational expenses. |
Need help selecting the perfect vacuum pump? Contact our experts today for personalized advice!