RF reactive sputtering is a sophisticated thin film deposition technique used in various industries, including semiconductors, optics, and solar panels. It combines the principles of sputtering with reactive gases to form compound films on substrates. The process involves bombarding a target material with high-energy ions in a vacuum chamber, causing atoms to be ejected and deposited onto a substrate. The addition of reactive gases like oxygen or nitrogen allows for the formation of compound films, such as oxides or nitrides, which are crucial for specific applications. The mechanism relies on precise control of plasma generation, reactive gas partial pressure, and the interaction between the target material and the reactive gas.
Key Points Explained:
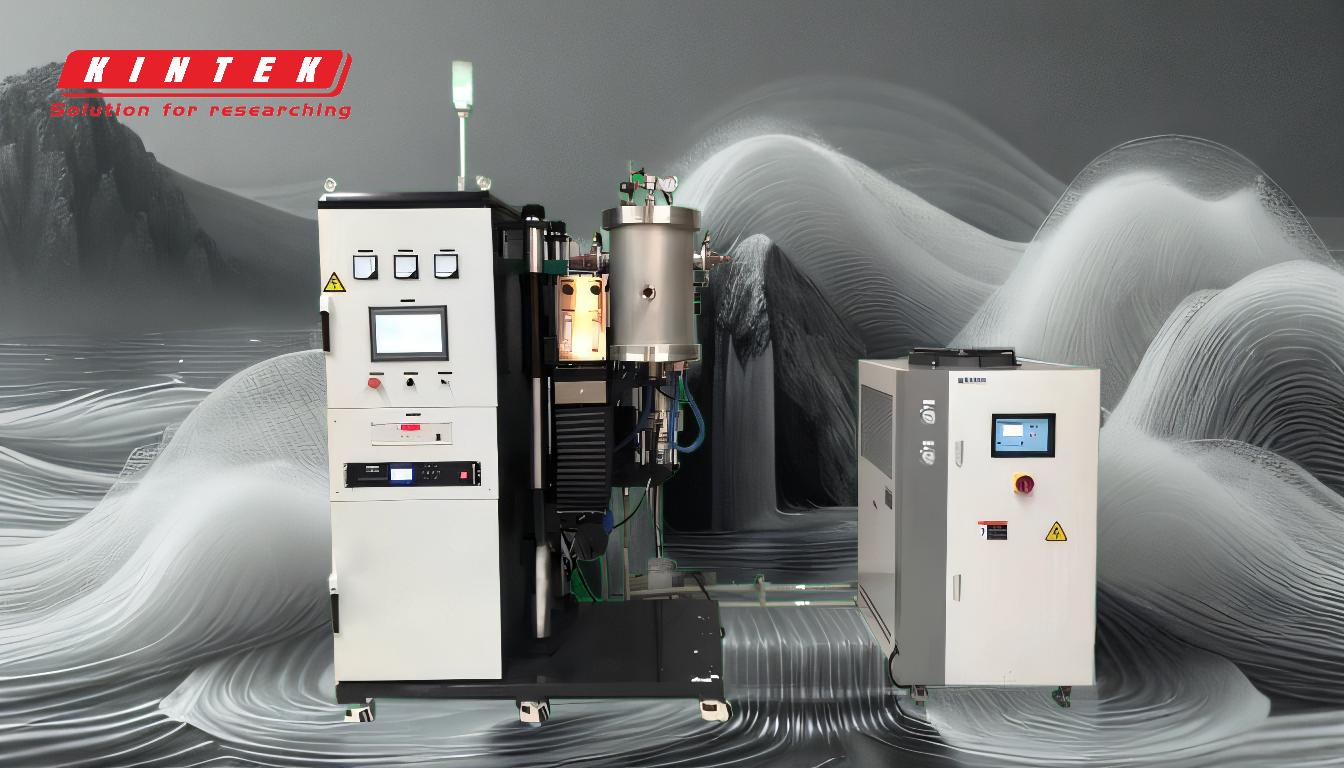
-
Basic Sputtering Mechanism:
- Sputtering involves bombarding a target material with high-energy ions (typically argon) in a vacuum chamber. This bombardment ejects atoms from the target, which then deposit onto a substrate, forming a thin film.
- The process is initiated by creating a plasma, where inert gas atoms are ionized and accelerated toward the target material.
-
Introduction of Reactive Gases:
- In reactive sputtering, a reactive gas (e.g., oxygen or nitrogen) is introduced into the chamber alongside the inert gas.
- The reactive gas chemically interacts with the ejected target atoms, forming compound films such as oxides or nitrides on the substrate.
-
Role of RF (Radio Frequency) Power:
- RF sputtering uses alternating current at radio frequencies to generate plasma. This method is particularly useful for non-conductive target materials, as it prevents charge buildup on the target surface.
- The RF power helps sustain the plasma and ensures efficient sputtering of both conductive and insulating materials.
-
Control of Reactive Gas Partial Pressure:
- The properties of the deposited film are highly dependent on the partial pressure of the reactive gas in the chamber.
- Precise control of the reactive gas flow rate and distribution ensures the desired chemical composition and uniformity of the thin film.
-
Interaction Between Target and Reactive Gas:
- The ejected target atoms react with the reactive gas in the plasma or on the substrate surface, forming the desired compound.
- The reaction kinetics and the distribution of the reactive gas within the chamber play a critical role in determining the film's properties.
-
Advantages of RF Reactive Sputtering:
- This technique is versatile and can be used with a wide range of materials, including insulators, semiconductors, and metals.
- It allows for the deposition of high-quality compound films with precise control over composition and thickness.
-
Applications of RF Reactive Sputtering:
- RF reactive sputtering is widely used in the production of thin films for microelectronics, optical coatings, and solar panels.
- It is particularly valuable for depositing dielectric and nitride films, which are essential in semiconductor manufacturing.
By understanding the interplay between the sputtering process, reactive gases, and RF power, RF reactive sputtering enables the creation of advanced thin films with tailored properties for cutting-edge applications.
Summary Table:
Key Aspect | Description |
---|---|
Basic Sputtering Mechanism | Bombardment of target material with high-energy ions to eject and deposit atoms. |
Reactive Gases | Introduction of gases like oxygen or nitrogen to form compound films. |
RF Power Role | Uses radio frequency to sustain plasma and sputter non-conductive materials. |
Reactive Gas Control | Precise control of gas partial pressure ensures film uniformity and composition. |
Target-Gas Interaction | Ejected atoms react with gases to form oxides, nitrides, or other compounds. |
Advantages | Versatile, high-quality films with precise control over thickness and composition. |
Applications | Used in semiconductors, optics, solar panels, and dielectric film production. |
Discover how RF reactive sputtering can elevate your thin film processes—contact our experts today!