Single screw extruders, while widely used in various industries, have several notable disadvantages that can impact their efficiency, versatility, and overall performance. These limitations include lower production efficiency, especially with high-viscosity or multi-component materials, which can lead to longer production times and higher operational costs. Additionally, single screw extruders may struggle with mixing and compounding tasks, limiting their ability to handle complex material formulations. Their design also makes them less adaptable to certain applications, such as those requiring precise temperature control or high throughput rates. Understanding these drawbacks is crucial for equipment purchasers to make informed decisions based on their specific production needs.
Key Points Explained:
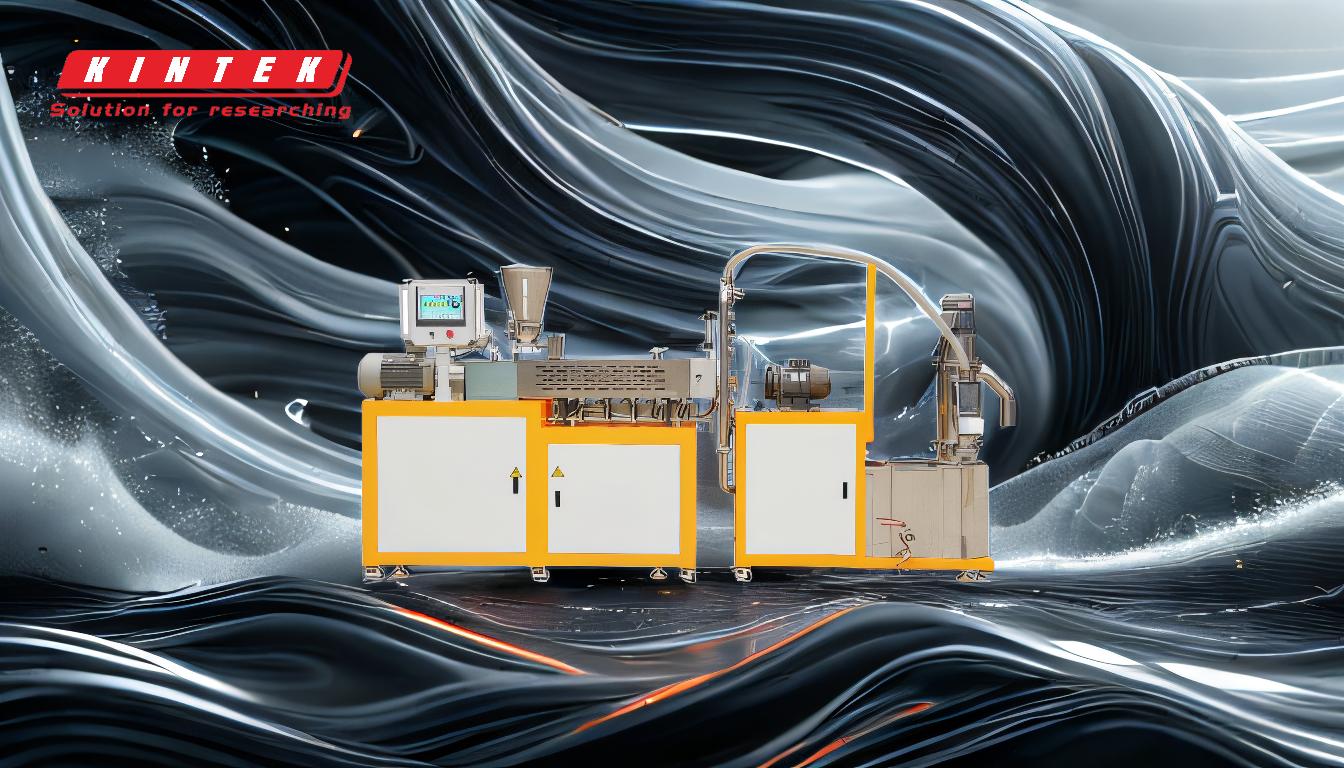
-
Lower Production Efficiency:
- Single screw extruders are generally less efficient compared to twin screw extruders, particularly when processing high-viscosity materials or multi-component blends.
- The lower efficiency stems from the limited shear and mixing capabilities of the single screw design, which can result in uneven material processing and longer cycle times.
- This inefficiency can lead to increased operational costs, as more energy and time are required to achieve the desired output.
-
Challenges with High-Viscosity Materials:
- High-viscosity materials require significant shear and mixing forces to ensure uniform processing, which single screw extruders often struggle to provide.
- The lack of effective mixing can lead to incomplete homogenization, resulting in poor product quality and potential material waste.
- This limitation makes single screw extruders less suitable for applications involving highly viscous polymers or complex formulations.
-
Limited Mixing and Compounding Capabilities:
- Single screw extruders are not ideal for tasks that require thorough mixing or compounding of multiple materials, such as adding fillers, colorants, or additives.
- The absence of intermeshing screws in single screw designs reduces their ability to achieve the high shear rates needed for effective compounding.
- As a result, manufacturers may need to invest in additional equipment or opt for twin screw extruders to meet mixing and compounding requirements.
-
Reduced Adaptability for Complex Applications:
- Single screw extruders are less versatile when it comes to handling specialized applications, such as those requiring precise temperature control, high throughput rates, or advanced material processing.
- Their simpler design limits their ability to adapt to varying production demands, making them less suitable for industries that require flexibility and precision.
- For example, industries like pharmaceuticals or advanced materials may find single screw extruders inadequate for their needs.
-
Operational and Maintenance Challenges:
- The inefficiencies and limitations of single screw extruders can lead to increased wear and tear, requiring more frequent maintenance and higher downtime.
- Operational challenges, such as difficulty in achieving consistent product quality, can also result in higher costs and reduced productivity over time.
- These factors make single screw extruders less cost-effective in the long run for certain applications.
-
Comparison with Twin Screw Extruders:
- Twin screw extruders offer several advantages over single screw extruders, including better mixing, higher throughput, and greater adaptability to complex materials.
- While twin screw extruders may have a higher initial cost, their superior performance and efficiency often justify the investment for applications requiring advanced processing capabilities.
- Purchasers should carefully evaluate their production needs to determine whether the benefits of twin screw extruders outweigh the lower upfront cost of single screw models.
By understanding these disadvantages, equipment purchasers can make more informed decisions and select the extruder type that best aligns with their production requirements and long-term goals.
Summary Table:
Disadvantage | Impact |
---|---|
Lower Production Efficiency | Longer cycle times, higher operational costs, and uneven material processing. |
Challenges with High-Viscosity Materials | Poor homogenization, material waste, and unsuitability for viscous polymers. |
Limited Mixing and Compounding | Ineffective for adding fillers, colorants, or achieving high shear rates. |
Reduced Adaptability | Less suitable for precise temperature control, high throughput, or advanced materials. |
Operational and Maintenance Challenges | Increased wear, frequent maintenance, and higher downtime. |
Comparison with Twin Screw Extruders | Twin screws offer better mixing, higher throughput, and greater adaptability. |
Need help choosing the right extruder for your production needs? Contact our experts today for personalized advice!