Twin screw extruders, while highly efficient and versatile, come with several disadvantages that potential buyers should consider. The primary drawbacks include higher costs, both in terms of initial investment and maintenance, due to their complex design and engineering. Additionally, they may require more skilled operators and have higher energy consumption compared to single screw extruders. These factors can impact the overall feasibility and operational efficiency of using twin screw extruders in various industrial applications.
Key Points Explained:
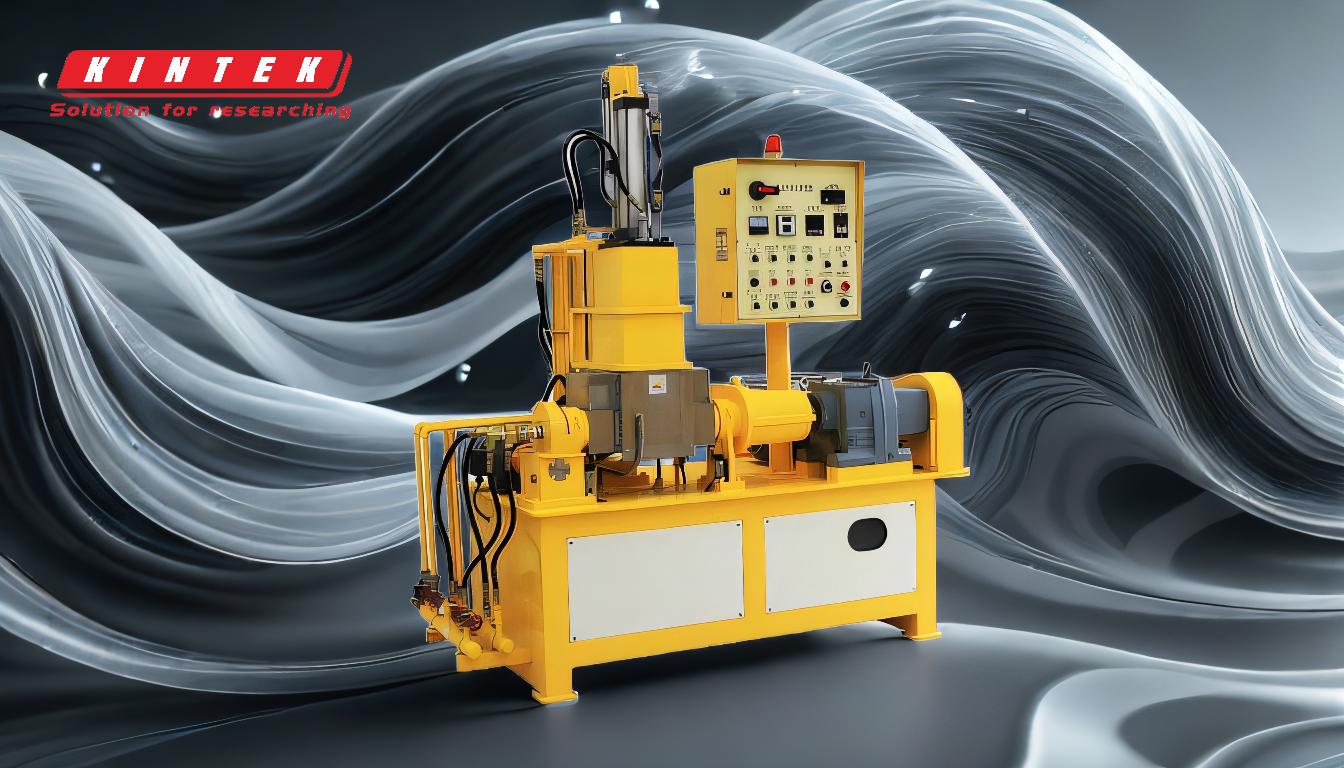
-
Higher Initial Cost
- Twin screw extruders are significantly more expensive to purchase than single screw extruders.
- The intricate design, precision engineering, and advanced materials used in their construction contribute to the higher price.
- This makes them less accessible for smaller businesses or operations with limited budgets.
-
Increased Maintenance Costs
- The complexity of twin screw extruders means they require more frequent and specialized maintenance.
- Components such as screws, barrels, and seals are subject to wear and tear, necessitating regular inspections and replacements.
- Maintenance often requires skilled technicians, adding to operational expenses.
-
Higher Energy Consumption
- Twin screw extruders generally consume more energy compared to single screw extruders.
- The advanced mixing and processing capabilities come at the cost of increased power usage, which can lead to higher utility bills.
- This may be a concern for businesses aiming to reduce their carbon footprint or operating in regions with high energy costs.
-
Requirement for Skilled Operators
- Operating twin screw extruders requires a higher level of expertise compared to single screw models.
- The complexity of the machine and its processes demands trained personnel to ensure optimal performance and avoid costly errors.
- This can lead to additional training costs or the need to hire specialized staff.
-
Limited Applications for Simple Processes
- Twin screw extruders are designed for complex mixing, compounding, and processing tasks.
- For simpler applications, their advanced features may be unnecessary, making them less cost-effective compared to single screw extruders.
- This limits their practicality in industries where basic extrusion processes are sufficient.
-
Space and Installation Requirements
- Twin screw extruders often require more floor space due to their larger size and additional components.
- Installation can be more complex, potentially requiring modifications to existing facilities.
- This may pose challenges for businesses with limited space or infrastructure.
-
Potential for Over-Engineering
- In some cases, the advanced capabilities of twin screw extruders may exceed the needs of the application.
- This over-engineering can lead to inefficiencies, as the machine may not be utilized to its full potential.
- It’s important to carefully assess whether the additional features justify the investment for a specific use case.
In summary, while twin screw extruders offer superior performance for complex processing tasks, their higher costs, maintenance requirements, and operational demands make them less suitable for simpler applications or businesses with limited resources. Careful consideration of these disadvantages is essential when deciding whether to invest in this type of equipment.
Summary Table:
Disadvantage | Details |
---|---|
Higher Initial Cost | More expensive due to complex design, precision engineering, and advanced materials. |
Increased Maintenance Costs | Requires frequent, specialized maintenance and skilled technicians. |
Higher Energy Consumption | Consumes more power, leading to higher utility bills and environmental concerns. |
Skilled Operators Needed | Demands trained personnel, increasing operational costs and training requirements. |
Limited for Simple Processes | Over-engineered for basic tasks, making single screw extruders more cost-effective. |
Space and Installation | Requires more floor space and complex installation, challenging for smaller facilities. |
Potential Over-Engineering | Advanced features may not be fully utilized, leading to inefficiencies. |
Need help deciding if a twin screw extruder is right for your business? Contact our experts today for personalized advice!