Leakage in a vacuum system is a critical issue that can significantly impact the performance and efficiency of the system. Leaks can lead to a variety of operational problems, including poor pumping, poor sealing, and difficulty in maintaining the desired vacuum level. These issues can compromise the quality of processes that rely on a controlled vacuum environment, such as in vacuum furnaces. Ensuring zero leakage is essential for maintaining the integrity of the system and achieving optimal performance.
Key Points Explained:
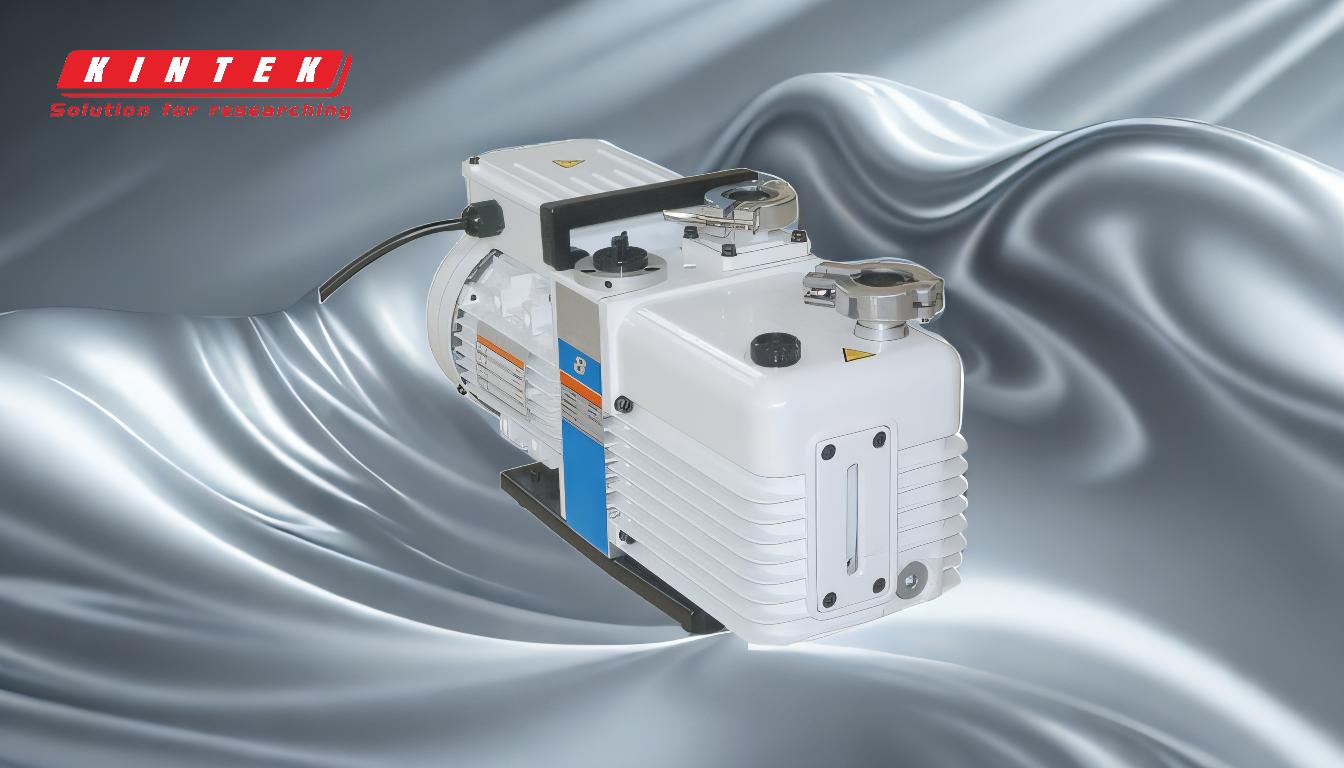
-
Impact on Vacuum Furnace Performance:
- Poor Pumping: Leaks can cause the vacuum pump to work inefficiently, leading to longer pump-down times and higher energy consumption.
- Poor Sealing: Leaks compromise the sealing integrity of the vacuum system, allowing contaminants to enter and potentially damaging sensitive components.
- Poor Ultimate Vacuum: The presence of leaks prevents the system from achieving the desired vacuum level, which is crucial for many high-precision processes.
-
Operational Errors:
- Difficulty in Discharging Normal Release Gas: Leaks can interfere with the normal operation of gas discharge systems, leading to improper venting and potential safety hazards.
- Backflow: Leaks can cause backflow, where gases or contaminants re-enter the system, leading to contamination and reduced process quality.
-
Importance of Zero Leakage:
- System Integrity: Zero leakage is essential for maintaining the integrity of the vacuum system, ensuring that it operates as intended without any external interference.
- Process Quality: Many processes, such as those in vacuum furnaces, require a controlled environment free from contaminants. Leaks can introduce impurities that degrade the quality of the final product.
-
Detection and Prevention:
- Leak Detection: Regular leak detection is crucial for identifying and addressing any leaks in the system. Techniques such as helium leak detection can be used to pinpoint the exact location of leaks.
- Preventive Maintenance: Implementing a robust preventive maintenance program can help in early detection and rectification of leaks, ensuring the system remains leak-free and operates efficiently.
In summary, leakage in a vacuum system can have severe consequences on the performance and quality of processes that rely on a controlled vacuum environment. Ensuring zero leakage through regular detection and preventive maintenance is essential for maintaining system integrity and achieving optimal operational efficiency.
Summary Table:
Impact of Leakage | Consequences |
---|---|
Poor Pumping | Longer pump-down times, higher energy consumption |
Poor Sealing | Contaminant entry, damage to sensitive components |
Poor Ultimate Vacuum | Inability to achieve desired vacuum levels, affecting precision processes |
Operational Errors | Difficulty in gas discharge, backflow, contamination, and safety hazards |
Zero Leakage Importance | Maintains system integrity, ensures process quality, and prevents contamination |
Detection & Prevention | Regular leak detection and preventive maintenance for efficient operation |
Ensure your vacuum system operates at peak performance—contact our experts today for leak detection and maintenance solutions!