Thin film coating is a critical process in various industries, including electronics, optics, and energy, where precise and uniform layers of material are deposited onto substrates. The methods of thin film coating can be broadly categorized into Physical Vapour Deposition (PVD), Chemical Vapour Deposition (CVD), Atomic Layer Deposition (ALD), and Spray Pyrolysis. Each method has its unique steps, advantages, and applications, making them suitable for different types of materials, film thicknesses, and production requirements. Understanding these methods helps in selecting the right technique for specific applications, ensuring optimal performance and efficiency.
Key Points Explained:
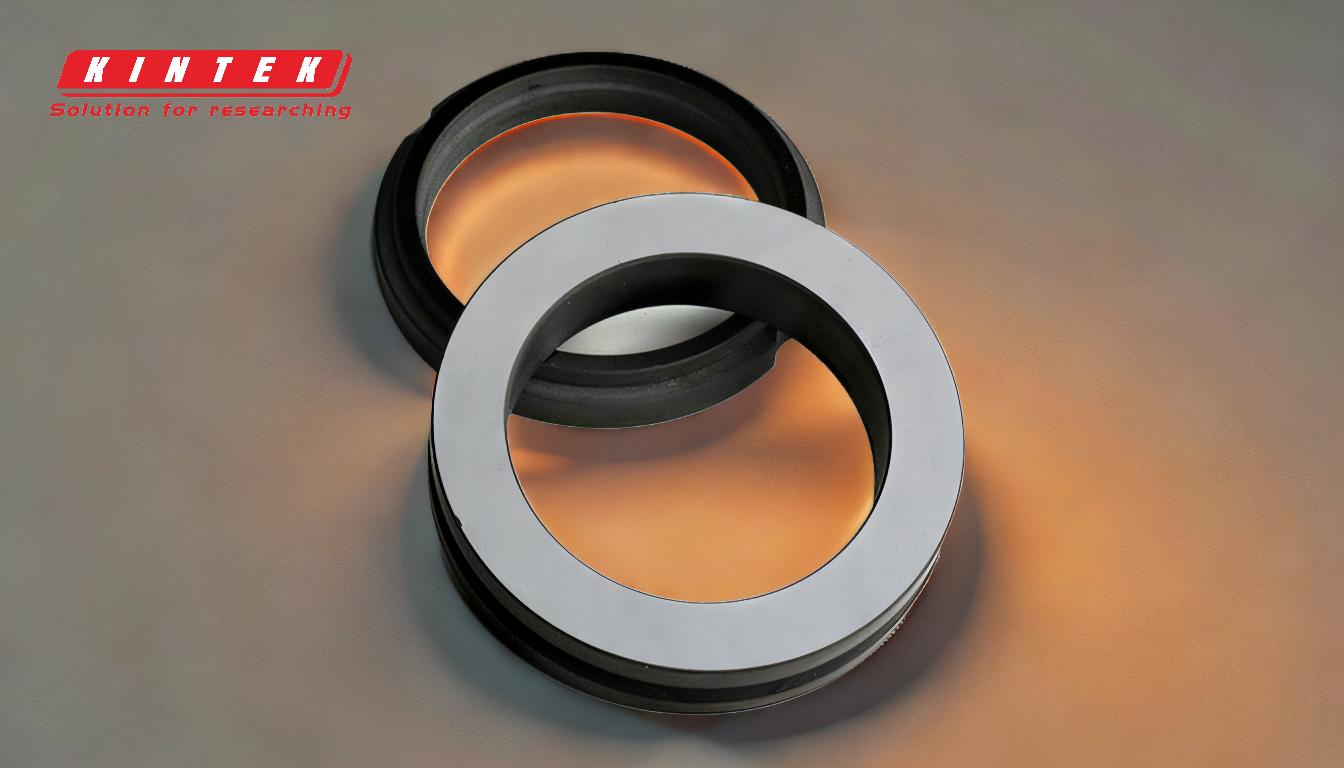
-
Physical Vapour Deposition (PVD):
- Process: PVD involves the evaporation or sputtering of a source material, which then condenses onto the substrate to form a thin film.
- Techniques: Common PVD techniques include evaporation and sputtering. In sputtering, plasma ions bombard the material, causing it to vaporize and deposit onto the surface.
- Applications: PVD is widely used for creating hard coatings, decorative finishes, and functional layers in electronics and optics.
-
Chemical Vapour Deposition (CVD):
- Process: CVD uses chemical reactions to deposit a thin film on the substrate. The process involves introducing reactive gases into a chamber where they react and form a solid film on the substrate.
- Advantages: CVD can produce high-quality, uniform films with excellent adhesion and conformality, making it suitable for complex geometries.
- Applications: CVD is commonly used in semiconductor manufacturing, coating tools, and creating protective layers.
-
Atomic Layer Deposition (ALD):
- Process: ALD deposits films one atomic layer at a time through sequential, self-limiting surface reactions. This allows for precise control over film thickness and composition.
- Advantages: ALD offers exceptional uniformity and conformality, even on high-aspect-ratio structures.
- Applications: ALD is used in advanced semiconductor devices, energy storage, and barrier coatings.
-
Spray Pyrolysis:
- Process: Spray pyrolysis involves spraying a material solution onto the substrate, followed by thermal decomposition to form a thin film.
- Advantages: This method is simple, cost-effective, and suitable for large-area coatings.
- Applications: Spray pyrolysis is used in solar cells, sensors, and transparent conductive coatings.
-
Coating Systems:
- Batch Systems: These systems process multiple wafers simultaneously, making them suitable for high-volume production.
- Cluster Tools: These use multiple chambers for different processes, allowing for sequential processing of single wafers.
- Factory Systems: Designed for high-volume use, these systems are large and integrated into production lines.
- Laboratory Systems: Small and used for low-volume experimental applications, these systems are ideal for research and development.
-
Common Steps in Thin Film Deposition:
- Preparation: Cleaning and preparing the substrate to ensure proper adhesion.
- Deposition: Applying the thin film using one of the methods mentioned above.
- Post-Processing: Annealing or other treatments to improve film properties.
- Inspection: Quality control to ensure the film meets specifications.
-
Selection Criteria:
- Material Properties: The choice of method depends on the material being deposited and the desired film properties.
- Film Thickness: Different methods offer varying levels of control over film thickness.
- Production Speed: Some methods are faster and more suitable for high-volume production.
- Cost: The cost of equipment, materials, and operation varies between methods.
By understanding these key points, one can make informed decisions about the most appropriate thin film coating method for a given application, ensuring optimal performance and efficiency.
Summary Table:
Method | Process Overview | Key Advantages | Applications |
---|---|---|---|
PVD | Evaporation or sputtering of source material onto the substrate. | Hard coatings, decorative finishes, functional layers. | Electronics, optics, decorative finishes. |
CVD | Chemical reactions deposit a thin film on the substrate. | High-quality, uniform films with excellent adhesion and conformality. | Semiconductor manufacturing, protective layers. |
ALD | Deposits films one atomic layer at a time. | Exceptional uniformity and conformality, even on complex structures. | Advanced semiconductors, energy storage, barrier coatings. |
Spray Pyrolysis | Spraying material solution onto the substrate, followed by thermal decomposition. | Simple, cost-effective, suitable for large-area coatings. | Solar cells, sensors, transparent conductive coatings. |
Need help selecting the right thin film coating method for your application? Contact our experts today for personalized guidance!