Molds in metal casting are essential tools used to shape molten metal into desired forms. They act as cavities that receive liquid metal, which then cools and solidifies into the shape of the mold. Molds can range from simple designs, like those used for ingots, to highly complex shapes based on intricate patterns. The process involves creating a mold cavity that matches the final product's geometry, ensuring precision and repeatability in manufacturing. Molds are critical in industries requiring metal components, as they determine the final product's shape, surface finish, and dimensional accuracy.
Key Points Explained:
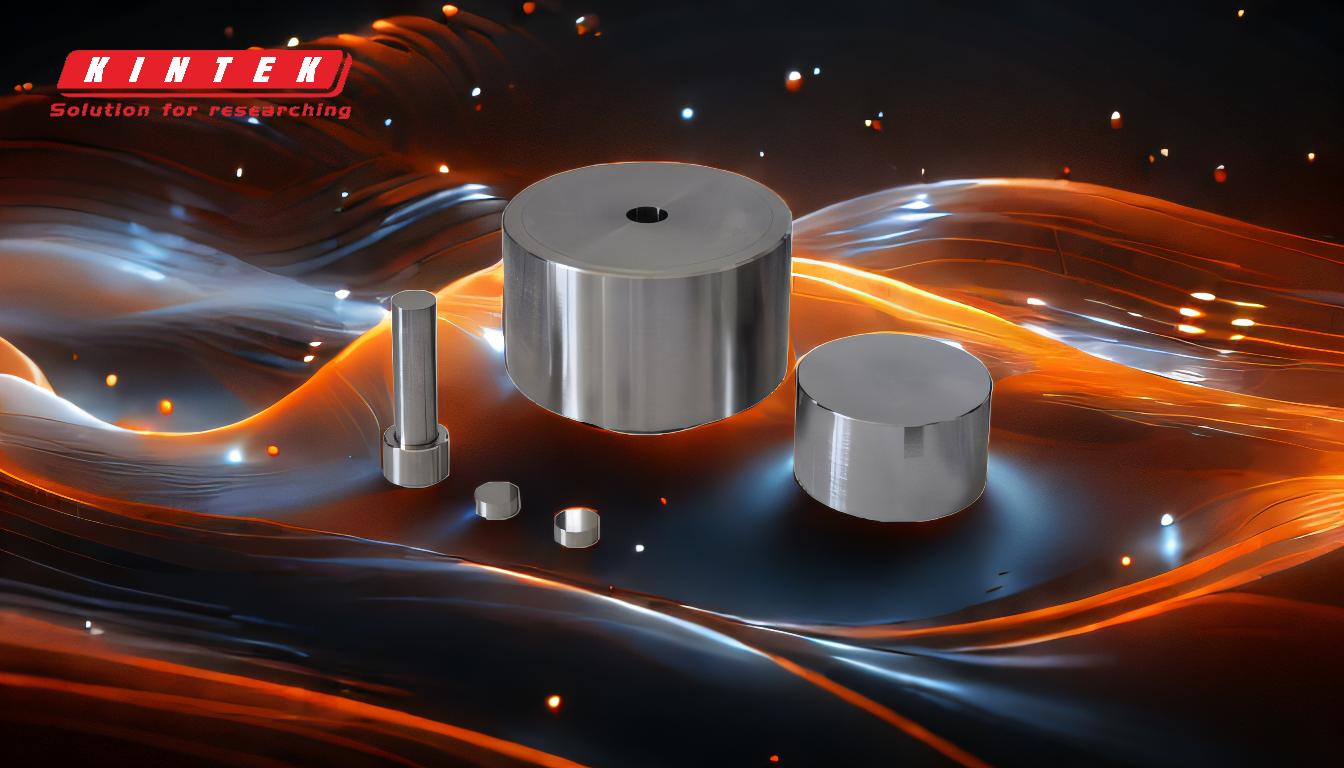
-
Definition of a Mold in Metal Casting
- A mold is a cavity designed to receive molten metal and shape it into a specific form as it cools and solidifies.
- It serves as a negative of the final product, ensuring the metal takes on the desired geometry.
-
Types of Molds
- Simple Molds: These are basic designs, such as those used for creating ingots. They resemble loaf pans, where molten metal is poured and left to cool.
- Complex Molds: These are used for intricate shapes and are often based on patterns. They require precise engineering to replicate detailed features of the final product.
-
Role of Patterns in Mold Creation
- Patterns are replicas of the final product, used to create the mold cavity.
- They determine the mold's internal shape and are critical for achieving accurate and consistent casting results.
-
Functionality of Molds
- Molds ensure the molten metal fills the cavity completely, capturing all details of the pattern.
- They provide structural support during cooling, preventing deformities or defects in the final product.
-
Applications of Molds in Metal Casting
- Molds are used across industries to produce metal components, from automotive parts to aerospace components.
- They enable mass production of identical parts with high precision and repeatability.
-
Importance of Mold Design
- Proper mold design ensures dimensional accuracy, surface finish, and structural integrity of the cast metal.
- It minimizes defects such as shrinkage, porosity, or incomplete filling of the mold cavity.
-
Materials Used for Molds
- Molds can be made from various materials, including sand, ceramic, metal, or graphite, depending on the casting process and metal type.
- The choice of material affects the mold's durability, heat resistance, and ability to produce fine details.
-
Challenges in Mold Making
- Creating molds for complex shapes requires advanced techniques and precision engineering.
- Ensuring proper venting and gating systems to allow molten metal to flow smoothly and avoid trapped air is critical.
By understanding the role and design of molds in metal casting, manufacturers can optimize the casting process to produce high-quality metal components efficiently.
Summary Table:
Aspect | Details |
---|---|
Definition | Cavity designed to shape molten metal into specific forms as it solidifies. |
Types | Simple (e.g., ingots) and complex (intricate shapes based on patterns). |
Role of Patterns | Replicas of final products used to create mold cavities. |
Functionality | Ensures complete filling and structural support during cooling. |
Applications | Automotive, aerospace, and other industries requiring metal components. |
Importance of Design | Ensures accuracy, surface finish, and minimizes defects. |
Materials | Sand, ceramic, metal, or graphite, depending on the process. |
Challenges | Requires precision engineering and proper venting/gating systems. |
Optimize your metal casting process with expertly designed molds—contact us today!