Pyrolysis and catalytic cracking are both thermal decomposition processes used to break down large molecules into smaller ones, but they differ significantly in their mechanisms, conditions, and applications. Pyrolysis is a thermal process that occurs in the absence of oxygen, primarily used for biomass conversion and waste treatment. Catalytic cracking, on the other hand, is a chemical process that uses heat, pressure, and a catalyst to break down large hydrocarbon molecules, commonly used in the oil and gas industry. The key differences lie in the presence of a catalyst, the reaction environment, and the specific applications of each process.
Key Points Explained:
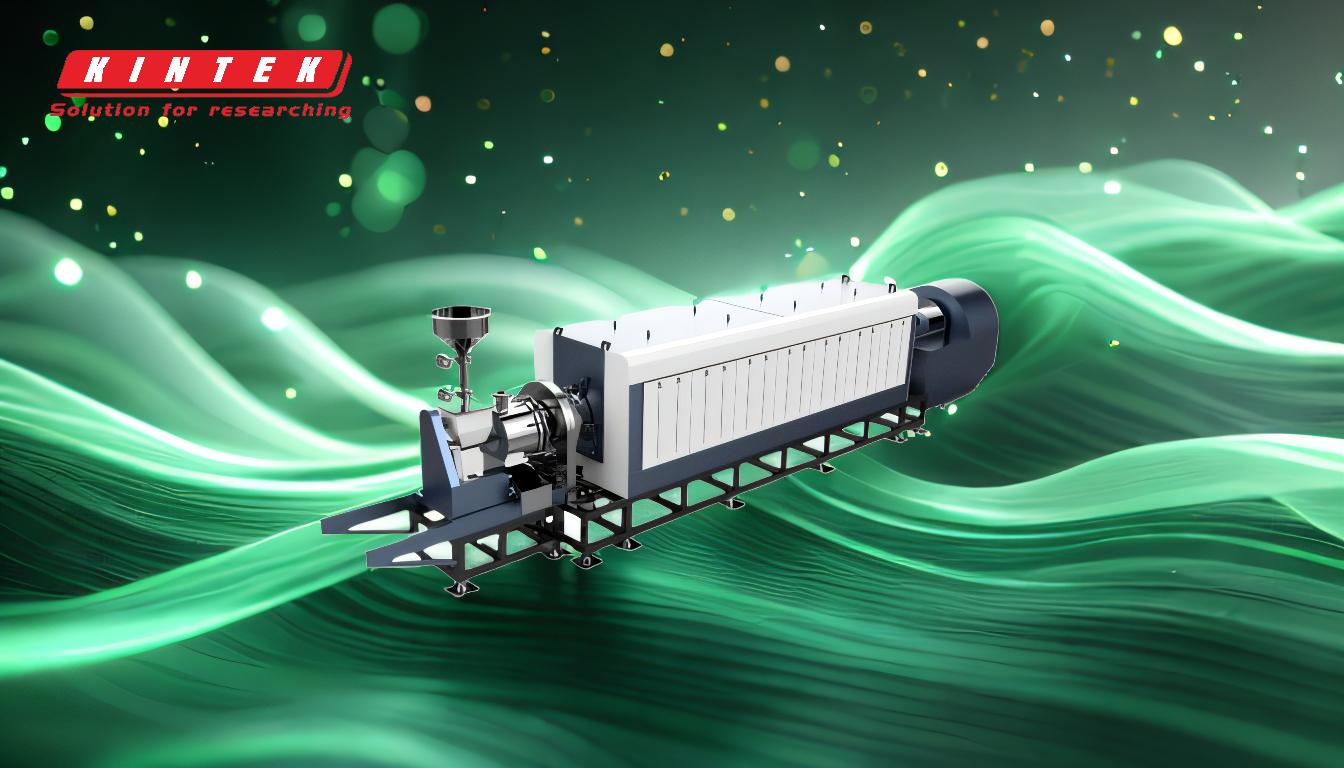
-
Definition and Mechanism:
- Pyrolysis: Pyrolysis is a thermal decomposition process that occurs in the absence of oxygen. It involves heating organic materials to high temperatures, causing them to break down into smaller molecules without combustion. This process is often used for converting biomass into bio-oil, syngas, and biochar.
