Blending metal powders is a critical process in various industries, including additive manufacturing, metallurgy, and powder metallurgy. Proper precautions must be taken to ensure safety, maintain powder quality, and achieve a homogeneous blend. Key considerations include preventing contamination, controlling environmental conditions, ensuring operator safety, and using appropriate blending equipment. Additionally, understanding the properties of the metal powders, such as particle size, density, and reactivity, is essential to avoid issues like segregation, oxidation, or ignition. By following best practices, such as using inert atmospheres, adhering to safety protocols, and selecting the right blending techniques, the process can be optimized for efficiency and safety.
Key Points Explained:
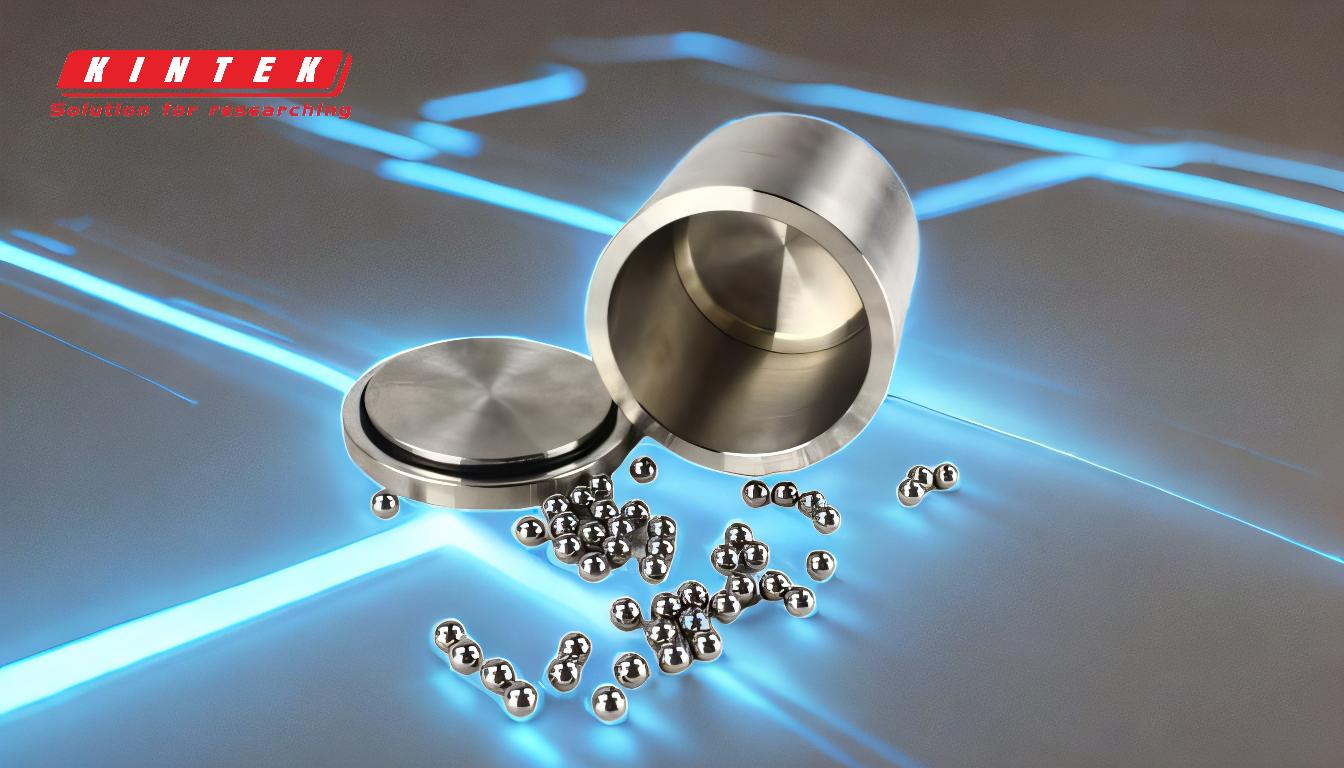
-
Preventing Contamination:
- Metal powders are highly sensitive to contamination, which can compromise the final product's quality. Ensure that blending equipment is thoroughly cleaned before use to avoid cross-contamination from previous batches.
