The maximum size reduction in a ball mill is influenced by a combination of factors, including the speed of rotation, the size and type of grinding medium, the nature of the material being ground, and the operational parameters of the mill. Optimal size reduction occurs when the mill operates at normal speed, allowing balls to cascade and impact the material effectively. Smaller balls and longer grinding times are generally required to achieve finer particle sizes. The efficiency of size reduction is also affected by the filling ratio of the mill, the hardness of the material, and the physical-chemical properties of the feed material. Understanding these factors is crucial for achieving the desired particle size and maximizing the grinding performance of a ball mill.
Key Points Explained:
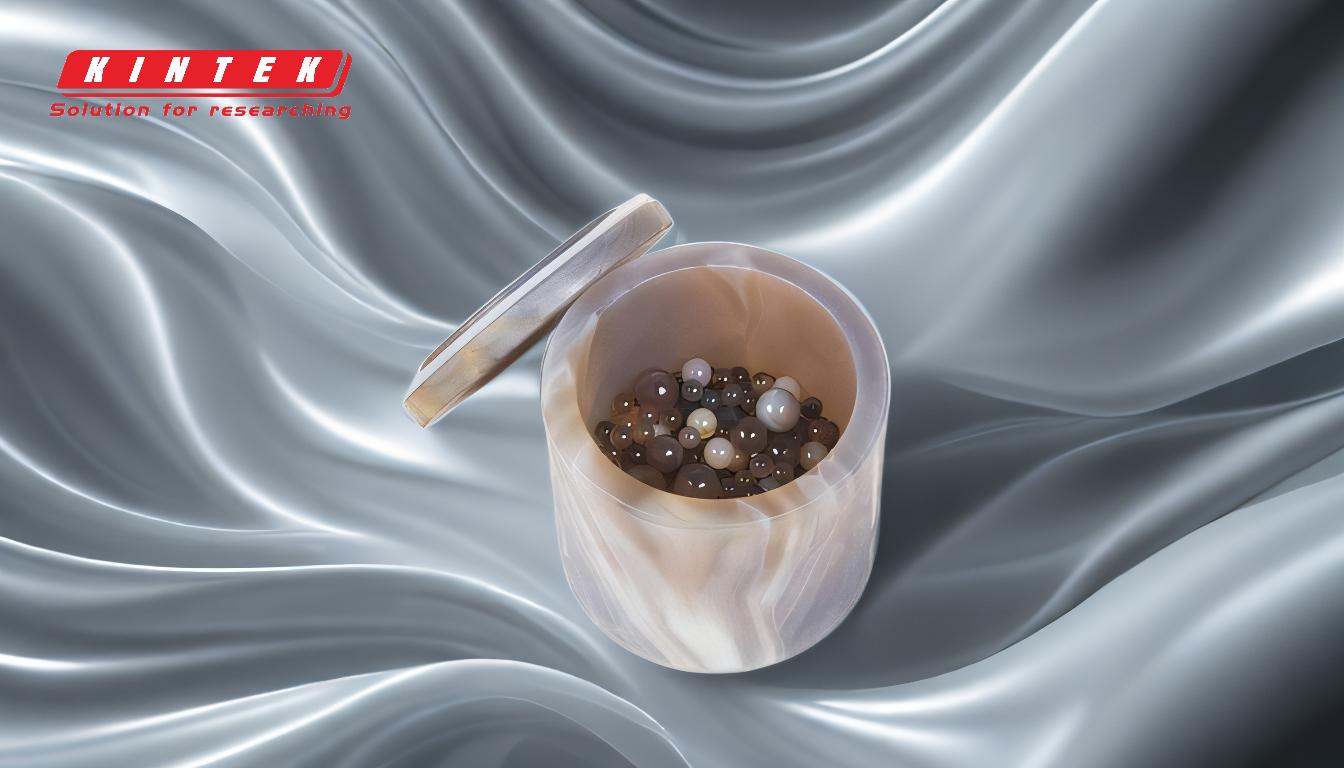
-
Speed of Rotation:
- The speed at which the ball mill rotates plays a critical role in size reduction.
- Low Speed: At low speeds, the balls tend to slide or roll over one another, resulting in minimal size reduction.
- High Speed: At high speeds, the balls are thrown against the cylinder wall due to centrifugal force, which prevents effective grinding.
- Normal Speed: At normal speeds, the balls are carried to the top of the mill and then cascade down, impacting the material and achieving maximum size reduction.
-
Grinding Medium:
- The size, density, and number of balls used in the mill significantly affect the grinding efficiency.
- Smaller Balls: Smaller balls are generally more effective at producing finer particles because they have a larger surface area relative to their volume, allowing for more contact points with the material.
- Density and Number: The density and number of balls also influence the energy transfer during grinding. Higher density balls can impart more energy to the material, while a greater number of balls increases the frequency of impacts.
-
Nature of the Material:
- The hardness and physical-chemical properties of the material being ground are crucial factors.
- Hardness: Harder materials require more energy to break down, which can be achieved by using denser balls or increasing the grinding time.
- Physical-Chemical Properties: The material's properties, such as its brittleness or toughness, can affect how easily it fractures under impact.
-
Operational Parameters:
- Several operational parameters influence the grinding performance, including the feed rate, residence time, and filling ratio.
- Feed Rate: The rate at which material is fed into the mill affects the residence time and the degree of grinding. A higher feed rate may reduce the residence time, leading to less effective grinding.
- Residence Time: Longer residence times allow for more thorough grinding, especially when aiming for finer particle sizes.
- Filling Ratio: The percentage of the mill volume filled with grinding medium (balls) affects the efficiency of the grinding process. An optimal filling ratio ensures that there is enough space for the balls to cascade and impact the material effectively.
-
Mill Design:
- The design of the ball mill, including the drum diameter and the ratio of drum diameter to length, also impacts size reduction.
- Drum Diameter: Larger drum diameters can accommodate more balls and provide a greater grinding surface area.
- L:D Ratio: The optimal length-to-diameter (L:D) ratio for a ball mill is typically between 1.56 and 1.64. This ratio ensures that the material is adequately ground without excessive energy consumption.
-
Grinding Time:
- The duration of grinding is directly related to the degree of size reduction.
- Longer Grinding Times: Longer grinding times are generally required to achieve finer particle sizes, as the material undergoes more impacts and abrasion over time.
-
Timely Removal of Ground Product:
- Efficient removal of the ground product from the mill is essential to prevent over-grinding and to maintain the desired particle size distribution.
- Over-Grinding: If the ground product is not removed promptly, it may continue to be ground, leading to excessive fines and energy wastage.
In summary, the maximum size reduction in a ball mill is a complex interplay of factors including rotation speed, grinding medium characteristics, material properties, operational parameters, mill design, and grinding time. Understanding and optimizing these factors are essential for achieving the desired particle size and maximizing the efficiency of the grinding process.
Summary Table:
Factor | Impact on Size Reduction |
---|---|
Speed of Rotation | Normal speed ensures balls cascade effectively, maximizing impact and size reduction. |
Grinding Medium | Smaller balls and higher density improve grinding efficiency for finer particles. |
Nature of Material | Harder materials require more energy; brittleness affects fracture under impact. |
Operational Parameters | Feed rate, residence time, and filling ratio influence grinding efficiency and particle size. |
Mill Design | Optimal drum diameter and L:D ratio ensure effective grinding without excess energy use. |
Grinding Time | Longer grinding times are needed for finer particle sizes. |
Product Removal | Timely removal prevents over-grinding and maintains desired particle size distribution. |
Optimize your ball mill performance—contact our experts today for tailored solutions!