A colloidal mill is a specialized machine used for particle size reduction, emulsification, homogenization, and dispersion of materials, particularly in industries such as pharmaceuticals, food, chemicals, and cosmetics. It operates on the rotor-stator principle, where a rapidly rotating rotor and a stationary stator create a high-shear environment in a narrow gap. This process breaks down solid particles into a liquid medium, resulting in superfine grinding and the creation of stable suspensions, emulsions, or dispersions. Colloidal mills are versatile, capable of handling highly viscous materials, and are available in various sizes, including compact lab models for research and development. They are essential for producing colloidal dispersions, suspensions, and emulsions in industries requiring precise particle size control and uniformity.
Key Points Explained:
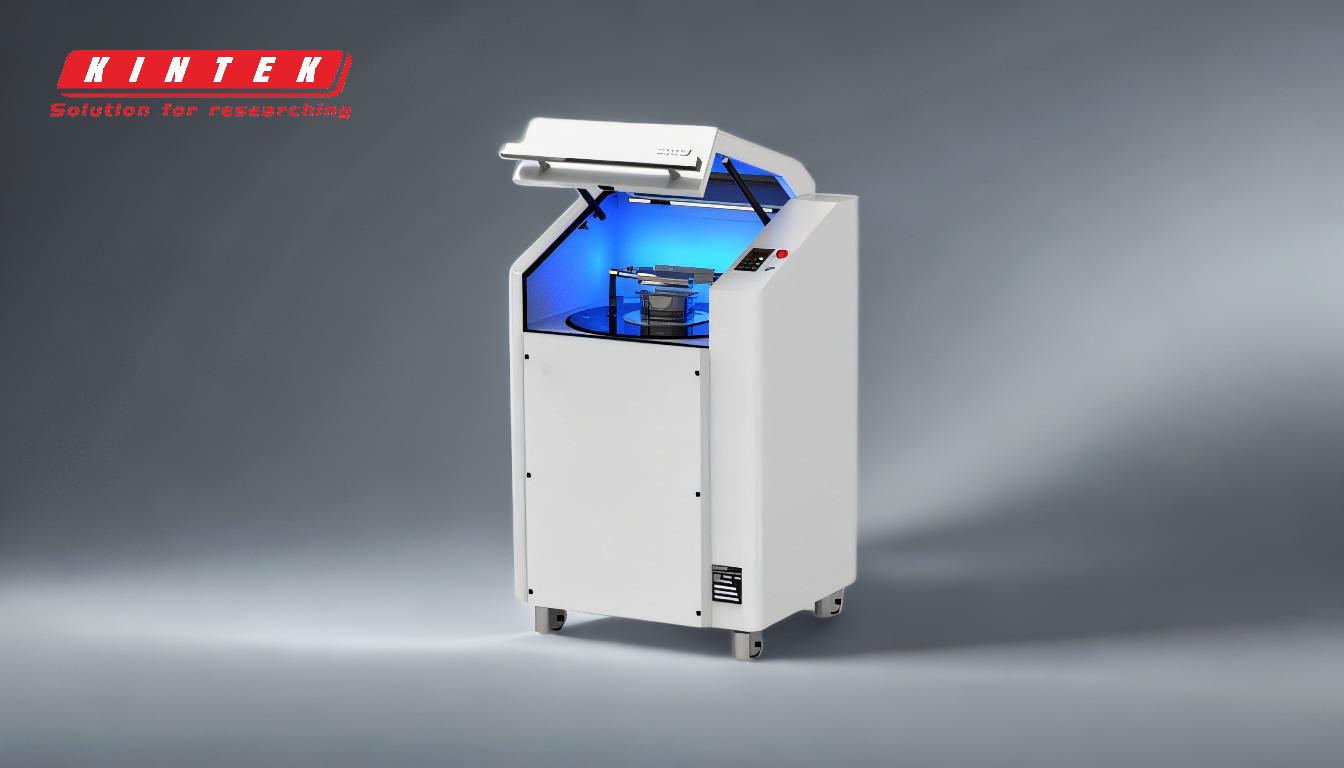
-
Principle of Operation:
- The colloidal mill operates on the rotor-stator principle.
