Vacuum pumps are essential in various industrial and scientific applications, but they come with several disadvantages that can impact their efficiency, maintenance, and operational costs. These disadvantages include high energy consumption, sensitivity to contaminants, maintenance requirements, and limitations in achieving ultra-high vacuum levels. Understanding these drawbacks is crucial for users to make informed decisions, especially in applications like the vacuum hot press, where vacuum quality and system reliability are critical.
Key Points Explained:
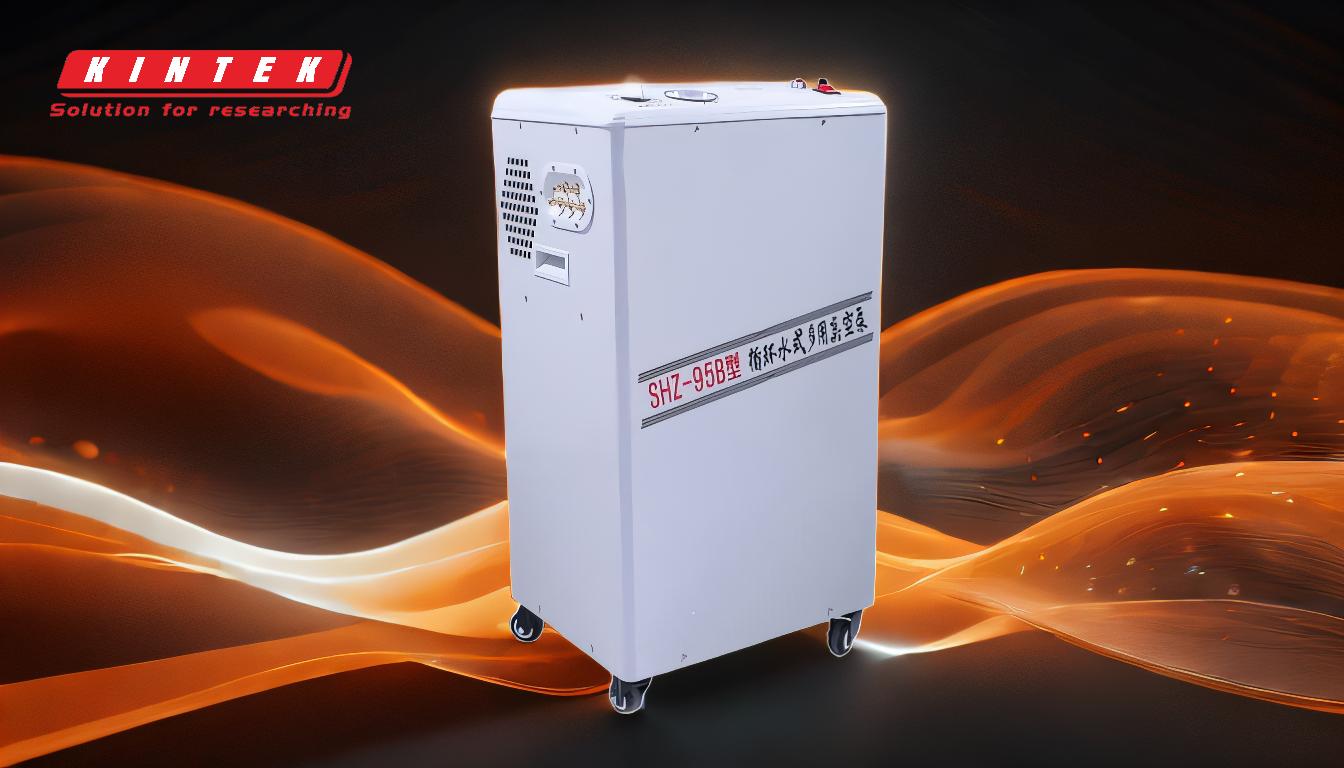
-
High Energy Consumption:
- Vacuum pumps, especially those used in high-performance applications, require significant energy to operate. This is particularly true for pumps that need to maintain a consistent vacuum level over extended periods. The energy cost can be a significant factor in the overall operational expenses, especially in large-scale industrial setups.
-
Sensitivity to Contaminants:
- Vacuum pumps are highly sensitive to contaminants such as dust, moisture, and other particulates. These contaminants can cause wear and tear on the pump's internal components, leading to reduced efficiency and potential breakdowns. For example, in a vacuum hot press, any contamination can affect the quality of the material being processed, leading to defects or suboptimal results.
-
Maintenance Requirements:
- Regular maintenance is essential to keep vacuum pumps operating efficiently. This includes routine cleaning, replacement of worn-out parts, and monitoring of oil levels (in oil-sealed pumps). The maintenance process can be time-consuming and costly, particularly for pumps that operate continuously or in harsh environments.
-
Limitations in Achieving Ultra-High Vacuum Levels:
- While vacuum pumps are effective in creating a vacuum, achieving ultra-high vacuum levels (below 10^-7 Torr) can be challenging. Specialized pumps and additional equipment, such as cryogenic traps or turbo-molecular pumps, may be required to reach these levels. This adds complexity and cost to the system, making it less practical for some applications.
-
Noise and Vibration:
- Some vacuum pumps, particularly rotary vane and piston pumps, can generate significant noise and vibration during operation. This can be a concern in environments where noise levels need to be minimized, such as laboratories or medical facilities. The noise and vibration can also lead to mechanical fatigue over time, further increasing maintenance needs.
-
Temperature Sensitivity:
- The efficiency of vacuum pumps can be affected by temperature variations. For instance, in liquid ring vacuum pumps, the temperature of the service liquid directly impacts the pump's performance. Higher temperatures can reduce the pump's capacity and vacuum pressure, as mentioned in the reference about the efficiency of liquid ring vacuum pumps. This sensitivity necessitates additional cooling systems, which can further complicate the setup and increase operational costs.
-
Initial Cost and Complexity:
- High-quality vacuum pumps, especially those designed for specialized applications, can be expensive to purchase and install. Additionally, integrating a vacuum pump into a larger system, such as a vacuum hot press, often requires additional components like vacuum valves, measuring instruments, and pipelines. This increases the overall complexity and cost of the system.
-
Environmental Concerns:
- Some vacuum pumps, particularly oil-sealed pumps, can pose environmental risks due to the potential for oil leaks or the release of harmful vapors. Proper disposal of used oil and adherence to environmental regulations are necessary, adding to the operational burden.
In conclusion, while vacuum pumps are indispensable in many applications, their disadvantages must be carefully considered. Users should evaluate their specific needs, such as the required vacuum level, operational environment, and maintenance capabilities, to choose the most suitable pump and mitigate potential drawbacks.
Summary Table:
Disadvantage | Description |
---|---|
High Energy Consumption | Significant energy required for operation, increasing operational costs. |
Sensitivity to Contaminants | Dust, moisture, and particulates can damage components and reduce efficiency. |
Maintenance Requirements | Regular cleaning, part replacement, and oil monitoring are time-consuming. |
Ultra-High Vacuum Limitations | Achieving ultra-high vacuum levels requires specialized, costly equipment. |
Noise and Vibration | Some pumps generate noise and vibration, impacting environments and maintenance. |
Temperature Sensitivity | Performance varies with temperature, often requiring additional cooling systems. |
Initial Cost and Complexity | High purchase and installation costs, with added system integration complexity. |
Environmental Concerns | Oil-sealed pumps may pose environmental risks due to leaks or harmful vapors. |
Need help selecting the right vacuum pump for your application? Contact our experts today!