Screw extrusion, particularly twin screw extrusion, is a widely used technology in various industries due to its versatility and efficiency. However, it comes with several disadvantages that need to be carefully considered, especially when making purchasing decisions for equipment and consumables. These disadvantages include high costs, significant space requirements, increased energy consumption, a steep learning curve for operation and maintenance, potential material wastage, and limitations in application range. Understanding these drawbacks is crucial for making informed decisions and optimizing the use of screw extrusion technology.
Key Points Explained:
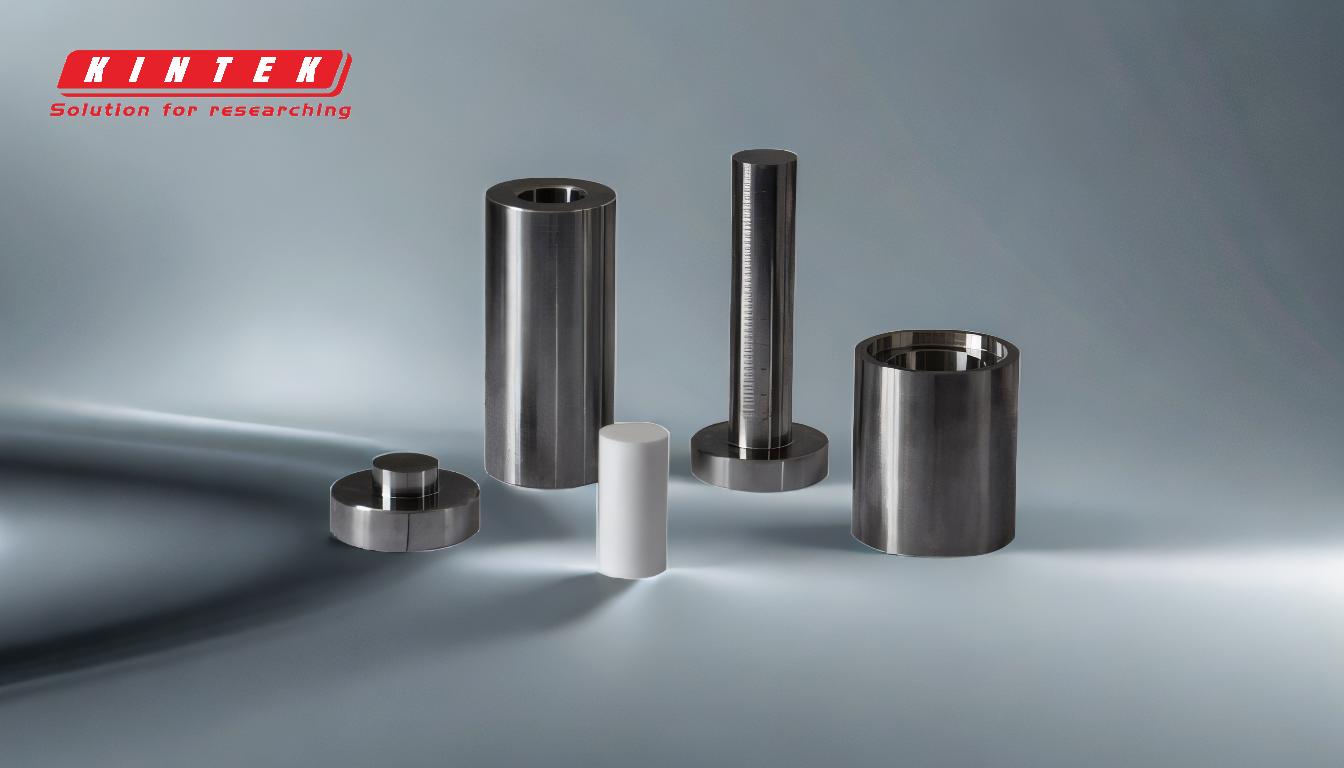
-
Cost Considerations:
- High Initial Investment: Twin screw extruders are generally more expensive than single screw extruders. The initial purchase cost can be a significant barrier, especially for small to medium-sized enterprises.
- Operational Costs: Beyond the initial investment, the operational costs, including maintenance and spare parts, can also be high. This makes it essential to evaluate the total cost of ownership over the equipment's lifespan.
-
Size and Space Requirements:
- Large Footprint: Twin screw extruders typically require more space compared to other types of extruders. This can be a challenge for facilities with limited space.
- Infrastructure Needs: The need for additional infrastructure, such as cooling circulators and material handling equipment, further increases the space requirements.
-
Higher Energy Consumption:
- Energy Intensity: Twin screw extruders consume more energy due to their complex design and the need for precise control over the extrusion process. This can lead to higher utility bills and a larger carbon footprint.
- Efficiency Concerns: While they are efficient in terms of mixing and processing capabilities, the energy consumption per unit of output can be higher compared to simpler extrusion systems.
-
Learning Curve and Maintenance:
- Complex Operation: The operation of twin screw extruders requires specialized knowledge and skills. This can result in a steep learning curve for operators, necessitating extensive training.
- Maintenance Challenges: The complexity of the machinery also means that maintenance can be more demanding. Regular and preventive maintenance is crucial to avoid downtime and costly repairs.
-
Material Wastage:
- Startup and Shutdown Losses: During the startup and shutdown phases, there can be significant material wastage as the system stabilizes. This is particularly problematic when processing expensive or specialized materials.
- Cleaning and Changeover: The need for thorough cleaning between different production runs can also lead to material loss, especially if the residues cannot be reused.
-
Limited Application Range:
- Material Compatibility: While versatile, twin screw extruders may not be suitable for all types of materials. Certain materials may require specific conditions or modifications that are not easily achievable with standard twin screw extruders.
- Process Limitations: Some processes may require capabilities that twin screw extruders cannot provide, such as extremely high temperatures or pressures, limiting their application range.
In conclusion, while twin screw extruders offer numerous advantages, their disadvantages must be carefully weighed against the specific needs and constraints of your operation. Understanding these drawbacks can help in making a more informed decision and in implementing strategies to mitigate their impact.
Summary Table:
Disadvantage | Key Details |
---|---|
High Costs | - High initial investment and operational costs, including maintenance and spare parts. |
Space Requirements | - Large footprint and additional infrastructure needs like cooling systems. |
Energy Consumption | - Higher energy intensity and efficiency concerns compared to simpler systems. |
Learning Curve & Maintenance | - Complex operation requiring specialized skills and demanding maintenance. |
Material Wastage | - Startup/shutdown losses and cleaning/changeover material loss. |
Limited Application Range | - Material compatibility issues and process limitations. |
Need help navigating the challenges of twin screw extrusion? Contact our experts today for tailored solutions!