The efficiency of a ball mill is maximized when it operates at its normal speed, where the balls are carried to the top of the mill and then cascade down, achieving maximum size reduction. This optimal speed ensures that the grinding medium (balls) effectively impacts and grinds the material. Additionally, factors such as the drum diameter-to-length ratio (optimal L:D ratio of 1.56–1.64), ball filling and sizes, rotation speed, and timely removal of ground product play critical roles in determining the mill's efficiency. Properly balancing these factors ensures optimal grinding performance and productivity.
Key Points Explained:
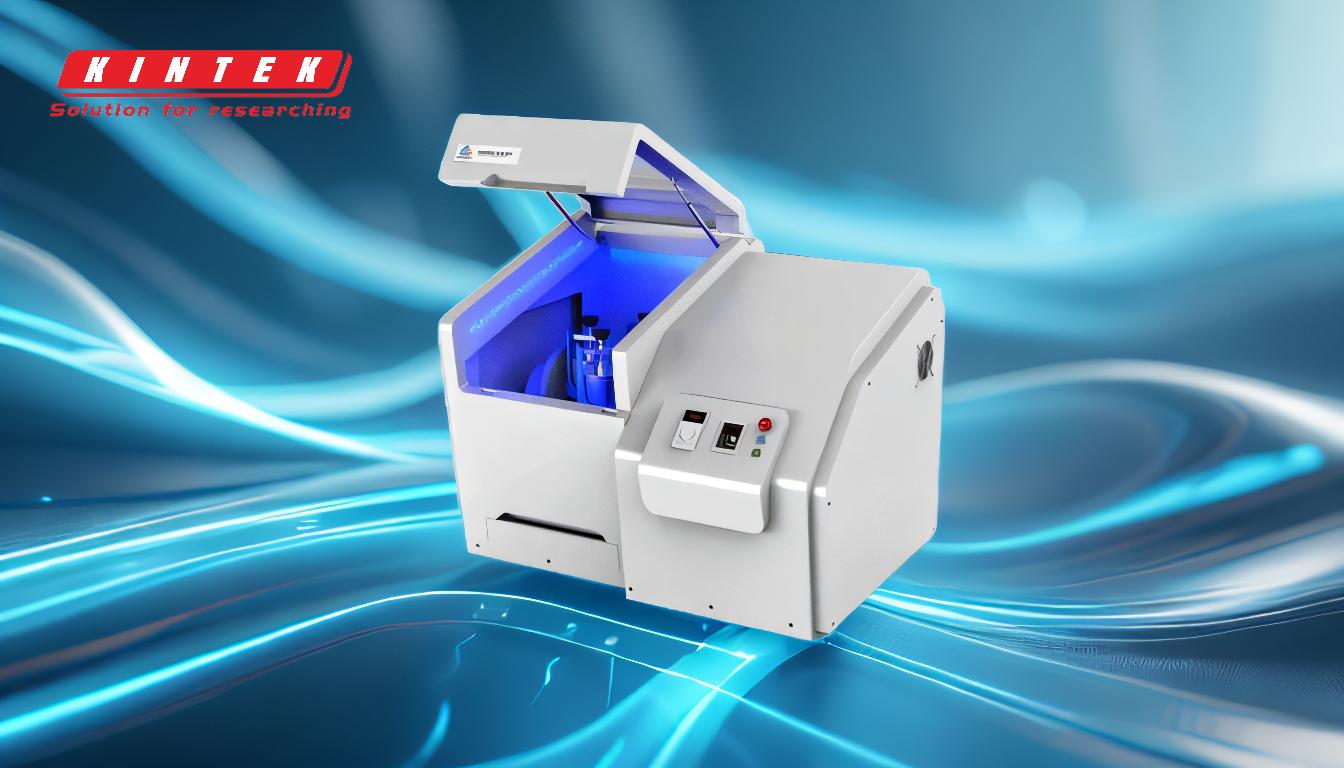
-
Optimal Rotation Speed:
- The efficiency of a ball mill is highly dependent on its rotation speed. At normal speed, the balls are lifted to a certain height and then cascade down, creating a grinding action that maximizes size reduction.
- At low speeds, the balls slide or roll over each other, resulting in minimal grinding. At high speeds, centrifugal force causes the balls to stick to the mill wall, preventing effective grinding. Therefore, operating at the normal speed is critical for achieving maximum efficiency.
-
Drum Diameter-to-Length Ratio:
- The L:D ratio (length-to-diameter ratio) of the drum significantly affects grinding efficiency. The optimal range is 1.56–1.64. This ratio ensures an even distribution of grinding forces and prevents overloading or underutilization of the mill.
-
Ball Filling and Sizes:
- The filling ratio (percentage of the mill volume filled with grinding medium) and the size of the balls are crucial. Proper ball filling ensures sufficient grinding action, while the size of the balls should match the material being ground to achieve effective size reduction.
-
Physical-Chemical Properties of Feed Material:
- The nature of the material being ground (e.g., hardness, density, and moisture content) influences grinding efficiency. Softer materials grind more easily, while harder materials require more energy and time.
-
Armor Surface Shape:
- The shape and texture of the mill's interior (armor surface) affect the movement of the balls and the grinding action. A well-designed armor surface promotes efficient cascading of the balls.
-
Timely Removal of Ground Product:
- Efficient removal of ground material prevents over-grinding and ensures continuous operation. Delayed removal can lead to energy waste and reduced productivity.
-
Residence Time and Feed Rate:
- The residence time of the material in the mill chamber and the feed rate must be optimized. Too short a residence time may result in incomplete grinding, while too long a residence time can lead to over-grinding and energy inefficiency.
-
Rotation Speed and Centrifugal Force:
- The rotation speed must be carefully controlled to avoid excessive centrifugal force, which can cause the balls to stick to the mill wall, reducing grinding efficiency. The normal speed ensures the balls cascade effectively.
-
Grinding Medium and Material Compatibility:
- The type and size of the grinding medium (balls) should match the material being ground. Larger balls are suitable for coarser materials, while smaller balls are better for finer grinding.
-
Mill Filling Ratio:
- The filling ratio (percentage of the mill volume filled with grinding medium) should be optimized. Overfilling can reduce grinding efficiency, while underfilling may lead to insufficient grinding action.
By carefully balancing these factors—rotation speed, L:D ratio, ball filling and sizes, material properties, and operational parameters—the efficiency of a ball mill can be maximized, ensuring optimal grinding performance and productivity.
Summary Table:
Factor | Optimal Range/Consideration |
---|---|
Rotation Speed | Operate at normal speed for effective cascading of balls. |
L:D Ratio | 1.56–1.64 for even grinding force distribution. |
Ball Filling Ratio | Optimize filling ratio to ensure sufficient grinding action. |
Ball Sizes | Match ball sizes to material coarseness (larger balls for coarse, smaller for fine grinding). |
Material Properties | Consider hardness, density, and moisture content for efficient grinding. |
Armor Surface Shape | Use a well-designed surface for efficient ball movement. |
Ground Product Removal | Timely removal prevents over-grinding and energy waste. |
Residence Time & Feed Rate | Optimize to avoid incomplete or over-grinding. |
Mill Filling Ratio | Avoid overfilling or underfilling for consistent grinding efficiency. |
Ready to optimize your ball mill performance? Contact our experts today for tailored solutions!