A vacuum pump and a regular pump differ primarily in their purpose, operating principles, and design. A vacuum pump is specifically designed to remove gas molecules from a sealed volume to create a partial or full vacuum, altering pressure states to achieve this. It operates with high pressure ratios and can be mechanical or chemical in nature. Regular pumps, on the other hand, are used to move fluids (liquids or gases) from one place to another, often to increase pressure or flow rate. Vacuum pumps are categorized into wet and dry types, with wet pumps using oil or water for lubrication and sealing, while dry pumps rely on tight tolerances and operate without lubrication. Regular pumps, such as centrifugal or positive displacement pumps, are designed for fluid transfer and do not focus on creating a vacuum.
Key Points Explained:
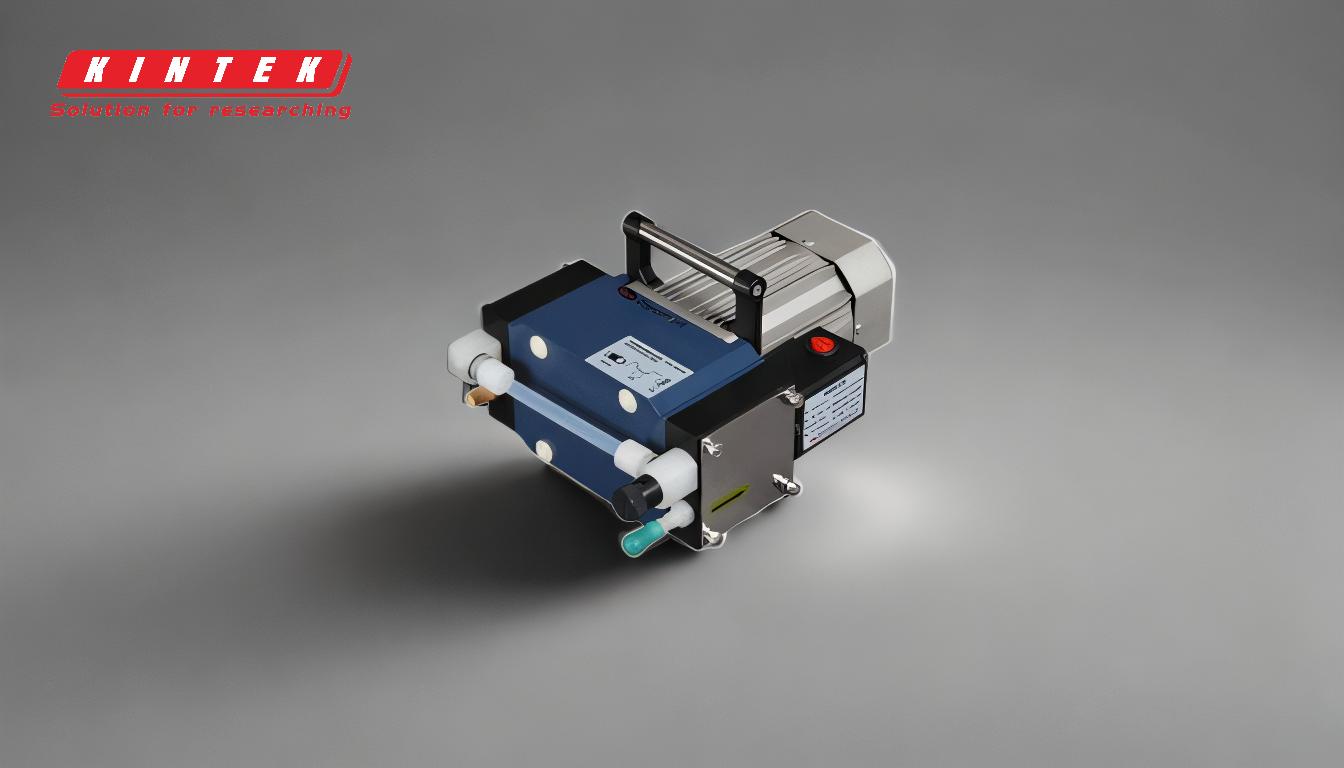
-
Purpose and Functionality:
- Vacuum Pump: Designed to remove gas molecules from a sealed volume, creating a partial or full vacuum. It operates by altering pressure states, moving gas molecules from high-pressure to low-pressure areas. This is essential in applications requiring controlled environments, such as laboratories, manufacturing, or HVAC systems.
- Regular Pump: Focuses on moving fluids (liquids or gases) from one location to another. Its primary function is to increase pressure or flow rate, making it suitable for applications like water supply, irrigation, or industrial fluid transfer.
-
Operating Principles:
- Vacuum Pump: Works with a high pressure ratio, often requiring multistage designs to achieve the necessary vacuum levels. It can operate mechanically (e.g., rotary vane pumps) or chemically (e.g., diffusion pumps). The process involves compressing a vacuum to higher pressures, typically up to atmospheric pressure.
- Regular Pump: Operates by increasing the kinetic energy of the fluid, often through mechanisms like impellers (centrifugal pumps) or pistons (positive displacement pumps). Its goal is to maintain or increase fluid pressure for transportation or processing.
-
Design and Lubrication:
- Vacuum Pump: Can be categorized into wet and dry types. Wet vacuum pumps use oil or water for lubrication and sealing, which helps maintain efficiency and reduce wear. Dry vacuum pumps, on the other hand, operate without lubrication, relying on precise tolerances to function effectively.
- Regular Pump: Typically uses lubrication to reduce friction and wear, especially in rotating or moving parts. The design focuses on durability and efficiency for continuous fluid transfer, often incorporating seals and bearings to prevent leaks and maintain performance.
-
Pressure Handling:
- Vacuum Pump: Designed to handle very low pressures, often below atmospheric pressure, and can achieve near-vacuum conditions. It operates within specific pressure ranges, such as 1 bar(a) to 0.1 bar(a), depending on the application.
- Regular Pump: Operates at or above atmospheric pressure, focusing on maintaining or increasing fluid pressure for transportation or processing. It is not designed to create or handle vacuum conditions.
-
Applications:
- Vacuum Pump: Used in applications requiring controlled environments, such as vacuum packaging, semiconductor manufacturing, and scientific research. It is essential in processes where gas removal or pressure reduction is critical.
- Regular Pump: Applied in everyday scenarios like water supply, HVAC systems, and industrial processes. It is versatile and widely used for fluid transfer and pressure maintenance.
By understanding these key differences, equipment and consumable purchasers can make informed decisions based on the specific requirements of their applications, ensuring optimal performance and efficiency.
Summary Table:
Aspect | Vacuum Pump | Regular Pump |
---|---|---|
Purpose | Removes gas molecules to create a vacuum. | Moves fluids (liquids/gases) to increase pressure or flow rate. |
Operating Principle | High pressure ratio, multistage designs, mechanical or chemical operation. | Increases kinetic energy of fluids via impellers or pistons. |
Design | Wet (oil/water lubrication) or dry (tight tolerances, no lubrication). | Uses lubrication for durability, seals, and bearings. |
Pressure Handling | Handles very low pressures, often below atmospheric pressure. | Operates at or above atmospheric pressure. |
Applications | Vacuum packaging, semiconductor manufacturing, scientific research. | Water supply, HVAC systems, industrial fluid transfer. |
Need help choosing the right pump for your application? Contact our experts today!