- A rapidly rotating cone (rotor) and a stationary cone (stator) create a narrow gap where materials are subjected to intense shearing forces.
- This high-shear environment breaks down solid particles into a liquid medium, achieving superfine grinding and dispersion.
-
Functions and Capabilities:
- Particle Size Reduction: Reduces solid materials into fine particles within a liquid medium.
- Emulsification: Creates stable emulsions by dispersing one liquid into another.
- Homogenization: Ensures uniform distribution of particles or droplets in a liquid.
- Dispersion: Breaks down agglomerates and disperses solids evenly in a liquid.
- These functions are often achieved simultaneously in a single process cycle, making the colloidal mill highly efficient.
-
Applications Across Industries:
- Pharmaceutical Industry: Used for preparing colloidal dispersions, suspensions, emulsions, and ointments. Ideal for tablet batching systems.
- Food and Beverage Industry: Utilized for homogenizing and emulsifying products like dairy, sauces, and confectionery.
- Chemical Industry: Helps in creating stable chemical dispersions and suspensions.
- Cosmetics and Detergents: Used for producing creams, lotions, and detergent formulations.
- Other Industries: Includes rubber, paint, textile, meat processing, starch, and paper industries.
-
Types of Colloidal Mills:
- Industrial Colloidal Mills: Designed for large-scale production in industries like pharmaceuticals, food, and chemicals.
- Lab Colloidal Mills (R&D Colloid Mills): Compact and small-sized mills used in laboratories for research and development purposes. These are also known as Mini Colloid Mills or Compact Colloid Mills.
-
Advantages:
- Versatility: Capable of handling a wide range of materials, including highly viscous substances.
- Efficiency: Achieves multiple processes (grinding, emulsifying, homogenizing, dispersing) in a single cycle.
- Precision: Provides superfine grinding and uniform particle size distribution.
- Scalability: Suitable for small, medium, and large-scale production.
-
Key Components:
- Rotor: The rotating part that generates the shearing force.
- Stator: The stationary part that works in tandem with the rotor to create the narrow gap for shearing.
- Gap Adjustment Mechanism: Allows precise control over the gap between the rotor and stator, influencing the fineness of the grind.
- Cooling System: Often included to prevent overheating during the processing of heat-sensitive materials.
-
Material Compatibility:
- Colloidal mills are designed to handle a variety of materials, including:
- Solids that are not easily moistened by the dispersion medium.
- Highly viscous liquids.
- Heat-sensitive materials (with cooling systems in place).
- Colloidal mills are designed to handle a variety of materials, including:
-
Importance in Research and Development:
- Lab colloidal mills are critical for R&D in industries like pharmaceuticals and food. They allow researchers to test and develop new formulations on a small scale before scaling up to industrial production.
-
Maintenance and Durability:
- Colloidal mills are built to withstand high-shear operations and are often made from durable materials like stainless steel to ensure longevity and ease of cleaning.
-
Future Trends:
- Advancements in colloidal mill technology focus on improving energy efficiency, reducing maintenance requirements, and enhancing precision in particle size reduction and dispersion.
In summary, a colloidal mill is a versatile and efficient machine essential for industries requiring precise particle size reduction, emulsification, homogenization, and dispersion. Its rotor-stator design, combined with its ability to handle a wide range of materials, makes it indispensable in pharmaceuticals, food, chemicals, and cosmetics. Whether for industrial production or laboratory research, colloidal mills offer a reliable solution for achieving uniform and stable product formulations.
Summary Table:
Aspect | Details |
---|---|
Principle of Operation | Rotor-stator system creating high-shear forces for superfine grinding. |
Key Functions | Particle size reduction, emulsification, homogenization, and dispersion. |
Applications | Pharmaceuticals, food, chemicals, cosmetics, and more. |
Types | Industrial and lab (R&D) colloidal mills. |
Advantages | Versatile, efficient, precise, and scalable. |
Key Components | Rotor, stator, gap adjustment mechanism, and cooling system. |
Material Compatibility | Handles solids, viscous liquids, and heat-sensitive materials. |
Ready to enhance your production process? Contact us today to learn more about colloidal mills!