The effect of ball size in ball milling is a critical factor that influences the efficiency and outcome of the grinding process. Smaller balls are generally more effective for producing finer particles due to their increased surface area and ability to create more collisions per unit time. However, the optimal ball size also depends on the material being milled, the mill's rotational speed, and the desired particle size. Larger balls may be more suitable for coarse grinding, while smaller balls are preferred for fine grinding. The interplay between ball size, mill speed, and grinding time must be carefully balanced to achieve the desired particle size distribution.
Key Points Explained:
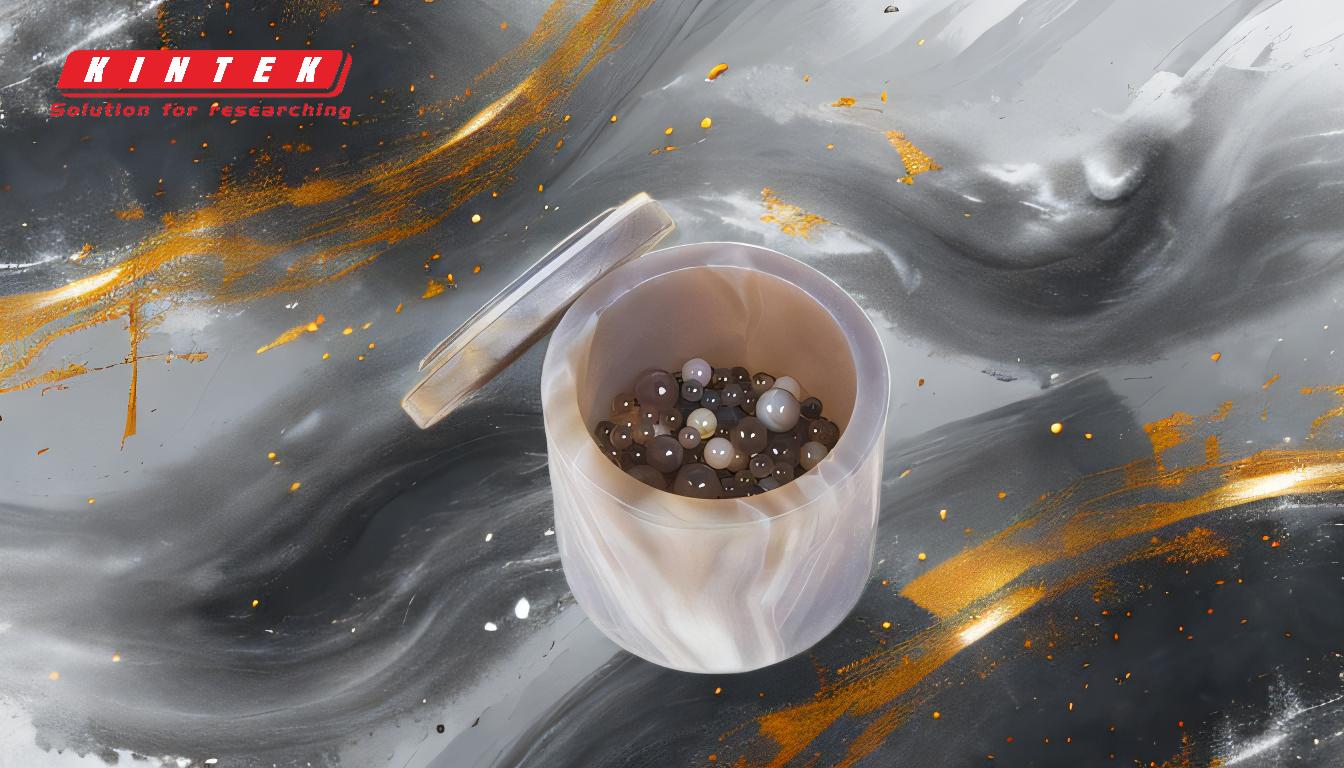
-
Impact of Ball Size on Grinding Efficiency
- Smaller Balls: Smaller balls have a larger surface area relative to their volume, which increases the number of collisions and the grinding efficiency. This makes them ideal for producing finer particles.
- Larger Balls: Larger balls are more effective for coarse grinding because they can impart more energy per collision, breaking down larger particles more effectively.
-
Relationship Between Ball Size and Particle Size
- Finer Particles: To achieve finer particles, smaller balls are generally used. This is because smaller balls can create more contact points and collisions, leading to more effective size reduction.
- Coarse Particles: For coarser particles, larger balls may be more appropriate as they can deliver more impact force, which is necessary for breaking down larger particles.
-
Interaction with Mill Speed
- Low Speed: At low speeds, balls tend to slide or roll over each other, resulting in minimal size reduction. This is less dependent on ball size but more on the lack of kinetic energy.
- High Speed: At high speeds, balls are thrown against the cylinder wall due to centrifugal force, which can prevent effective grinding regardless of ball size.
- Optimal Speed: At normal speeds, balls are carried to the top of the mill and then cascade down, creating the most effective grinding action. The optimal ball size for this speed will depend on the desired particle size.
-
Grinding Time Considerations
- Longer Grinding Times: Smaller balls generally require longer grinding times to achieve the desired particle size, especially for very fine particles. This is because the smaller balls need more time to create enough collisions to break down the material effectively.
- Shorter Grinding Times: Larger balls may achieve the desired particle size in a shorter time for coarser grinding, as they can deliver more energy per collision.
-
Material-Specific Considerations
- Hardness and Brittleness: The hardness and brittleness of the material being milled can influence the optimal ball size. Harder materials may require larger balls to achieve effective grinding, while more brittle materials may be more effectively ground with smaller balls.
- Feed Size: The initial size of the material being fed into the mill can also influence the choice of ball size. Larger feed sizes may require larger balls to break down the material initially, followed by smaller balls for finer grinding.
-
Practical Implications for Equipment and Consumable Purchasers
- Cost Efficiency: Purchasers should consider the cost efficiency of using different ball sizes. Smaller balls may require longer grinding times, which could increase energy costs, but they may also produce higher-quality fine particles.
- Operational Flexibility: Having a range of ball sizes available can provide operational flexibility, allowing the mill to be adjusted for different materials and desired particle sizes.
- Maintenance and Wear: Smaller balls may wear out faster due to the increased number of collisions, potentially increasing maintenance costs. Larger balls may be more durable but could also cause more wear on the mill lining.
In summary, the effect of ball size in ball milling is multifaceted, involving considerations of grinding efficiency, particle size, mill speed, grinding time, material properties, and practical operational factors. Understanding these interactions is crucial for optimizing the milling process and achieving the desired outcomes.
Summary Table:
Factor | Smaller Balls | Larger Balls |
---|---|---|
Grinding Efficiency | Higher due to increased collisions | Lower but effective for coarse grinding |
Particle Size | Ideal for fine particles | Suitable for coarse particles |
Mill Speed | Optimal at normal speeds | Optimal at normal speeds |
Grinding Time | Longer for finer particles | Shorter for coarse grinding |
Material Hardness | Better for brittle materials | Better for harder materials |
Cost Efficiency | Higher energy costs, finer output | Lower energy costs, coarser output |
Maintenance | Higher wear and maintenance | Durable but may wear mill lining |
Ready to optimize your ball milling process? Contact our experts today for tailored solutions!