Bio-oil is primarily composed of water and a wide range of oxygenated organic compounds derived from biomass. The main components include alcohols, aldehydes, carboxylic acids, esters, furans, pyrans, ketones, monosaccharides, anhydrosugars, and phenolic compounds. These oxygenated compounds contribute to bio-oil's high thermal instability and relatively low heating value compared to conventional fuels. Additionally, bio-oil contains reactive molecules and oligomeric species with high molecular weights, making it chemically unstable even at room temperature. The water content in bio-oil typically ranges from 14–33 wt%, which is difficult to remove and can lead to phase separation at higher concentrations. Overall, the complex mixture of oxygenated compounds and water defines the chemical composition and properties of bio-oil.
Key Points Explained:
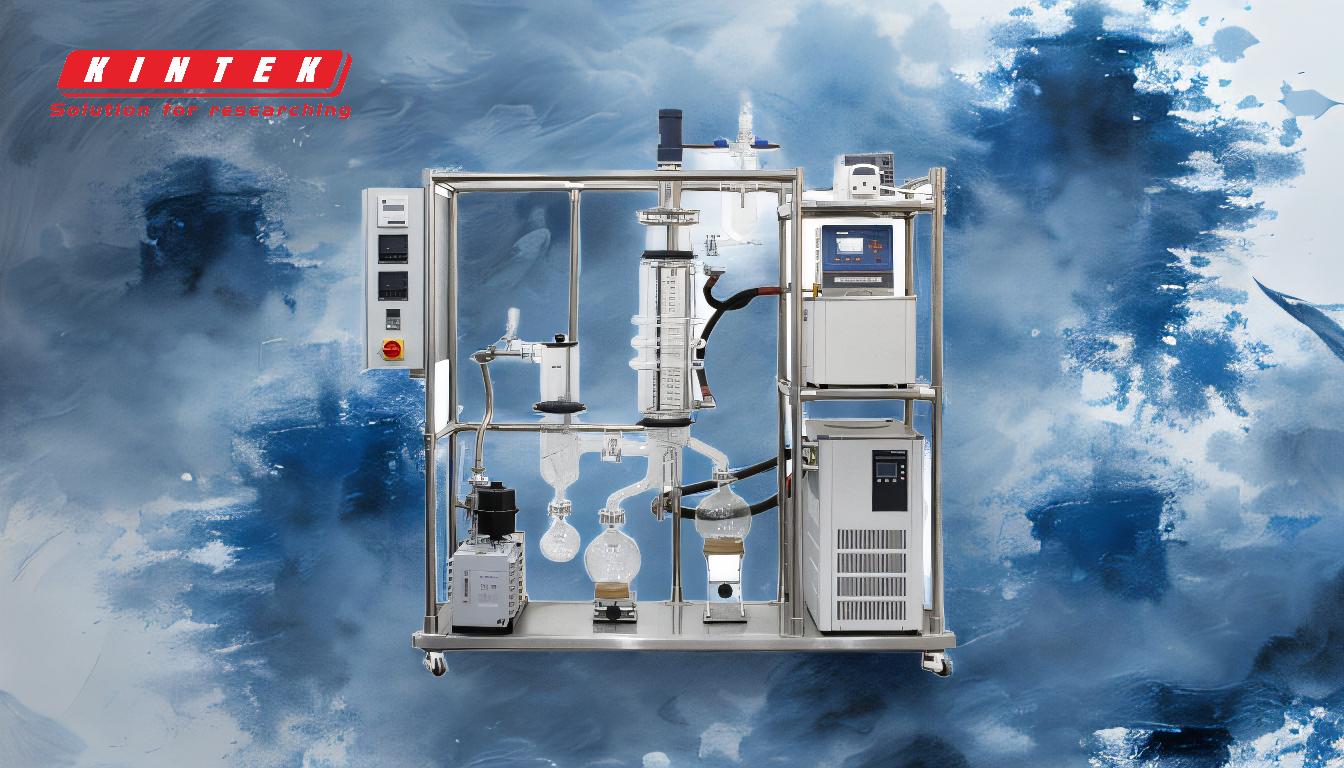
-
Primary Components of Bio-oil:
- Bio-oil is mainly composed of water (14–33 wt%) and oxygenated organic compounds derived from biomass.
- These organic compounds include:
- Alcohols, aldehydes, and carboxylic acids.
- Esters, furans, pyrans, and ketones.
- Monosaccharides, anhydrosugars, and phenolic compounds.
- The presence of these compounds is a result of the breakdown of carbohydrates and lignin in biomass during the pyrolysis or liquefaction process.
-
Oxygenated Compounds and Their Impact:
- The high concentration of oxygenated compounds is a defining feature of bio-oil.
- These compounds contribute to bio-oil's high thermal instability and low heating value (15–22 MJ/kg), which is significantly lower than conventional fuel oil (43–46 MJ/kg).
- The oxygenated nature of bio-oil makes it reactive and prone to polymerization, leading to instability even at room temperature.
-
Water Content in Bio-oil:
- Bio-oil contains a significant amount of water (14–33 wt%), which is difficult to remove using conventional methods like distillation.
- High water content can lead to phase separation in bio-oil, particularly when the water concentration exceeds certain thresholds.
- The presence of water also lowers the energy density of bio-oil, further reducing its heating value.
-
Complex Mixture of Organic Components:
- Bio-oil is not a single compound but a complex mixture of hundreds of organic components, including:
- Acids, alcohols, ketones, and furans.
- Phenols, ethers, esters, and sugars.
- Aldehydes, alkenes, and nitrogen compounds.
- This complexity makes bio-oil challenging to refine and utilize directly as a fuel.
- Bio-oil is not a single compound but a complex mixture of hundreds of organic components, including:
-
Reactive Molecules and Oligomeric Species:
- Bio-oil contains reactive molecules and oligomeric species with molecular weights larger than 5000.
- These high-molecular-weight compounds contribute to the instability of bio-oil, as they can undergo further reactions, leading to changes in viscosity and composition over time.
-
Implications for Use and Processing:
- The composition of bio-oil makes it unsuitable for direct use in conventional engines or boilers without significant upgrading.
- Upgrading processes, such as hydrodeoxygenation or catalytic cracking, are often required to reduce the oxygen content and improve stability.
- The high water content and complex mixture of compounds also pose challenges for storage and transportation, as bio-oil can degrade or separate over time.
In summary, the main component of bio-oil is a mixture of water and oxygenated organic compounds derived from biomass. These compounds, including alcohols, aldehydes, carboxylic acids, and phenolic compounds, contribute to bio-oil's unique properties, such as thermal instability and low heating value. The presence of reactive molecules and oligomeric species further complicates its use, necessitating advanced processing techniques to make it a viable alternative fuel.
Summary Table:
Key Component | Description |
---|---|
Water Content | 14–33 wt%, difficult to remove, can cause phase separation. |
Oxygenated Compounds | Alcohols, aldehydes, carboxylic acids, esters, furans, pyrans, ketones, etc. |
Heating Value | 15–22 MJ/kg, lower than conventional fuels (43–46 MJ/kg). |
Reactive Molecules | Oligomeric species with high molecular weights, contributing to instability. |
Processing Challenges | Requires hydrodeoxygenation or catalytic cracking for stability and usability. |
Want to learn more about bio-oil and its applications? Contact our experts today for tailored solutions!