- Catalytic Cracking: Catalytic cracking is a chemical process that breaks down large hydrocarbon molecules into smaller ones using heat, pressure, and a catalyst. The catalyst facilitates the cracking reactions at lower temperatures and pressures than would be required for thermal cracking alone.
-
Reaction Environment:
- Pyrolysis: Pyrolysis requires an oxygen-free environment to prevent combustion. However, achieving a completely oxygen-free environment is practically impossible, so a small amount of oxidation always occurs. The process typically occurs at temperatures between 400°C and 800°C.
- Catalytic Cracking: Catalytic cracking occurs in the presence of a catalyst, which lowers the activation energy required for the cracking reactions. The process typically occurs at temperatures between 450°C and 550°C and at pressures slightly above atmospheric.
-
Applications:
- Pyrolysis: Pyrolysis is commonly used for biomass conversion, waste treatment, and the production of biofuels. It is also used in the recycling of plastics and tires, converting them into useful products like oil, gas, and char.
- Catalytic Cracking: Catalytic cracking is primarily used in the oil and gas industry to convert heavy hydrocarbon fractions into lighter, more valuable products such as gasoline, diesel, and olefins. It is a key process in petroleum refining.
-
Products:
- Pyrolysis: The products of pyrolysis include bio-oil, syngas, and biochar when applied to biomass. When applied to plastics or tires, the products can include oil, gas, and carbon black.
- Catalytic Cracking: The products of catalytic cracking are primarily lighter hydrocarbons, including gasoline, diesel, and olefins, which are valuable in the petrochemical industry.
-
Catalyst Involvement:
- Pyrolysis: Pyrolysis does not involve the use of a catalyst. The decomposition is driven solely by heat.
- Catalytic Cracking: Catalytic cracking relies on the presence of a catalyst, such as zeolites, to facilitate the cracking reactions. The catalyst not only lowers the required temperature and pressure but also helps in controlling the product distribution.
-
Energy Requirements:
- Pyrolysis: Pyrolysis generally requires higher temperatures compared to catalytic cracking, as it relies solely on thermal energy to break down the molecules.
- Catalytic Cracking: Catalytic cracking operates at lower temperatures and pressures due to the presence of a catalyst, making it more energy-efficient for large-scale industrial applications.
-
Environmental Impact:
- Pyrolysis: Pyrolysis can be considered environmentally friendly when used for waste treatment and biomass conversion, as it can reduce the volume of waste and produce renewable energy sources. However, it can also produce emissions if not properly controlled.
- Catalytic Cracking: Catalytic cracking is a key process in the petroleum industry, which has significant environmental impacts due to the extraction, refining, and combustion of fossil fuels. However, the process itself is optimized to maximize the yield of valuable products while minimizing waste.
In summary, while both pyrolysis and catalytic cracking involve the thermal decomposition of large molecules into smaller ones, they differ in their mechanisms, reaction environments, and applications. Pyrolysis is a thermal process used primarily for biomass and waste treatment, while catalytic cracking is a chemical process used in the petroleum industry to produce valuable fuels and chemicals. The presence of a catalyst in catalytic cracking allows for more efficient and controlled reactions at lower temperatures and pressures compared to pyrolysis.
Summary Table:
Aspect | Pyrolysis | Catalytic Cracking |
---|---|---|
Definition | Thermal decomposition in the absence of oxygen. | Chemical process using heat, pressure, and a catalyst. |
Reaction Environment | Oxygen-free, temperatures: 400°C–800°C. | Catalyst presence, temperatures: 450°C–550°C, slightly above atmospheric. |
Applications | Biomass conversion, waste treatment, biofuel production. | Oil and gas industry, petroleum refining. |
Products | Bio-oil, syngas, biochar (biomass); oil, gas, carbon black (plastics/tires). | Gasoline, diesel, olefins. |
Catalyst Involvement | No catalyst. | Uses catalysts like zeolites. |
Energy Requirements | Higher temperatures required. | Lower temperatures and pressures due to catalyst. |
Environmental Impact | Environmentally friendly for waste treatment; emissions if uncontrolled. | Significant environmental impact due to fossil fuel processing. |
Want to learn more about pyrolysis and catalytic cracking? Contact our experts today for tailored insights!