A two-high roll mill, also known as a two-roll mill, is a versatile piece of equipment used primarily in the rubber, plastic, and polymer industries for mixing, compounding, and testing materials. It consists of two horizontally aligned rollers that rotate in opposite directions, creating friction and shearing forces to mix or process materials like rubber, plastics, and pigments. The rollers can be adjusted to control the gap between them, allowing for precise material processing. This machine is widely used in material development, quality control, and educational purposes due to its ability to generate consistent results and uniform mixing.
Key Points Explained:
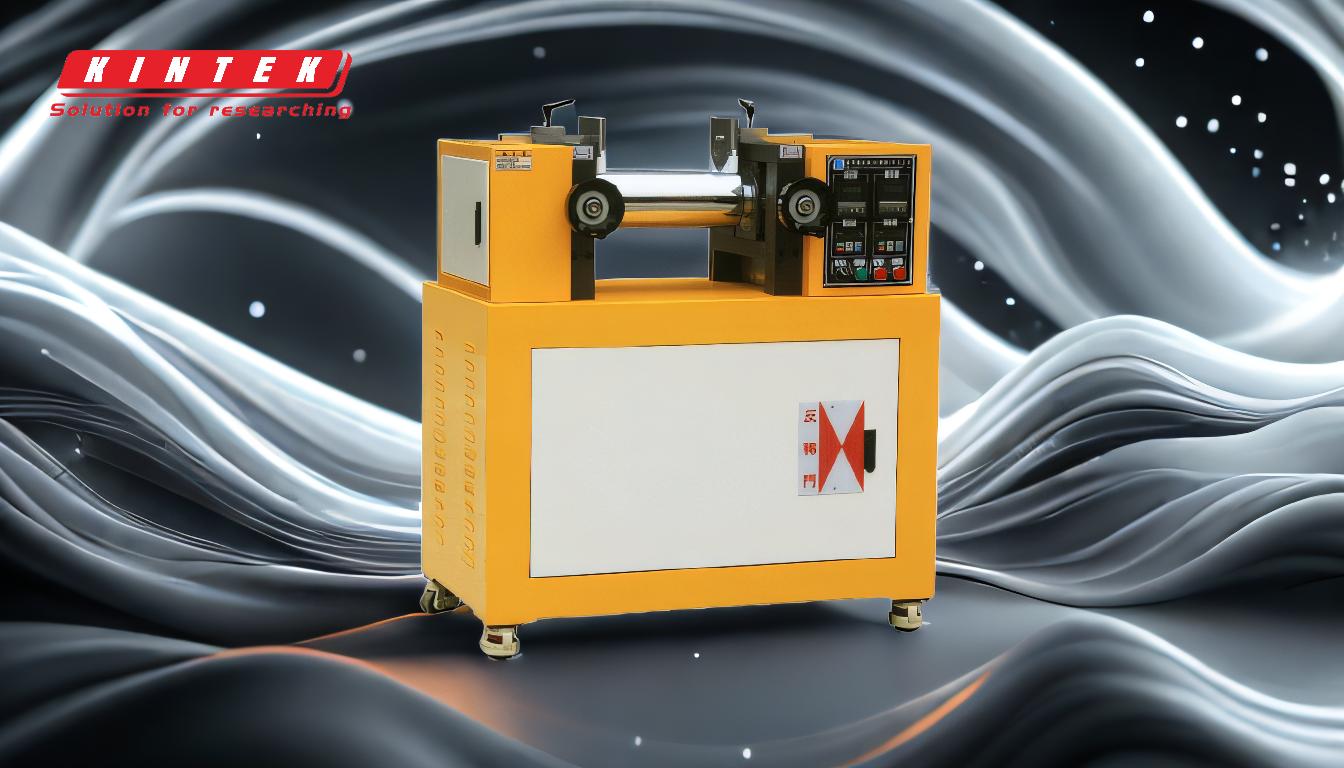
-
Basic Structure and Operation:
- A two-high roll mill consists of two horizontal rollers placed one above the other.
- The rollers rotate in opposite directions at the same or different speeds, depending on the application.
- The front roller is often adjustable, allowing the operator to control the gap between the rollers, while the rear roller is typically fixed.
- Materials such as rubber, plastics, or pigments are fed into the gap between the rollers, where they are subjected to shearing forces and heat, resulting in mixing or processing.
-
Key Components:
- Rollers: Made of corrosion-resistant steel, the rollers are designed to maintain uniform temperature and withstand high-temperature applications.
- Bearing and Frame: Support the rollers and ensure smooth operation.
- Driving Device: Powers the rollers and controls their rotation speed.
- Distance Adjusting Device: Allows for precise adjustment of the gap between the rollers.
- Temperature Adjusting Device: Regulates the temperature of the rollers to ensure consistent results.
- Emergency Braking Device: Ensures safety by stopping the machine in case of an emergency.
-
Functionality and Applications:
- Mixing and Compounding: The primary function of a two-roll mill is to mix rubber, plastics, or polymers with additives, pigments, or other materials.
- Shearing Forces: The difference in rotational speed between the two rollers creates friction and shearing forces, which are crucial for effective mixing.
- Heat Generation: The rollers generate heat, which helps in the mastication and processing of materials.
- Applications: Used in material development, quality control, pigment evaluation, polymer testing, and educational purposes.
-
Advantages:
- Consistency: The uniform temperature and precise control of roller speed and gap ensure reproducible results.
- Durability: The use of corrosion-resistant steel makes the rollers durable and suitable for high-temperature applications.
- Versatility: Suitable for a wide range of materials, including rubber, plastics, and pigments.
-
Industrial and Laboratory Use:
- In industrial settings, two-roll mills are used for large-scale mixing and compounding of materials.
- In laboratories, they are used for small-scale testing, material development, and quality control.
-
Safety and Maintenance:
- The inclusion of an emergency braking device enhances safety during operation.
- Regular maintenance of components like bearings, lubrication systems, and temperature control devices is essential for optimal performance.
By understanding these key points, a purchaser can evaluate whether a two-high roll mill meets their specific needs for material processing, mixing, or testing. The machine's versatility, durability, and precision make it a valuable tool in both industrial and laboratory settings.
Summary Table:
Feature | Description |
---|---|
Basic Structure | Two horizontal rollers rotating in opposite directions for material processing. |
Key Components | Rollers, bearing and frame, driving device, distance and temperature adjusters. |
Applications | Mixing, compounding, quality control, and material testing. |
Advantages | Consistent results, durability, and versatility for various materials. |
Industrial Use | Large-scale mixing and compounding in industries. |
Laboratory Use | Small-scale testing and material development. |
Safety Features | Emergency braking device and regular maintenance for safe operation. |
Discover how a two-high roll mill can enhance your material processing—contact us today!