- Use dedicated tools and containers for specific powder types to prevent mixing of incompatible materials.
- Work in a cleanroom or controlled environment to minimize exposure to dust, moisture, and other contaminants.
-
Controlling Environmental Conditions:
- Metal powders are often reactive and can oxidize or absorb moisture if exposed to air. Conduct blending in an inert atmosphere, such as argon or nitrogen, to prevent oxidation.
- Maintain proper humidity and temperature levels in the blending area to avoid clumping or degradation of the powders.
- Use sealed containers or glove boxes when handling highly reactive powders like aluminum or titanium.
-
Ensuring Operator Safety:
- Metal powders, especially fine particles, can pose health risks if inhaled or come into contact with skin. Operators should wear appropriate personal protective equipment (PPE), including respirators, gloves, and protective clothing.
- Implement proper ventilation systems to reduce the risk of airborne particles.
- Provide training on handling hazardous materials and emergency procedures in case of spills or exposure.
-
Selecting Appropriate Blending Equipment:
- Choose blending equipment that matches the specific requirements of the metal powders. Common options include tumble blenders, V-blenders, and high-shear mixers.
- Ensure the equipment is made from materials that do not react with the powders, such as stainless steel or ceramic-lined containers.
- Regularly inspect and maintain equipment to prevent wear and tear that could introduce contaminants or affect blending efficiency.
-
Understanding Powder Properties:
- Different metal powders have varying particle sizes, densities, and flow characteristics, which can affect blending. For example, fine powders may segregate or form agglomerates, while coarse powders may require longer blending times.
- Conduct pre-blending tests to determine the optimal blending time, speed, and technique for achieving a homogeneous mixture.
- Consider using flow agents or binders if the powders have poor flow properties.
-
Minimizing Segregation:
- Segregation occurs when particles of different sizes or densities separate during blending. To minimize this, use blending techniques that promote uniform mixing, such as tumbling or fluidization.
- Avoid over-blending, as excessive mixing can lead to particle attrition or segregation.
- Store blended powders in a way that prevents settling or separation, such as in sealed, vibration-free containers.
-
Handling Reactive Powders:
- Some metal powders, such as magnesium, titanium, or aluminum, are highly reactive and can ignite or explode if exposed to air or moisture. Handle these powders with extreme caution.
- Use explosion-proof equipment and conduct blending in a controlled environment with fire suppression systems in place.
- Follow strict safety protocols, including grounding equipment to prevent static discharge, which can ignite reactive powders.
-
Quality Control and Testing:
- After blending, perform quality control tests to ensure the mixture is homogeneous and meets the required specifications. Common tests include particle size analysis, density measurements, and chemical composition analysis.
- Document the blending process parameters, such as time, speed, and environmental conditions, for traceability and consistency.
- Address any deviations or inconsistencies promptly to maintain product quality.
By adhering to these precautions, the blending of metal powders can be conducted safely and effectively, ensuring high-quality results and minimizing risks to both operators and equipment.
Summary Table:
Key Precautions | Details |
---|---|
Prevent Contamination | Clean equipment, use dedicated tools, and work in controlled environments. |
Control Environmental Conditions | Use inert atmospheres, maintain humidity/temperature, and handle reactive powders carefully. |
Ensure Operator Safety | Use PPE, proper ventilation, and provide training for hazardous materials. |
Select Blending Equipment | Choose compatible equipment (e.g., tumble blenders) and maintain regularly. |
Understand Powder Properties | Consider particle size, density, and flow characteristics for optimal blending. |
Minimize Segregation | Use uniform mixing techniques and avoid over-blending. |
Handle Reactive Powders | Use explosion-proof equipment and follow strict safety protocols. |
Quality Control and Testing | Perform tests (e.g., particle size analysis) and document process parameters. |
Need expert advice on blending metal powders safely? Contact us today for tailored solutions!