Glass coating materials are diverse and tailored to specific applications, leveraging the unique properties of metals, ceramics, and polymers. These materials are chosen based on factors such as melting points, mechanical behavior, and chemical resistance. Metals like aluminum (Al), titanium (Ti), and platinum (Pt) are commonly used for their durability and reflective properties. Ceramics such as magnesium oxide (MgO) and zirconium dioxide (ZrO2) offer high thermal stability and wear resistance. Polymers like PEEK and PTFE are valued for their chemical resistance and flexibility. Understanding the properties and applications of these materials is crucial for selecting the right coating for glass in various industries.
Key Points Explained:
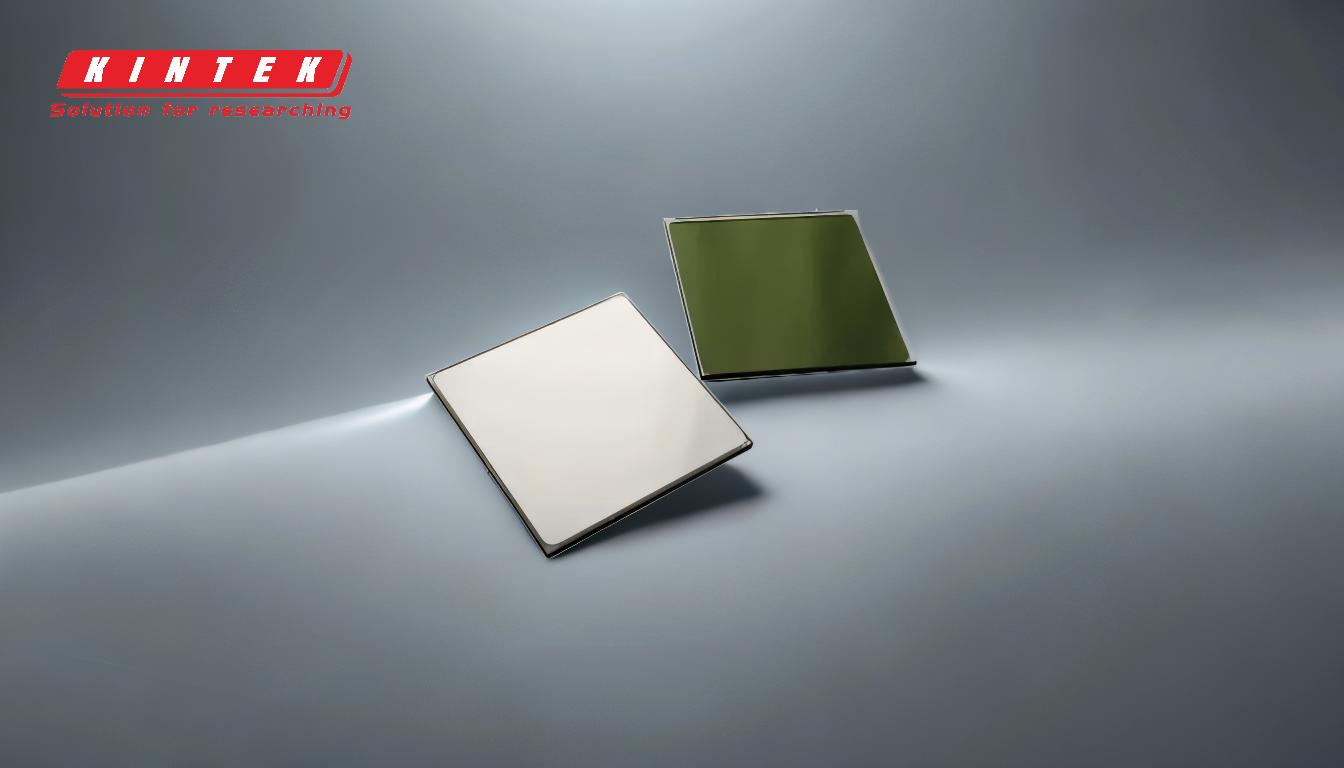
-
Metals as Coating Materials:
- Aluminum (Al): Lightweight, reflective, and corrosion-resistant, aluminum is often used in optical applications and as a protective layer.
- Titanium (Ti): Known for its strength and biocompatibility, titanium coatings are used in medical devices and aerospace applications.
- Platinum (Pt): Highly resistant to oxidation and corrosion, platinum coatings are used in high-temperature and chemically aggressive environments.
-
Ceramics as Coating Materials:
- Magnesium Oxide (MgO): Offers excellent thermal stability and is used in high-temperature applications.
- Zirconium Dioxide (ZrO2): Known for its high strength and wear resistance, ZrO2 is used in protective coatings and as a thermal barrier.
- Aluminum Oxide (Al2O3): Provides high hardness and chemical resistance, making it suitable for abrasive environments.
-
Polymers as Coating Materials:
- PEEK (Polyether Ether Ketone): A high-performance polymer with excellent chemical resistance and mechanical properties, used in demanding applications.
- PTFE (Polytetrafluoroethylene): Known for its non-stick properties and chemical inertness, PTFE is used in coatings for cookware and industrial applications.
-
Selection Criteria for Coating Materials:
- Melting Points: High melting points are crucial for coatings exposed to high temperatures.
- Mechanical Behavior: Strength, flexibility, and wear resistance are key factors in material selection.
- Chemical Resistance: Resistance to corrosion and chemical attack is essential for coatings in harsh environments.
-
Applications of Glass Coatings:
- Optical Coatings: Metals like aluminum are used to create reflective surfaces in mirrors and lenses.
- Protective Coatings: Ceramics and polymers are used to protect glass from scratches, chemical damage, and thermal stress.
- Functional Coatings: Coatings can also provide additional functionalities such as anti-fogging, anti-reflective, or conductive properties.
By understanding the properties and applications of these materials, one can make informed decisions when selecting the appropriate coating for glass in various contexts.
Summary Table:
Material Type | Examples | Key Properties | Applications |
---|---|---|---|
Metals | Aluminum (Al), Titanium (Ti), Platinum (Pt) | Durability, reflectivity, corrosion resistance | Optical coatings, medical devices, aerospace |
Ceramics | MgO, ZrO2, Al2O3 | High thermal stability, wear resistance, chemical resistance | High-temperature applications, protective coatings, thermal barriers |
Polymers | PEEK, PTFE | Chemical resistance, flexibility, non-stick properties | Industrial coatings, cookware, demanding applications |
Selection Criteria | Melting points, mechanical behavior, chemical resistance | High melting points, strength, flexibility, corrosion resistance | Suitable for harsh environments, protective and functional coatings |
Need help selecting the right glass coating material? Contact our experts today for tailored solutions!