A batch reactor operates in a non-continuous manner, where all reactants, catalysts, and necessary components are added to the reactor at the start. The reactor is then sealed, and the reaction proceeds over a fixed period without additional inputs or outputs. Temperature, pressure, and mixing are carefully controlled during this phase. Once the reaction reaches the desired conversion or completion, the products are removed. This mode of operation is ideal for small-scale production, complex reactions, or processes involving biological materials, as it allows precise control over reaction conditions and is relatively simple to design and operate.
Key Points Explained:
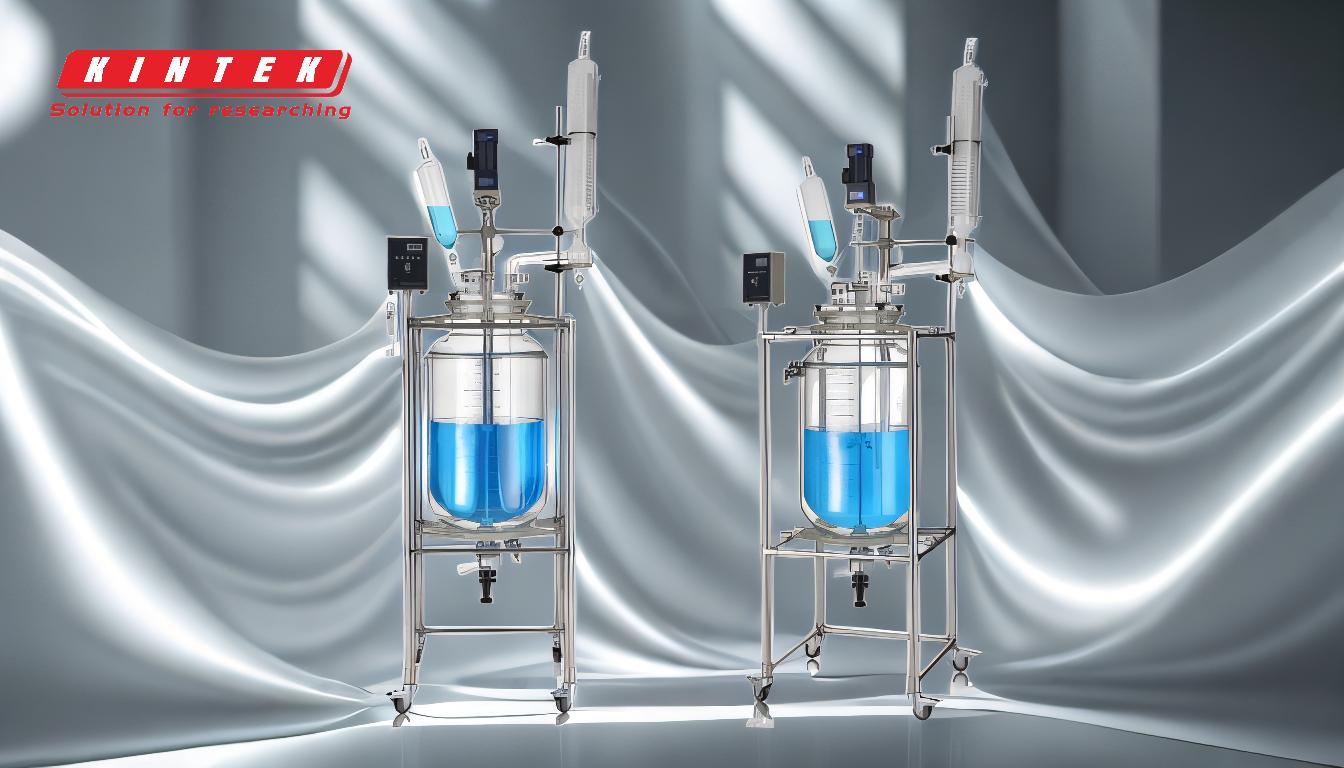
-
Non-Continuous Operation:
- Batch reactors operate in a closed system where reactants are added at the beginning, and no additional materials enter or exit during the reaction.
- This contrasts with continuous reactors, where reactants and products flow in and out simultaneously.
-
Reaction Initiation:
- All necessary components, including reactants, catalysts, and solvents, are loaded into the reactor at the start.
- The reactor is then sealed to prevent any leakage or contamination during the reaction.
-
Reaction Progression:
- The reaction proceeds over a fixed time period, often under controlled conditions such as heating or cooling.
- For example, a reaction might occur at 50°C for 5 hours, depending on the specific requirements of the process.
-
Control of Conditions:
- Temperature, pressure, and mixing are critical parameters that must be carefully controlled to ensure the reaction proceeds as intended.
- Batch reactors do not reach a steady state, so maintaining consistent conditions throughout the reaction is essential.
-
Product Removal:
- Once the reaction is complete, the products are removed from the reactor.
- This marks the end of the batch cycle, and the reactor can be cleaned and prepared for the next batch.
-
Applications:
- Batch reactors are commonly used in small-scale production, research and development, and processes involving biological materials such as enzyme production.
- They are also suitable for complex reactions that require precise control over reaction conditions.
-
Advantages:
- Simplicity in design and operation makes batch reactors ideal for learning and understanding reaction kinetics.
- They allow for flexibility in processing different reactions and materials in the same reactor.
- Precise control over reaction conditions can lead to high-quality products.
-
Limitations:
- Batch reactors are not suitable for large-scale continuous production due to their non-continuous nature.
- They require downtime between batches for cleaning and preparation, which can reduce overall efficiency.
By understanding these key points, one can appreciate the mode of operation of a batch reactor and its suitability for specific applications in chemical and biological processing.
Summary Table:
Aspect | Details |
---|---|
Operation Mode | Non-continuous; reactants added at start, no inputs/outputs during reaction |
Key Controls | Temperature, pressure, and mixing |
Applications | Small-scale production, R&D, biological materials, complex reactions |
Advantages | Precise control, simple design, flexibility in processing |
Limitations | Not suitable for large-scale production; downtime between batches |
Discover how batch reactors can optimize your chemical processes—contact our experts today!