Sieve shakers are essential tools in particle size analysis, and their proper use requires adherence to specific precautions to ensure accurate and reliable results. Key precautions include selecting the appropriate sieve shaker for the material being tested, ensuring the sample does not undergo changes during wet sieving, and maintaining the equipment properly. These steps help prevent errors, preserve sample integrity, and extend the lifespan of the sieve shaker. Below, we explore these precautions in detail, focusing on material compatibility, wet sieving considerations, and equipment maintenance.
Key Points Explained:
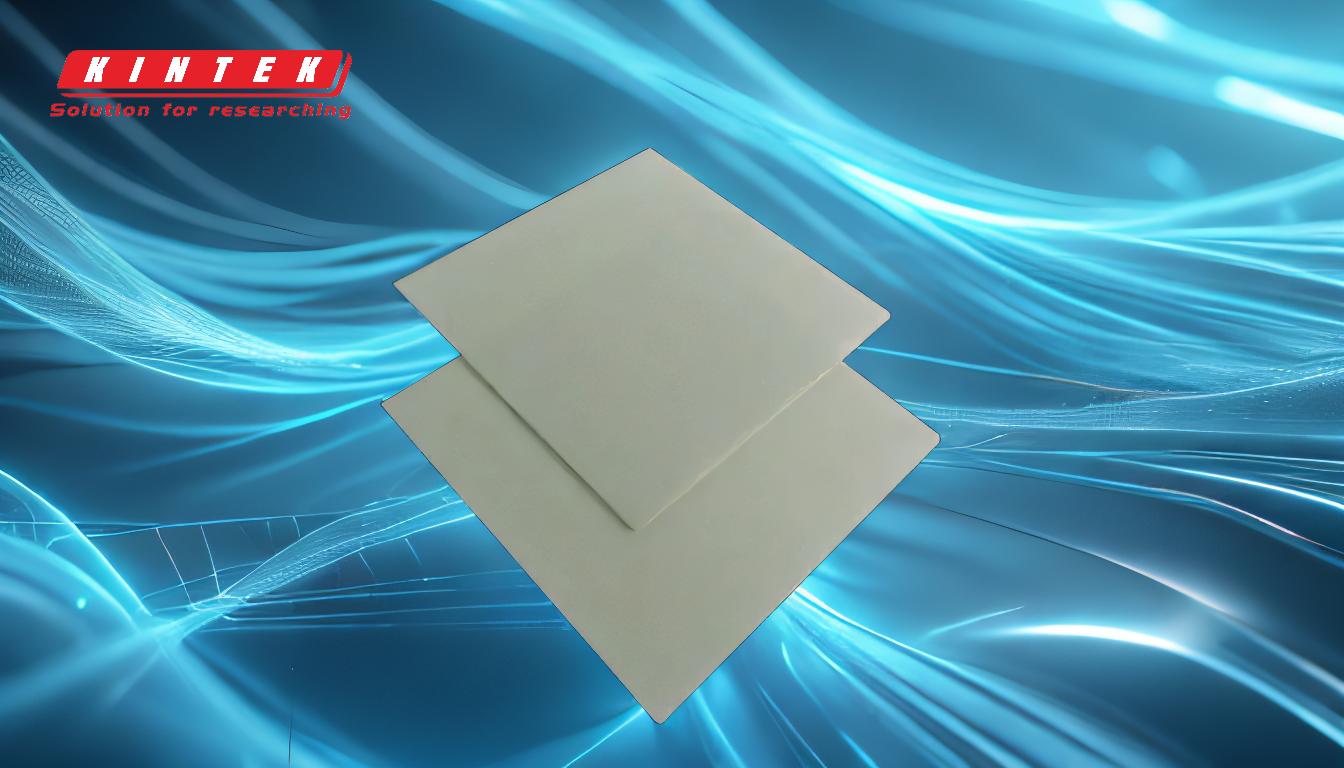
-
Material Compatibility:
- Match the Sieve Shaker to the Material: Different sieve shakers are designed for specific types of materials, such as coarse aggregates, fine powders, or granular substances. Using the wrong type of shaker can lead to inaccurate results or damage to the equipment.
- Consider Sieve Diameter: The diameter of the sieves must align with the shaker's specifications. Mismatched sizes can cause improper agitation or sieving, affecting the analysis.
-
Wet Sieving Precautions:
- Prevent Sample Alteration: During wet sieving, ensure the sample does not swell, dissolve, or react with the liquid. Such changes can distort the particle size distribution and compromise the accuracy of the results.
- Use Appropriate Liquids: Select a liquid that is chemically compatible with the sample to avoid unwanted reactions or degradation.
- Control Sieving Time: Prolonged wet sieving can lead to sample degradation or excessive wear on the sieves. Follow recommended time limits for the specific material being tested.
-
Equipment Maintenance:
- Regular Cleaning: Clean the sieve shaker and sieves after each use to prevent cross-contamination and buildup of residues that can affect future analyses.
- Inspect for Wear and Damage: Regularly check the sieves and shaker components for signs of wear, such as mesh tears or frame deformities. Replace damaged parts promptly to maintain accuracy.
- Calibration: Periodically calibrate the sieve shaker to ensure consistent performance and adherence to industry standards.
-
Operational Best Practices:
- Secure Sieve Stacking: Ensure the sieves are properly stacked and securely fastened in the shaker to prevent misalignment or spillage during operation.
- Avoid Overloading: Do not overload the sieves with excessive sample material, as this can hinder proper sieving and lead to inaccurate results.
- Monitor Vibration Intensity: Adjust the vibration intensity according to the material being tested. Excessive vibration can damage delicate samples or sieves, while insufficient vibration may result in incomplete sieving.
By following these precautions, users can maximize the accuracy of their sieve analysis, extend the lifespan of their equipment, and ensure consistent, reliable results. Proper selection, handling, and maintenance of sieve shakers are critical for achieving optimal performance in particle size analysis.
Summary Table:
Precaution | Key Considerations |
---|---|
Material Compatibility | Match shaker to material type, ensure sieve diameter aligns with shaker specifications. |
Wet Sieving | Prevent sample alteration, use compatible liquids, control sieving time. |
Equipment Maintenance | Clean regularly, inspect for wear, calibrate periodically. |
Operational Practices | Secure sieve stacking, avoid overloading, monitor vibration intensity. |
Maximize your sieve analysis accuracy—contact our experts today for tailored advice!