Ceramic fiber modules are pre-fabricated insulation units made from high-quality ceramic fiber blankets. These modules are designed for quick and efficient installation in high-temperature industrial furnaces and kilns. They are constructed by folding or stitching ceramic fiber blankets into specific shapes and sizes, often reinforced with anchors or other accessories to ensure stability and durability. The primary purpose of ceramic fiber modules is to provide superior thermal insulation, reduce heat loss, and improve energy efficiency in industrial heating applications. Their modular design simplifies installation, making them a popular choice for lining furnaces, boilers, and other high-temperature equipment.
Key Points Explained:
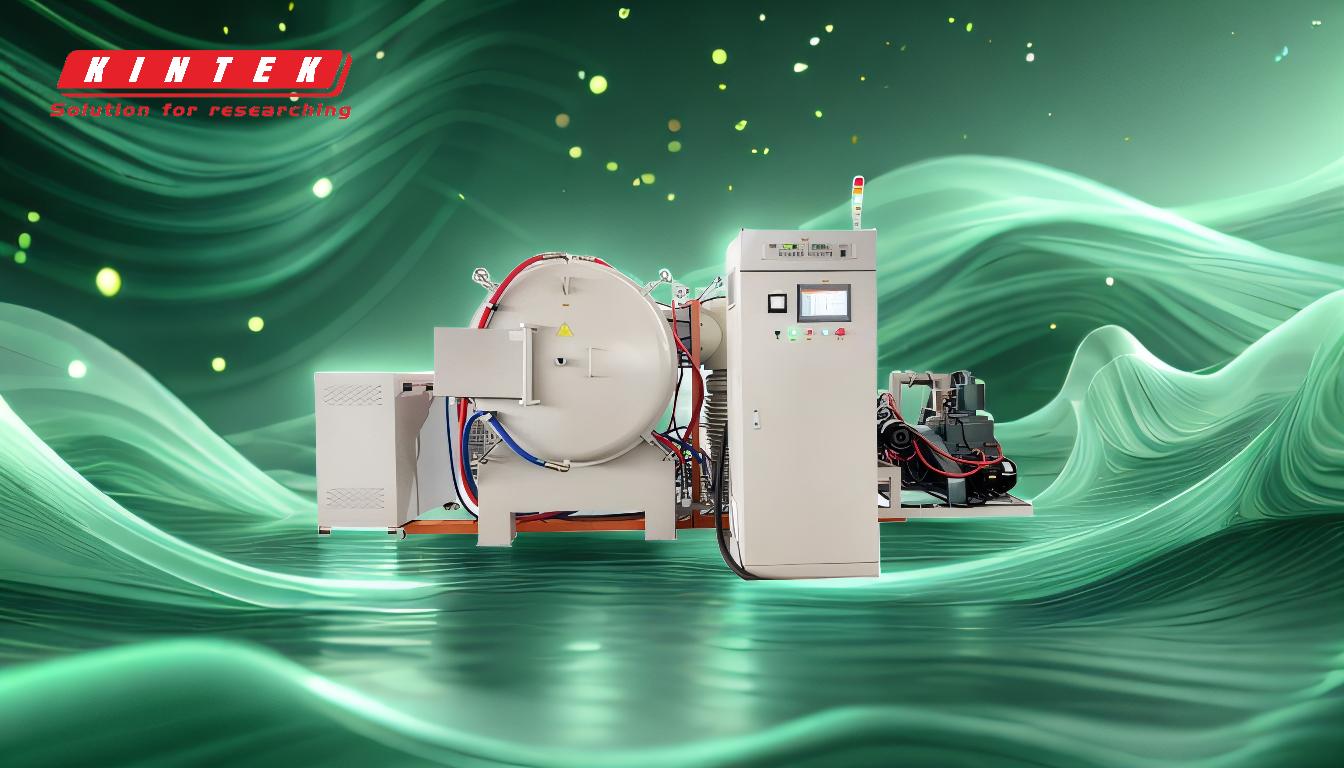
-
Composition of Ceramic Fiber Modules:
- Ceramic fiber modules are made from high-quality ceramic fiber blankets, which are lightweight, flexible, and resistant to high temperatures.
- The blankets are either folded or stitched to form the module's structure, ensuring uniformity and consistency in insulation performance.
-
Design and Construction:
- The modules are edge-staked or folded to create a compact and durable structure.
- Anchors and other accessories are integrated into the modules to facilitate secure installation and long-term stability in high-temperature environments.
-
Installation Advantages:
- The modular design allows for quick and efficient installation, reducing downtime during furnace relining or maintenance.
- The pre-fabricated nature of the modules ensures consistent insulation performance and eliminates the need for on-site cutting or shaping.
-
Applications:
- Ceramic fiber modules are widely used in industrial furnaces, kilns, boilers, and other high-temperature equipment.
- They are suitable for applications requiring thermal insulation, heat conservation, and energy efficiency.
-
Benefits:
- Superior thermal insulation properties, reducing heat loss and improving energy efficiency.
- Lightweight and flexible, reducing the structural load on furnaces and equipment.
- Resistant to thermal shock and chemical corrosion, ensuring long-term durability in harsh environments.
-
Customization:
- Ceramic fiber modules can be customized in terms of size, shape, and density to meet specific application requirements.
- Various anchor types and installation accessories are available to suit different furnace designs and operating conditions.
By combining these features, ceramic fiber modules offer a reliable and efficient solution for high-temperature insulation needs in industrial settings. Their ease of installation, durability, and performance make them a preferred choice for many industries.
Summary Table:
Feature | Description |
---|---|
Composition | Made from high-quality ceramic fiber blankets, lightweight and heat-resistant. |
Design | Folded or stitched for durability, reinforced with anchors for stability. |
Installation | Modular design for quick, efficient installation with minimal downtime. |
Applications | Used in furnaces, kilns, boilers, and other high-temperature equipment. |
Benefits | Superior insulation, lightweight, resistant to thermal shock and corrosion. |
Customization | Available in various sizes, shapes, and densities to meet specific needs. |
Upgrade your industrial furnace insulation with ceramic fiber modules—contact us today for a customized solution!