TiAlN (Titanium Aluminum Nitride) and AlTiN (Aluminum Titanium Nitride) are both advanced coatings used to enhance the performance of tools and components, particularly in high-stress environments. While they share similarities in composition and application, their differences lie in the ratio of titanium (Ti) to aluminum (Al), which affects their mechanical, thermal, and tribological properties. TiAlN typically has a higher titanium content, offering better oxidation resistance and hardness, while AlTiN, with a higher aluminum content, provides superior thermal stability and wear resistance. These differences make each coating suitable for specific applications depending on the operational demands.
Key Points Explained:
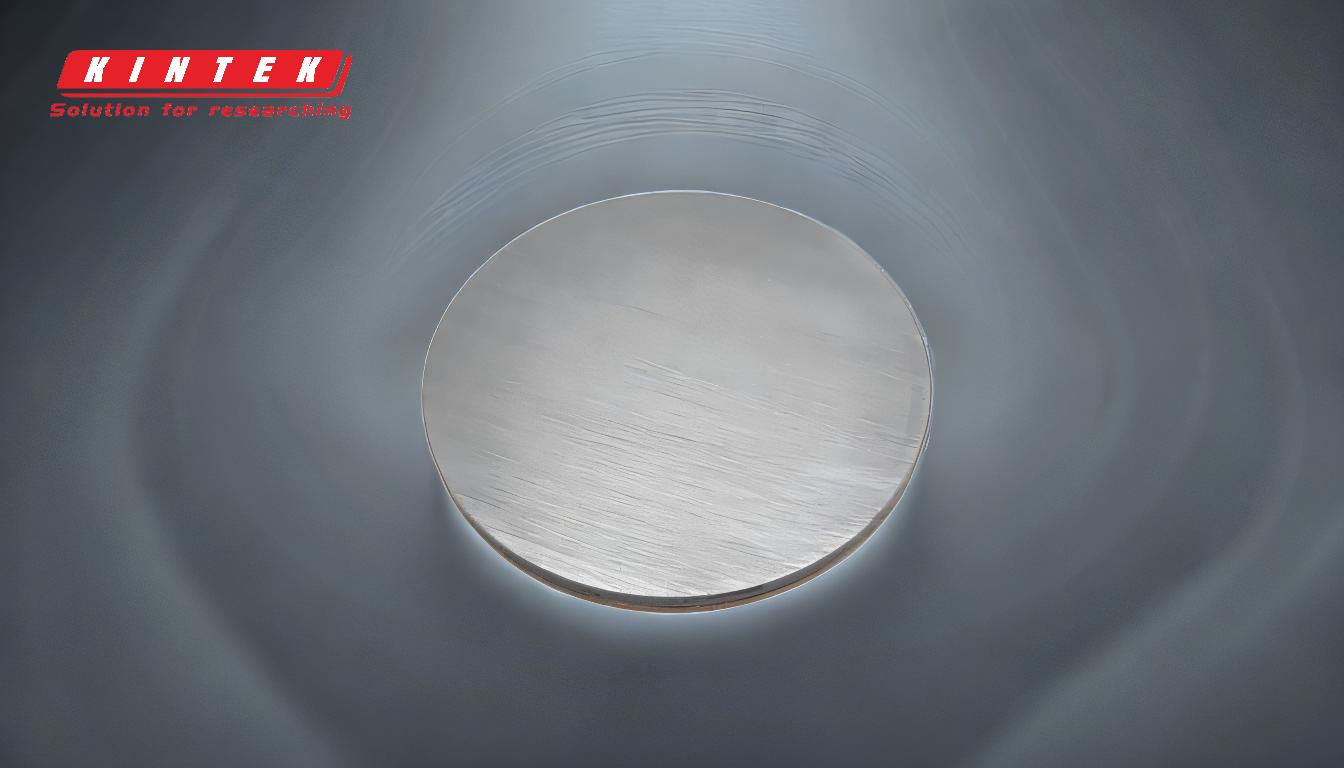
-
Composition and Structure:
- TiAlN: This coating has a higher titanium-to-aluminum ratio, typically around 50:50 or slightly more titanium. The higher titanium content contributes to its excellent oxidation resistance and hardness.
- AlTiN: In contrast, AlTiN has a higher aluminum content, often exceeding 60%. The increased aluminum content enhances its thermal stability and wear resistance, making it suitable for high-temperature applications.
-
Mechanical Properties:
- Hardness: TiAlN coatings are known for their high hardness, which is beneficial for applications involving significant wear and friction. The nanostructured TiAlN coatings, in particular, offer superior hardness compared to traditional TiN coatings.
- Wear Resistance: AlTiN, with its higher aluminum content, provides better wear resistance, especially in high-temperature environments. This makes it ideal for cutting tools and other components subjected to extreme conditions.
-
Thermal Properties:
- Oxidation Resistance: TiAlN coatings exhibit excellent oxidation resistance due to the formation of a stable aluminum oxide layer at high temperatures. This property is crucial for tools operating in oxidative environments.
- Thermal Stability: AlTiN coatings offer superior thermal stability, maintaining their mechanical properties even at elevated temperatures. This makes them suitable for high-speed machining and other high-temperature applications.
-
Tribological Properties:
- Friction and Wear: Both coatings enhance tribological properties, but AlTiN's higher aluminum content provides better performance in reducing friction and wear under high-stress conditions.
- Surface Roughness: Both TiAlN and AlTiN coatings improve surface roughness, contributing to smoother operation and reduced wear over time.
-
Application Suitability:
- TiAlN: Best suited for applications requiring high hardness and oxidation resistance, such as in cutting tools and molds that operate at moderate temperatures.
- AlTiN: More appropriate for high-temperature applications, such as high-speed machining and aerospace components, where thermal stability and wear resistance are critical.
-
Cost-Efficiency:
- Both coatings are cost-effective compared to other advanced coatings, but the choice between TiAlN and AlTiN should be based on the specific operational requirements to ensure optimal performance and longevity.
In summary, while TiAlN and AlTiN coatings share many beneficial properties, their differences in composition and resulting mechanical, thermal, and tribological properties make each uniquely suited for specific applications. Understanding these differences is crucial for selecting the right coating to enhance the performance and durability of tools and components in various industrial applications.
Summary Table:
Property | TiAlN | AlTiN |
---|---|---|
Composition | Higher titanium content (~50:50 ratio) | Higher aluminum content (>60%) |
Hardness | High hardness, excellent wear resistance | Superior wear resistance in high temps |
Oxidation Resistance | Excellent due to stable oxide layer | Good, but less than TiAlN |
Thermal Stability | Moderate | Superior, ideal for high-temp apps |
Applications | Cutting tools, molds (moderate temps) | High-speed machining, aerospace |
Need help choosing the right coating for your tools? Contact our experts today!