Fiber kilns and brick kilns differ primarily in their construction materials, which lead to significant differences in heating and cooling rates, efficiency, and suitability for specific applications. Fiber kilns, made of rigidized fiber, heat up and cool down much faster than brick kilns. This makes fiber kilns ideal for rapid production cycles, such as fusing glass or ceramics, where quick turnaround times are essential. Brick kilns, on the other hand, are slower to heat and cool due to their dense, insulating properties, making them better suited for processes that require sustained, even heat over longer periods, such as traditional pottery firing. The choice between the two depends on the user's specific needs, including the type of work being produced and the desired production speed.
Key Points Explained:
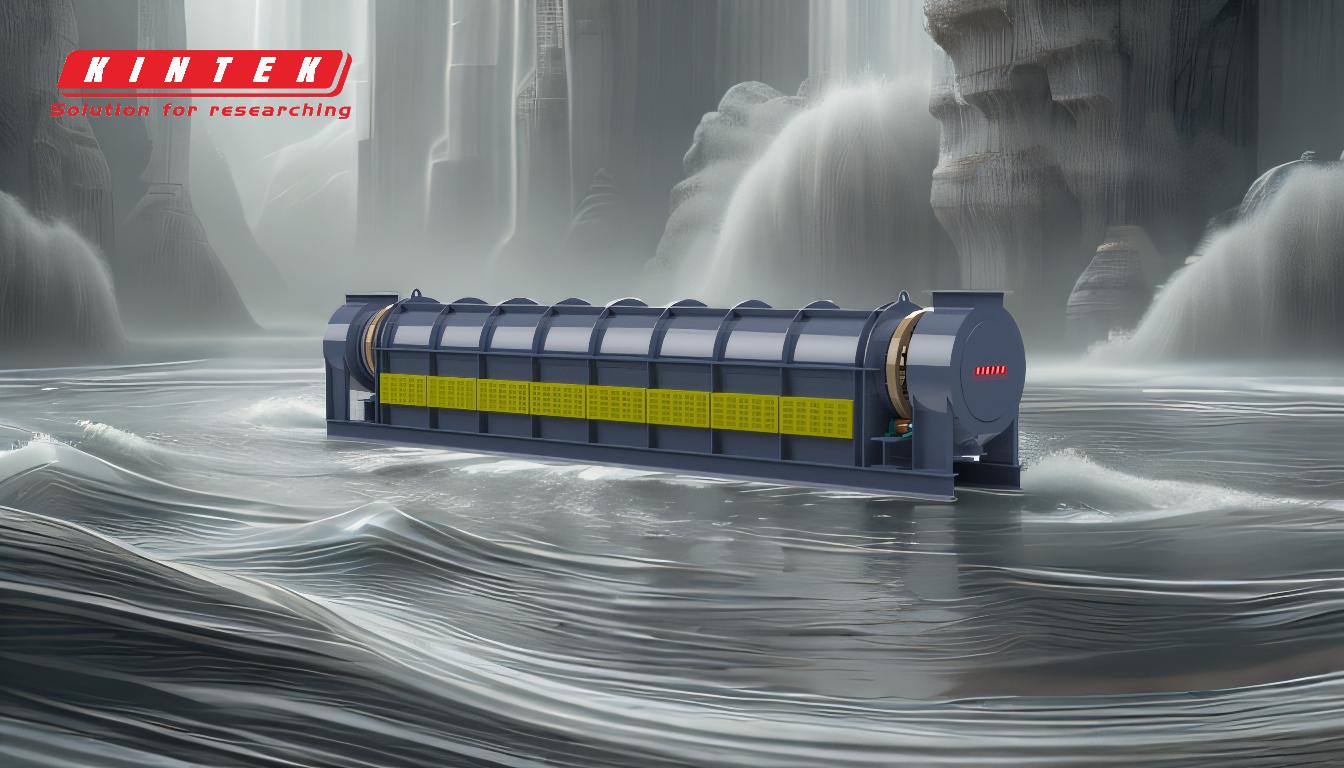
-
Construction Materials:
- Fiber Kilns: Made from rigidized fiber, a lightweight and highly insulating material. This material allows for rapid heat transfer, making fiber kilns efficient for quick heating and cooling cycles.
- Brick Kilns: Constructed from dense, refractory bricks that provide excellent thermal insulation. These bricks retain heat for longer periods, making them ideal for processes requiring consistent, prolonged heat.
-
Heating and Cooling Rates:
- Fiber Kilns: Heat up and cool down much faster due to the lightweight nature of the fiber material. This rapid thermal response is advantageous for applications like glass fusing, where quick turnaround times are critical.
- Brick Kilns: Slower to heat and cool because of the dense brick construction. This slower thermal response is beneficial for processes like pottery firing, where even, sustained heat is necessary to ensure proper curing and hardening of materials.
-
Efficiency and Energy Use:
- Fiber Kilns: More energy-efficient for rapid cycling due to their ability to quickly reach and lose heat. This efficiency can lead to lower energy costs over time, especially in high-production environments.
- Brick Kilns: While they may use more energy to reach and maintain high temperatures, their ability to retain heat can be more efficient for long-duration firings, reducing the need for constant energy input.
-
Suitability for Specific Applications:
- Fiber Kilns: Ideal for applications requiring quick production cycles, such as glass fusing, small-scale ceramics, or any process where rapid heating and cooling are beneficial. They are also suitable for artists or small studios with limited space, as they are generally more compact.
- Brick Kilns: Better suited for traditional pottery, large-scale ceramics, or any process that benefits from prolonged, even heat. They are often used in industrial settings or by artists who require the consistent, high temperatures that brick kilns can provide.
-
Durability and Maintenance:
- Fiber Kilns: Generally require less maintenance due to their lightweight and durable construction. However, the fiber material may degrade over time with frequent high-temperature use, requiring periodic replacement.
- Brick Kilns: Known for their durability and longevity, especially in high-temperature environments. However, they may require more maintenance, such as replacing worn bricks or repairing cracks, to ensure consistent performance.
-
Cost Considerations:
- Fiber Kilns: Often more affordable initially due to their simpler construction and lighter materials. However, the potential need for more frequent replacement of fiber components could increase long-term costs.
- Brick Kilns: Typically have a higher upfront cost due to the materials and construction required. However, their durability and longevity can make them a more cost-effective option over time, especially for users who require consistent, high-temperature firings.
In summary, the choice between a fiber kiln and a brick kiln depends on the specific needs of the user, including the type of work being produced, desired production speed, and long-term cost considerations. Fiber kilns offer rapid heating and cooling, making them ideal for quick-turnaround projects, while brick kilns provide sustained, even heat, making them better suited for traditional, long-duration firings.
Summary Table:
Feature | Fiber Kiln | Brick Kiln |
---|---|---|
Material | Rigidized fiber (lightweight, insulating) | Dense refractory bricks (excellent insulation) |
Heating/Cooling | Rapid heating and cooling | Slower heating and cooling |
Efficiency | Energy-efficient for rapid cycles | Efficient for long-duration firings |
Applications | Glass fusing, small-scale ceramics | Traditional pottery, large-scale ceramics |
Durability | Less maintenance, but fiber may degrade | Highly durable, requires more maintenance |
Cost | Lower upfront cost, higher long-term | Higher upfront cost, cost-effective long-term |
Still unsure which kiln is right for you? Contact our experts today for personalized advice!