The manufacturing process of rubber involves several key stages, starting with the extraction of latex from rubber trees and culminating in the production of finished rubber products. The process includes steps such as compounding, extrusion, calendering, vulcanization, and latex processing. Each stage plays a critical role in transforming raw latex into durable and functional rubber materials. The methods used to shape and cure rubber, such as molding, extrusion, and vulcanization, are tailored to the specific requirements of the final product. Understanding these processes is essential for producing high-quality rubber products used in various industries.
Key Points Explained:
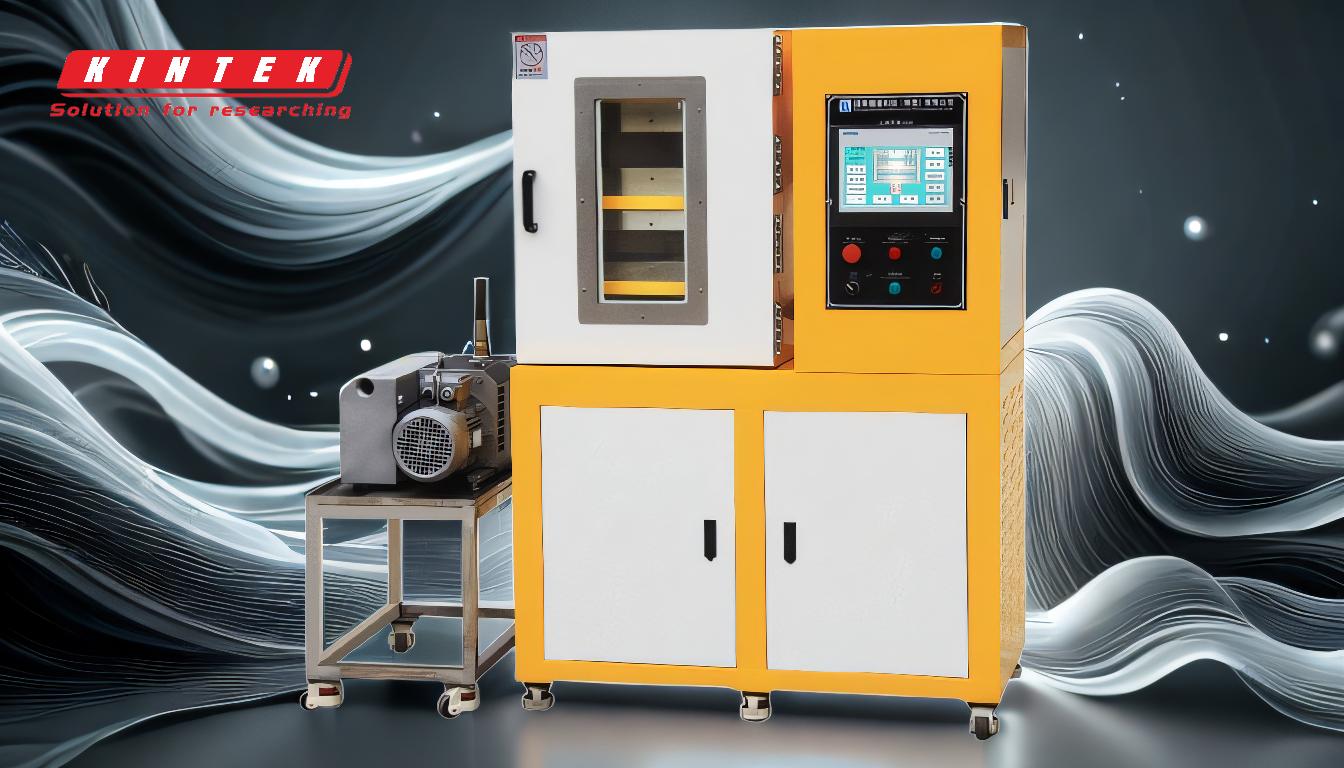
-
Latex Extraction and Initial Processing
- The process begins with the extraction of latex sap from rubber trees. Professional tappers harvest the sap, which is then filtered and packaged into drums.
- The filtered latex is transported to factories, where it is processed into slabs using an acidic additive. This step prepares the raw material for further processing.
- Latex processing involves dispersing rubber particles into an aqueous phase, which is essential for creating products like gloves or balloons.
-
Compounding
- Compounding is the process of mixing raw rubber with additives such as fillers, plasticizers, and curing agents. This step enhances the properties of the rubber, such as elasticity, durability, and resistance to heat or chemicals.
- The compounded rubber is then ready for shaping and curing.
-
Shaping Processes
- Extrusion: Rubber is forced through a die to create continuous shapes like tubes, hoses, or seals.
- Calendering: Rubber is passed through rollers to produce thin sheets or films, often used in industrial applications. This process is facilitated by a rubber calender.
-
Molding: Rubber is shaped using molds. Common methods include:
- Compression Molding: Uncured rubber is pressed between heated molds.
- Injection Molding: Preheated rubber is forced into a mold cavity by a rotating screw, ideal for complex shapes.
-
Vulcanization
- Vulcanization is a critical step that involves curing the rubber to improve its strength, elasticity, and resistance to wear and tear. This process is often carried out using a rubber vulcanizer.
- Methods include:
- Open Vulcanization: Rubber is cured in open molds or directly in hot air.
- Continuous Vulcanization: Rubber products are cured as they move through a heated chamber, suitable for long, continuous shapes.
- Latex products, such as gloves, undergo vulcanization using steam to set their final form.
-
Latex Processing
- Latex dipping machines use porcelain or aluminum molds dipped into the latex compound.
- The dipped molds are washed, air-dried, and vulcanized using steam to create products like gloves or balloons.
-
Polyurethane Production
- Polyurethane is a synthetic rubber alternative produced through chemical reactions. It offers unique properties like high flexibility and resistance to abrasion, making it suitable for specialized applications.
-
Final Product Finishing
- After vulcanization, rubber products may undergo additional finishing processes, such as trimming, coating, or quality inspection, to ensure they meet specific standards.
By following these steps, manufacturers can produce a wide range of rubber products tailored to various industrial and consumer needs. Each stage of the process is carefully controlled to ensure the final product meets the desired performance and quality standards.
Summary Table:
Stage | Key Process | Purpose |
---|---|---|
Latex Extraction | Harvesting and filtering latex sap from rubber trees | Prepares raw material for processing |
Compounding | Mixing rubber with additives like fillers and curing agents | Enhances elasticity, durability, and resistance |
Shaping Processes | Extrusion, calendering, molding (compression/injection) | Shapes rubber into desired forms |
Vulcanization | Curing rubber using heat or steam | Improves strength, elasticity, and wear resistance |
Latex Processing | Dipping molds into latex, washing, and vulcanizing | Produces latex-based products like gloves and balloons |
Polyurethane Production | Chemical reactions to create synthetic rubber | Offers flexibility and abrasion resistance for specialized applications |
Final Product Finishing | Trimming, coating, and quality inspection | Ensures products meet performance and quality standards |
Need high-quality rubber products? Contact our experts today to learn more!