A falling film evaporator and a climbing film evaporator are both types of evaporators used in industrial processes, but they differ in their design and operation. A falling film evaporator operates by allowing the process fluid to flow downward as a thin film along the walls of the tubes, where it is instantly vaporized by the hot utility. In contrast, a climbing film evaporator involves the process fluid moving upward along the tube walls, driven by the vapor generated during the heating process. The key differences lie in the direction of fluid flow, heat transfer efficiency, and suitability for different types of fluids and processes.
Key Points Explained:
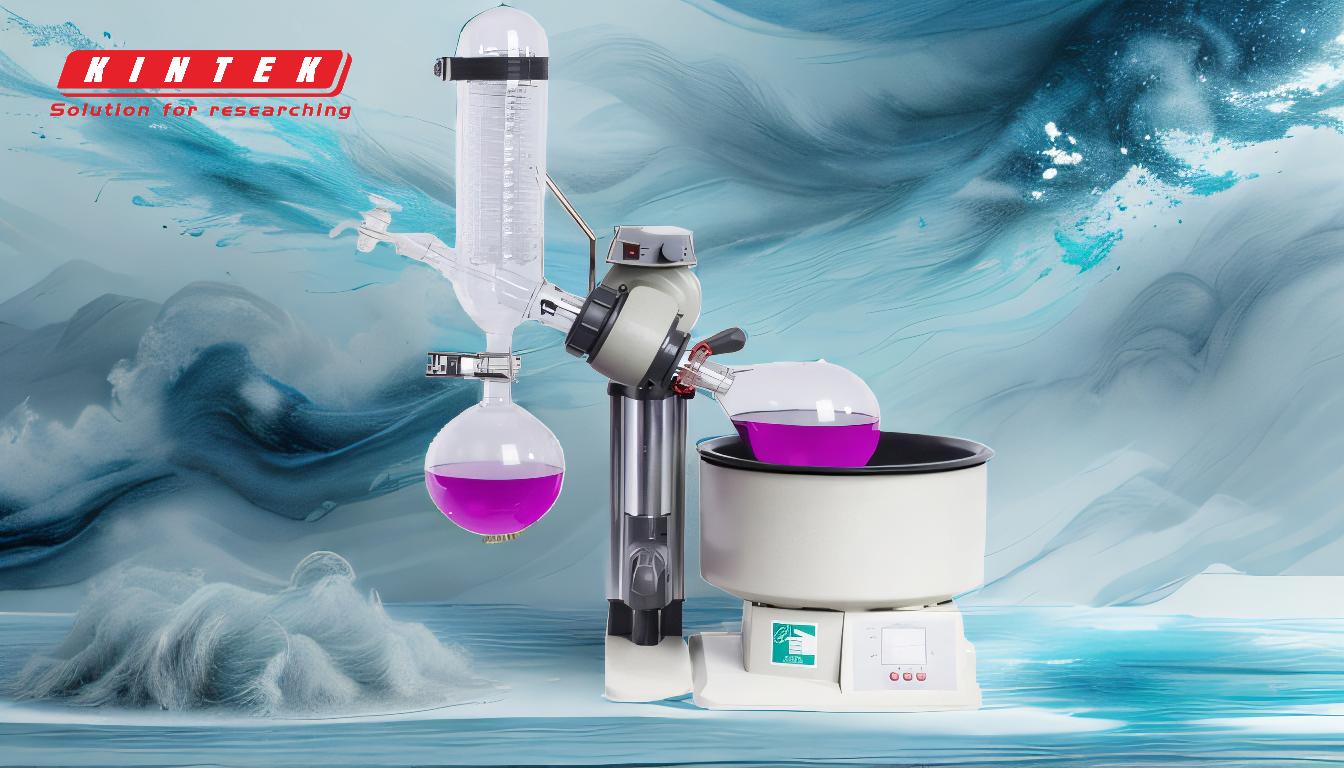
-
Direction of Fluid Flow:
- Falling Film Evaporator: The process fluid flows downward along the walls of the tubes. This design is particularly useful for heat-sensitive materials because the fluid is exposed to heat for a shorter duration.
- Climbing Film Evaporator: The process fluid moves upward along the tube walls. This upward movement is driven by the vapor generated during the heating process, which creates a lifting effect.
-
Heat Transfer Efficiency:
- Falling Film Evaporator: The thin film of liquid ensures a large surface area for heat transfer, leading to efficient evaporation. The short contact time with the heating surface minimizes the risk of thermal degradation.
- Climbing Film Evaporator: The upward movement of the fluid can lead to better mixing and more uniform heat distribution. However, the efficiency can be affected by the viscosity and boiling characteristics of the fluid.
-
Suitability for Different Fluids:
- Falling Film Evaporator: Ideal for heat-sensitive fluids and those with low viscosity. It is commonly used in the food, pharmaceutical, and chemical industries.
- Climbing Film Evaporator: More suitable for fluids that require longer contact time with the heating surface or those that benefit from the lifting action of the vapor. It is often used in applications where the fluid has a higher viscosity or where foaming is a concern.
-
Design and Construction:
- Falling Film Evaporator: Similar to a vertical shell and tube heat exchanger. The design is custom-tailored based on specific process requirements, ensuring optimal performance for the intended application.
- Climbing Film Evaporator: Also resembles a vertical shell and tube heat exchanger but is designed to facilitate the upward movement of the fluid. The design considerations include the need to manage the vapor-liquid interface effectively.
-
Operational Considerations:
- Falling Film Evaporator: Requires precise control of the liquid distribution to ensure a uniform film along the tube walls. This can be challenging but is crucial for maintaining efficiency.
- Climbing Film Evaporator: Needs careful management of the vapor flow to prevent flooding or dry-out conditions. The operational parameters must be carefully controlled to maintain the desired performance.
In summary, while both falling film and climbing film evaporators are used for similar purposes, their differences in fluid flow direction, heat transfer efficiency, and suitability for different types of fluids make them better suited for specific applications. The choice between the two depends on the specific requirements of the process, including the nature of the fluid, the desired heat transfer characteristics, and the operational constraints.
Summary Table:
Aspect | Falling Film Evaporator | Climbing Film Evaporator |
---|---|---|
Direction of Fluid Flow | Fluid flows downward along tube walls, ideal for heat-sensitive materials. | Fluid moves upward, driven by vapor, suitable for higher viscosity or foaming fluids. |
Heat Transfer Efficiency | Thin film ensures large surface area, efficient evaporation, and minimal thermal degradation. | Upward movement allows better mixing but efficiency depends on fluid viscosity. |
Suitability for Fluids | Best for heat-sensitive, low-viscosity fluids (e.g., food, pharmaceuticals, chemicals). | Suitable for fluids requiring longer contact time or benefiting from vapor lifting. |
Design and Construction | Resembles a vertical shell and tube heat exchanger, tailored for specific process needs. | Similar design but optimized for upward fluid movement and vapor-liquid interface. |
Operational Considerations | Requires precise liquid distribution for uniform film. | Needs careful vapor flow management to prevent flooding or dry-out conditions. |
Need help choosing the right evaporator for your process? Contact our experts today for tailored solutions!