Mold release spray is a specialized product designed to prevent materials from sticking to molds during manufacturing processes. It typically consists of a combination of aerosols and wax, where the aerosol acts as a carrier to evenly distribute the wax onto the mold surface. Once sprayed, the aerosol evaporates, leaving behind a thin, protective wax coating that ensures easy release of the molded product. This composition makes it highly effective for applications in industries like plastics, composites, and rubber manufacturing.
Key Points Explained:
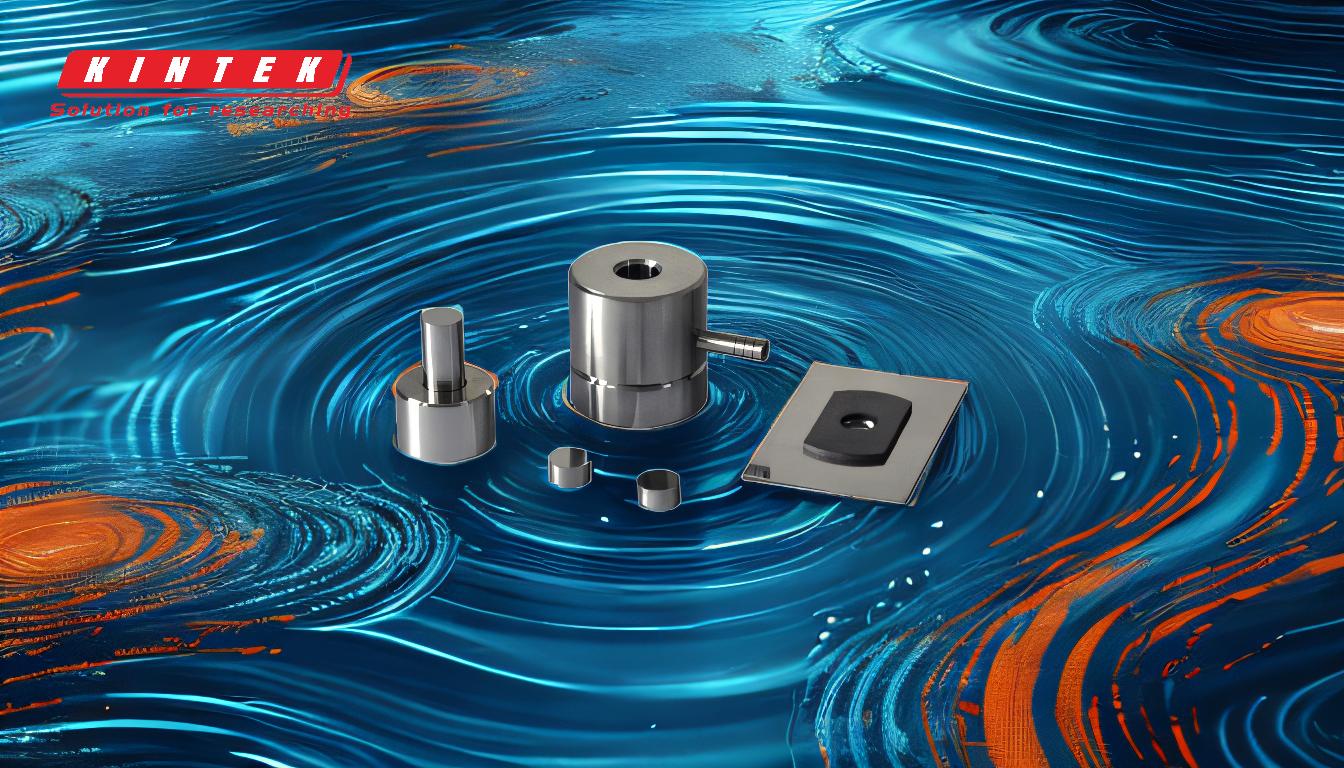
-
Primary Components of Mold Release Spray:
- Aerosols: These act as the carrier material in the spray. They help evenly distribute the wax over the mold surface. Aerosols are typically volatile compounds that evaporate quickly after application.
- Wax: The wax is the active ingredient that forms a protective layer on the mold. It prevents the molded material from adhering to the mold, ensuring a smooth release.
-
How It Works:
- When the spray is applied, the aerosol carries the wax particles and disperses them uniformly over the mold surface.
- The aerosol quickly evaporates, leaving behind a thin, even layer of wax.
- This wax layer reduces friction and adhesion, allowing the molded product to be easily removed without damage.
-
Applications of Mold Release Spray:
- Plastics Manufacturing: Used to release plastic parts from molds without leaving residue.
- Composite Materials: Helps in the production of fiberglass, carbon fiber, and other composite parts.
- Rubber Molding: Ensures easy removal of rubber products from molds.
- Other Industries: Also used in concrete casting, food processing (for non-stick applications), and more.
-
Benefits of Using Mold Release Spray:
- Ease of Use: The spray application ensures even coverage and reduces manual effort.
- Non-Stick Properties: The wax layer prevents sticking, reducing the risk of damaged molds or products.
- Versatility: Suitable for a wide range of materials and industries.
- Efficiency: Speeds up production by minimizing downtime caused by stuck parts.
-
Considerations for Equipment and Consumable Purchasers:
- Compatibility: Ensure the spray is compatible with the materials being molded (e.g., plastics, rubber, composites).
- Environmental Impact: Look for eco-friendly options with low volatile organic compound (VOC) emissions.
- Performance: Evaluate the spray's effectiveness in terms of release quality and residue left behind.
- Cost-Effectiveness: Balance the price with the performance and longevity of the product.
- Safety: Choose sprays that are non-toxic and safe for use in your specific environment.
By understanding the composition and functionality of mold release spray, purchasers can make informed decisions that enhance production efficiency and product quality.
Summary Table:
Aspect | Details |
---|---|
Primary Components | Aerosols (carrier) and wax (protective layer) |
How It Works | Aerosol evaporates, leaving a wax layer for easy mold release |
Applications | Plastics, composites, rubber, concrete casting, food processing |
Benefits | Ease of use, non-stick properties, versatility, efficiency |
Purchasing Tips | Compatibility, eco-friendliness, performance, cost-effectiveness, safety |
Enhance your manufacturing process with mold release spray—contact us today to learn more!