RF sputtering, while a widely used technique for thin film deposition, has several notable disadvantages that can impact its efficiency, cost, and applicability in various scenarios. These drawbacks include low deposition rates, high equipment and operational costs, challenges in achieving uniform coatings, and issues related to heat generation and impurity contamination. Understanding these limitations is crucial for equipment and consumable purchasers to make informed decisions.
Key Points Explained:
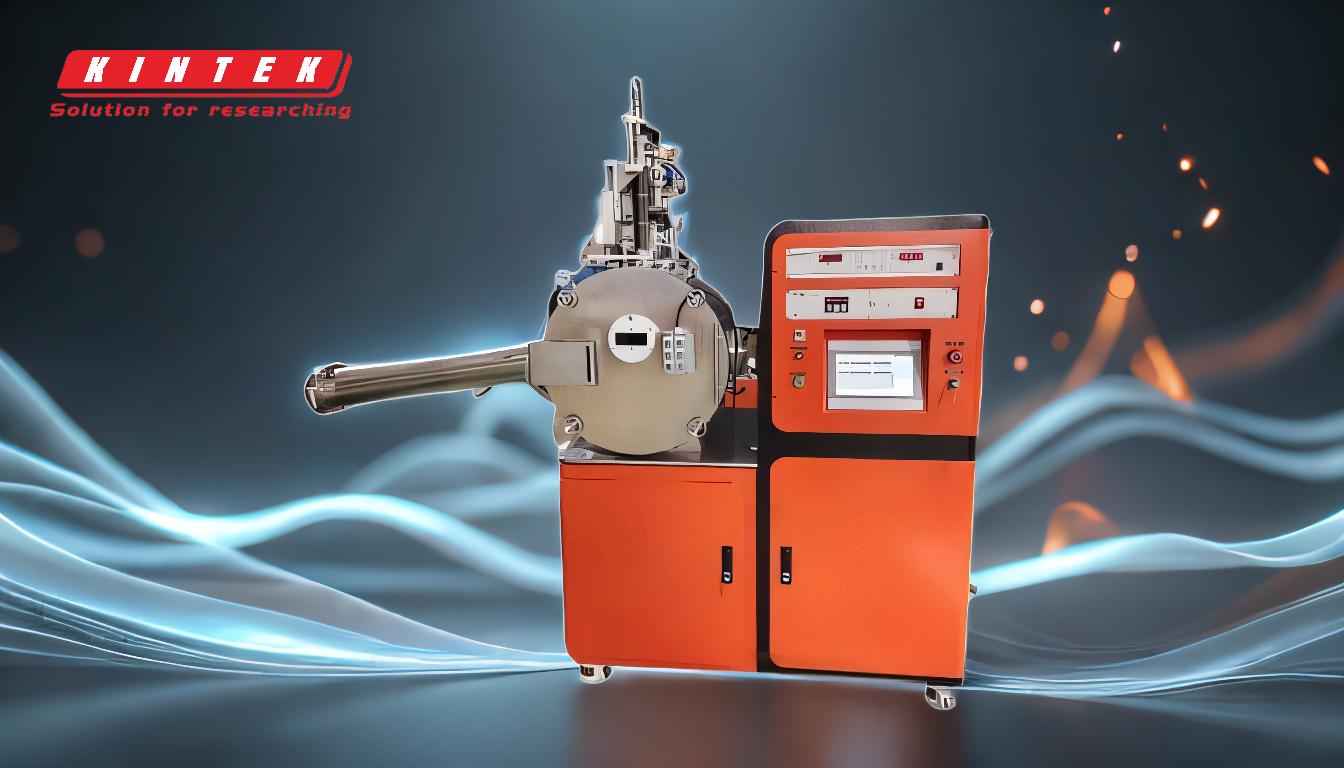
-
Low Deposition Rates:
- RF sputtering often exhibits very low deposition rates, especially for certain materials like SiO2. This can significantly increase the time required to achieve the desired film thickness, making the process less efficient compared to other deposition methods like thermal evaporation.
- The slow deposition speed can be a bottleneck in high-throughput manufacturing environments, where time efficiency is critical.
-
High Capital and Operational Costs:
- RF sputtering systems require expensive RF power supplies and additional impedance matching circuitry, which contribute to high initial capital expenses.
- The need for specialized equipment, such as sputter guns with strong permanent magnets to counteract stray magnetic fields from ferromagnetic targets, further increases system costs.
- Operational costs are also elevated due to the higher power input required to generate radio waves, leading to increased energy consumption.
-
Complexity and Maintenance:
- The complexity of RF sputtering equipment, including high-pressure devices and sophisticated power supplies, makes the system more challenging to operate and maintain.
- The process is sensitive to external factors such as stray magnetic fields, which can disturb the sputtering process and necessitate additional measures to stabilize the system.
-
Heat Generation and Thermal Management:
- A significant portion of the energy incident on the target becomes heat, which must be effectively removed to prevent overheating and maintain process stability.
- Overheating can lead to thermal stress on both the target and the substrate, potentially causing damage or affecting the quality of the deposited film.
-
Uniformity and Adhesion Challenges:
- Achieving uniform film thickness, especially on complex structures like turbine blades, can be difficult due to the non-uniform deposition flux distribution.
- The process may require moving fixtures or additional steps to ensure even coating, which adds to the complexity and cost.
- Adhesion issues can arise, particularly when depositing thick coatings, due to higher internal residual stress levels.
-
Impurity Contamination:
- RF sputtering operates under a lesser vacuum range compared to evaporation, increasing the risk of introducing impurities into the substrate.
- Gaseous contaminants can be activated in the plasma, further elevating the risk of film contamination.
- In reactive sputter deposition, precise control of gas composition is necessary to prevent target poisoning, adding another layer of complexity to the process.
-
Material Degradation and Inefficiency:
- Some materials, particularly organic solids, are susceptible to degradation due to ionic bombardment during the sputtering process.
- Sputtering targets are often expensive, and the process can be inefficient in terms of material use, leading to higher consumable costs.
-
Challenges in Film Structuring:
- Combining RF sputtering with lift-off processes for film structuring is difficult due to the diffuse transport characteristic of sputtering, which makes full shadowing impossible.
- This can lead to contamination problems and complicate the fabrication of structured films.
In summary, while RF sputtering is a versatile and widely used technique, it comes with several disadvantages that can impact its efficiency, cost, and applicability. These include low deposition rates, high capital and operational expenses, complexity in equipment and process control, challenges in achieving uniform and adherent coatings, and risks of impurity contamination and material degradation. Understanding these limitations is essential for making informed decisions in equipment and consumable procurement.
Summary Table:
Disadvantage | Description |
---|---|
Low Deposition Rates | Slow deposition, especially for materials like SiO2, impacting efficiency. |
High Capital & Operational Costs | Expensive RF power supplies, specialized equipment, and increased energy use. |
Complexity & Maintenance | Sensitive to external factors, requiring advanced stabilization measures. |
Heat Generation | Significant heat production necessitates effective thermal management. |
Uniformity & Adhesion Issues | Difficulty in achieving uniform coatings, especially on complex structures. |
Impurity Contamination | Higher risk of introducing impurities due to lesser vacuum range. |
Material Degradation | Organic materials may degrade due to ionic bombardment during sputtering. |
Film Structuring Challenges | Combining with lift-off processes is difficult, leading to contamination risks. |
Need help selecting the right thin film deposition method? Contact our experts today for tailored solutions!