A sputter coater is a specialized device used in materials science and microscopy to deposit thin layers of conductive materials onto non-conductive samples. This process is particularly crucial for scanning electron microscopy (SEM) applications, where it enhances sample conductivity and secondary electron emission, enabling high-resolution imaging. The sputtering process involves bombarding a target material with high-energy ions, converting it into a vapor that deposits onto the sample. Key parameters such as sputter current, voltage, vacuum pressure, and target material significantly influence the quality and efficiency of the coating. Sputter coaters are indispensable for preparing samples for SEM, ensuring accurate imaging and analysis.
Key Points Explained:
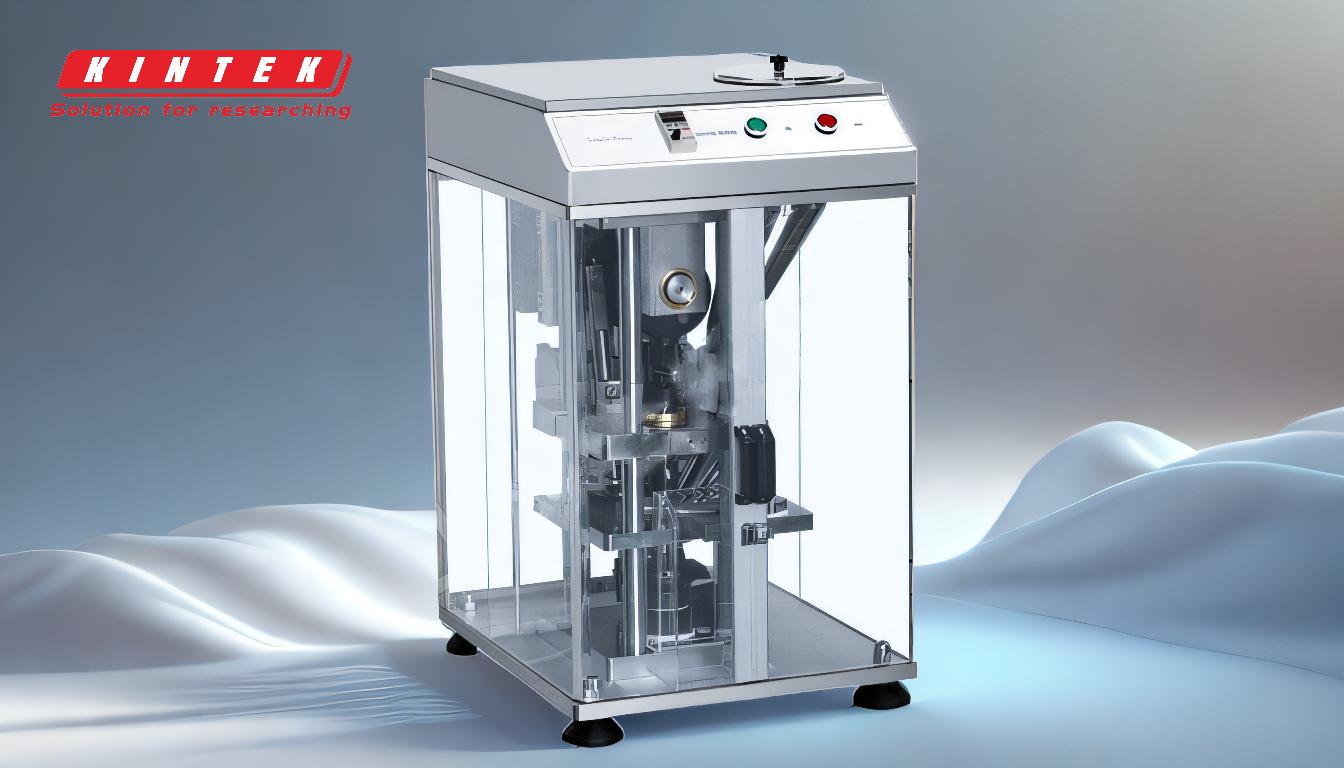
-
Purpose and Applications of a Sputter Coater:
- Sputter coaters are primarily used to coat non-conductive samples with thin layers of conductive materials like gold or platinum. This is essential for SEM imaging, as it prevents charging effects and enhances secondary electron emission, improving image resolution.
- For example, the Kintek gold sputter coater is designed for applications requiring magnification up to 100,000x, making it ideal for high-resolution SEM analysis.
-
How Sputtering Works:
- Sputtering is a physical vapor deposition (PVD) technique where a target material is bombarded with high-energy ions, causing atoms to be ejected and deposited onto a sample.
- This process transforms the solid target material into a fine spray of microscopic particles, creating a thin, uniform coating on the sample.
-
Key Parameters Influencing the Sputter Process:
- Sputter Current and Voltage: These determine the energy of the ions bombarding the target, affecting the deposition rate and coating quality.
- Vacuum Pressure: A controlled vacuum environment ensures efficient sputtering and prevents contamination.
- Target-to-Sample Distance: This influences the uniformity and thickness of the coating.
- Target Material and Thickness: High-purity materials with uniform grain size are essential for consistent and high-quality coatings.
- Sputter Gas: Inert gases like argon are commonly used to facilitate the sputtering process.
-
Advantages of Sputter Coating for SEM:
- Improved Conductivity: Metal coatings provide a conduction path, dissipating heat and minimizing beam damage during SEM imaging.
- Enhanced Secondary Electron Yield: This improves the signal-to-noise ratio, resulting in clearer and more detailed images.
- Versatility: Sputter coaters can handle a wide range of sample materials, making them suitable for diverse applications.
-
Challenges and Considerations:
- Heat Management: The sputtering process generates significant heat, requiring specialized chilling systems to maintain optimal conditions.
- Target Requirements: High purity and uniformity of the target material are critical to achieving consistent and high-quality coatings.
By understanding these key points, purchasers can evaluate sputter coaters based on their specific needs, ensuring they select a device that delivers the desired performance and results for their applications.
Summary Table:
Aspect | Details |
---|---|
Purpose | Coats non-conductive samples with conductive materials for SEM imaging. |
Key Applications | Enhances conductivity, prevents charging, and improves image resolution. |
Sputtering Process | Bombards target material with ions, creating a thin, uniform coating. |
Key Parameters | Sputter current, voltage, vacuum pressure, target material, and gas type. |
Advantages | Improved conductivity, enhanced electron yield, and versatility. |
Challenges | Heat management and high-purity target requirements. |
Ready to optimize your SEM imaging? Contact us today to find the perfect sputter coater for your lab!