Compressors and pumps are both mechanical devices used to move fluids, but they operate on different principles and are designed for specific applications. A pump primarily moves incompressible fluids like water or oil, while a compressor is designed to handle compressible fluids, such as gases. The key differences lie in their working mechanisms, pressure handling capabilities, and the nature of the fluids they process. Pumps generally increase the kinetic energy of the fluid to move it, whereas compressors reduce the volume of gases to increase their pressure. Understanding these distinctions is crucial for selecting the right equipment for specific industrial or commercial needs.
Key Points Explained:
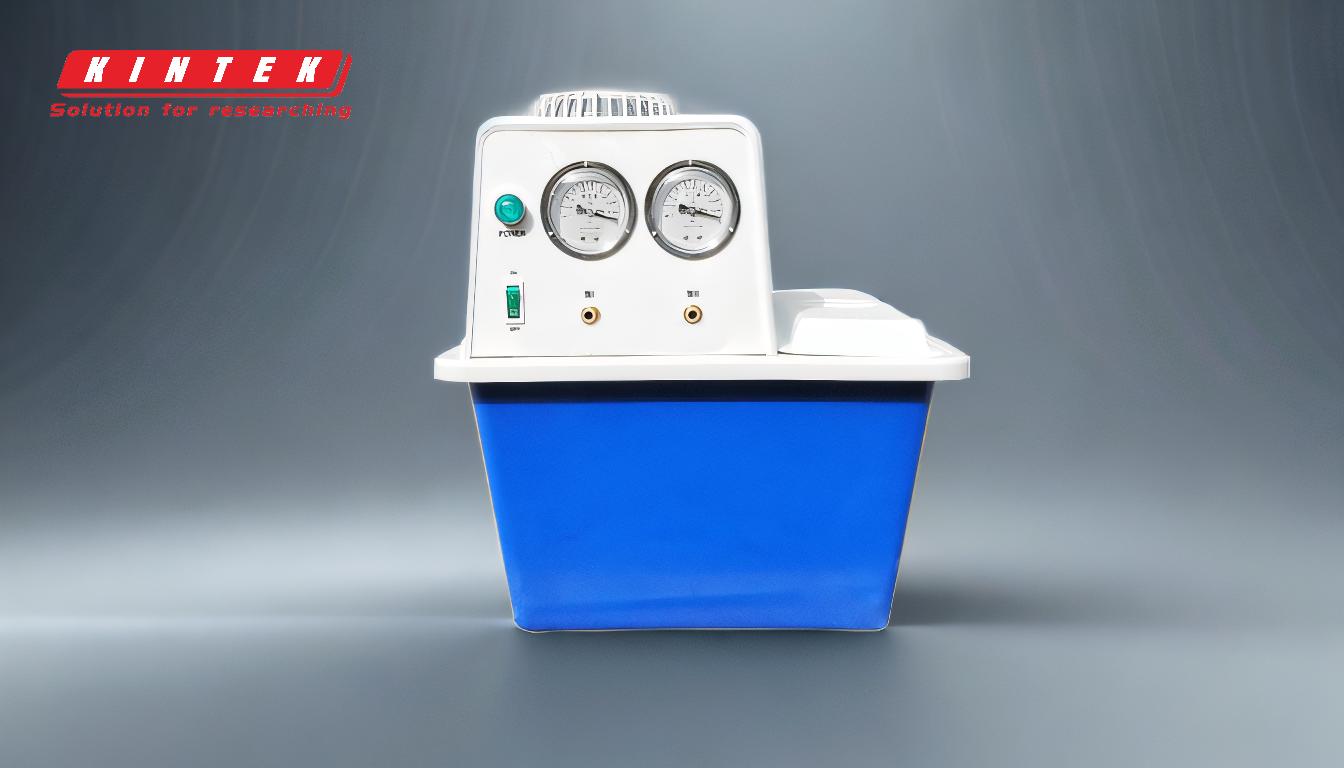
-
Nature of Fluids Processed:
- Pumps: Designed to handle incompressible fluids, such as liquids (e.g., water, oil, or chemicals). These fluids do not significantly change volume under pressure.
- Compressors: Specifically built to handle compressible fluids, such as gases (e.g., air, natural gas, or refrigerant). Gases can be compressed to reduce their volume and increase pressure.
-
Working Mechanism:
- Pumps: Operate by increasing the kinetic energy of the fluid, which is then converted into pressure energy to move the fluid through a system. Common types include centrifugal pumps and positive displacement pumps.
- Compressors: Work by reducing the volume of the gas, which increases its pressure. This is achieved through mechanisms like reciprocating pistons, rotary screws, or centrifugal force.
-
Pressure Handling:
- Pumps: Typically operate at lower pressures compared to compressors. They are designed to move fluids rather than significantly alter their pressure.
- Compressors: Capable of generating much higher pressures, as their primary function is to compress gases for storage or transport.
-
Applications:
- Pumps: Widely used in industries such as water treatment, agriculture, chemical processing, and oil refineries. They are essential for tasks like irrigation, circulation, and fluid transfer.
- Compressors: Commonly used in HVAC systems, refrigeration, natural gas processing, and industrial air systems. They are crucial for tasks like air conditioning, gas storage, and powering pneumatic tools.
-
Energy Efficiency:
- Pumps: Generally more energy-efficient when moving liquids, as they do not need to overcome the compressibility of gases.
- Compressors: Require more energy to compress gases, especially at higher pressures, due to the inherent properties of gases.
-
Design and Construction:
- Pumps: Often simpler in design, with fewer moving parts, especially in centrifugal pumps. They are built to handle the density and viscosity of liquids.
- Compressors: More complex, with components designed to handle the heat generated during gas compression. They often include cooling systems to manage the increased temperatures.
-
Maintenance and Durability:
- Pumps: Typically require less maintenance, especially when handling clean liquids. However, they can be prone to wear when handling abrasive or corrosive fluids.
- Compressors: May require more frequent maintenance due to the higher operating pressures and temperatures. Components like seals and valves are subject to more stress.
By understanding these key differences, equipment purchasers can make informed decisions based on the specific requirements of their applications, ensuring optimal performance and efficiency.
Summary Table:
Aspect | Pumps | Compressors |
---|---|---|
Nature of Fluids | Handle incompressible fluids (e.g., water, oil) | Handle compressible fluids (e.g., air, natural gas) |
Working Mechanism | Increase kinetic energy to move fluids | Reduce gas volume to increase pressure |
Pressure Handling | Operate at lower pressures | Generate higher pressures |
Applications | Water treatment, agriculture, chemical processing | HVAC, refrigeration, natural gas processing |
Energy Efficiency | More efficient for liquids | Require more energy for gas compression |
Design Complexity | Simpler design, fewer moving parts | More complex, with cooling systems |
Maintenance | Less maintenance, prone to wear with abrasive fluids | More frequent maintenance due to high pressures and temperatures |
Need help selecting the right equipment for your needs? Contact our experts today for tailored advice!