An internal screw mixer is a specialized equipment designed for mixing and blending solid materials, particularly granular or powdered substances. It operates using a vertical vessel with a rotating screw mechanism that facilitates material circulation and elevation. This action ensures thorough intermixing of solid particles and applies shear forces to those in direct contact with the screw, enhancing the mixing efficiency. The design is particularly useful for achieving uniform consistency in materials, making it a valuable tool in industries like food processing, pharmaceuticals, and chemical manufacturing.
Key Points Explained:
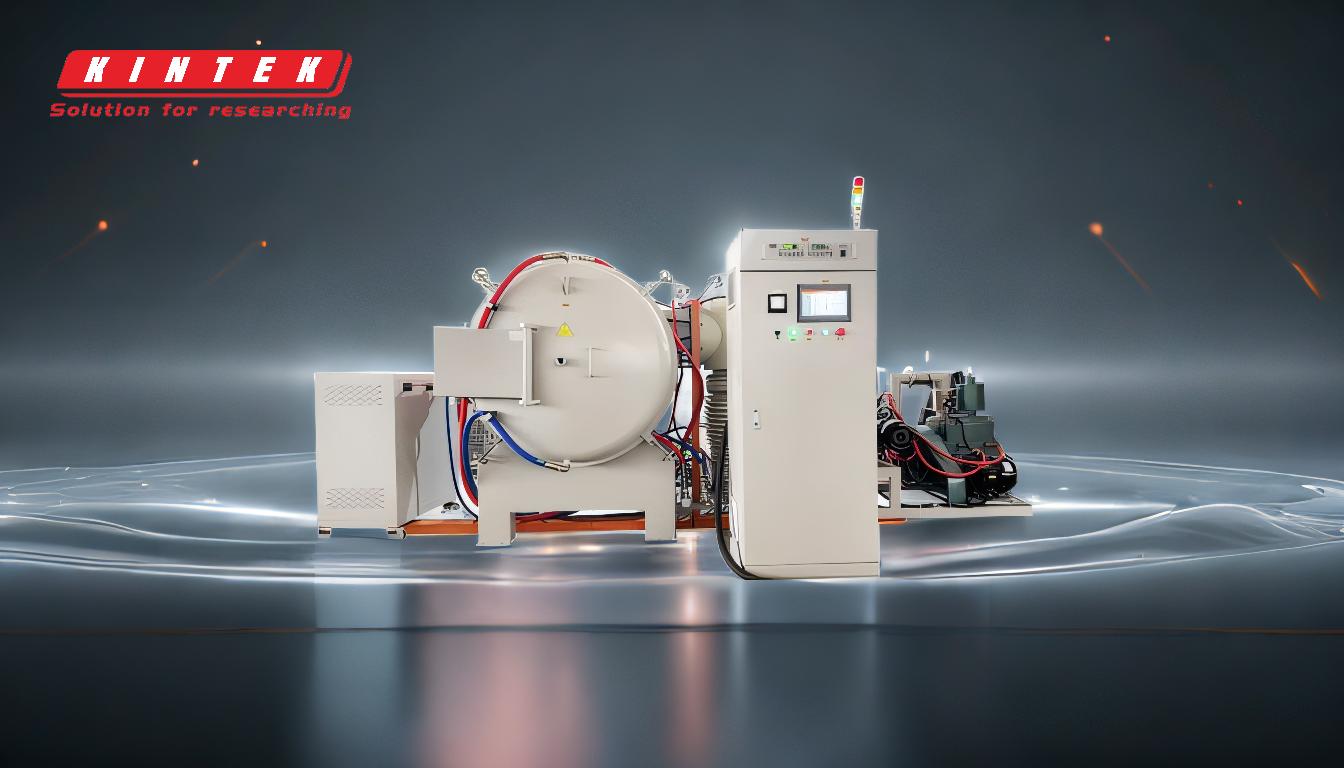
-
Design and Structure:
- The internal screw mixer is a vertical vessel equipped with a rotating screw.
- The screw's primary function is to move materials upward and circulate them within the vessel.
-
Material Circulation:
- The screw's rotation ensures that materials are continuously lifted and redistributed.
- This circulation promotes even mixing by preventing material stagnation and ensuring all particles are exposed to the mixing action.
-
Elevation of Material:
- As the screw rotates, it elevates materials from the bottom to the top of the vessel.
- This vertical movement helps in achieving a homogeneous mixture by redistributing particles throughout the vessel.
-
Intermixing of Solid Grains:
- The continuous movement and redistribution of materials lead to the intermixing of solid grains.
- This ensures that different particles are evenly distributed, resulting in a uniform blend.
-
Shear Action:
- The screw applies shear forces to materials in direct contact with it.
- This shear action is crucial for breaking down agglomerates and ensuring finer mixing, especially in cohesive or sticky materials.
-
Applications:
- Internal screw mixers are widely used in industries requiring precise and uniform mixing, such as food processing, pharmaceuticals, and chemical manufacturing.
- They are particularly effective for handling granular or powdered materials that need consistent blending.
-
Advantages:
- The design ensures efficient mixing with minimal energy consumption.
- The vertical configuration saves space compared to horizontal mixers.
- The shear action enhances the quality of the final product by ensuring a more uniform mixture.
By understanding these key points, an equipment or consumable purchaser can make an informed decision about the suitability of an internal screw mixer for their specific needs, ensuring optimal performance and product quality.
Summary Table:
Feature | Description |
---|---|
Design | Vertical vessel with a rotating screw for material circulation and elevation. |
Material Circulation | Continuous lifting and redistribution of materials for even mixing. |
Shear Action | Breaks down agglomerates, ensuring finer mixing of cohesive or sticky materials. |
Applications | Food processing, pharmaceuticals, and chemical manufacturing. |
Advantages | Efficient mixing, space-saving design, and enhanced product uniformity. |
Optimize your material blending process with an internal screw mixer—contact us today to learn more! For more information on related equipment, check out our laboratory vortex mixer and glass reactor vessel.