DC sputtering is a widely used physical vapor deposition (PVD) technique for creating thin films on substrates. It operates by applying a DC voltage to a conductive target material in a low-pressure inert gas environment, typically argon. The process involves ionizing the gas to create a plasma, which accelerates ions toward the target. These ions collide with the target, ejecting atoms that deposit onto a nearby substrate, forming a thin film. DC sputtering is favored for its simplicity, cost-effectiveness, and high deposition rates, making it suitable for industries like semiconductors, optics, and jewelry. It is particularly effective for conductive materials such as metals.
Key Points Explained:
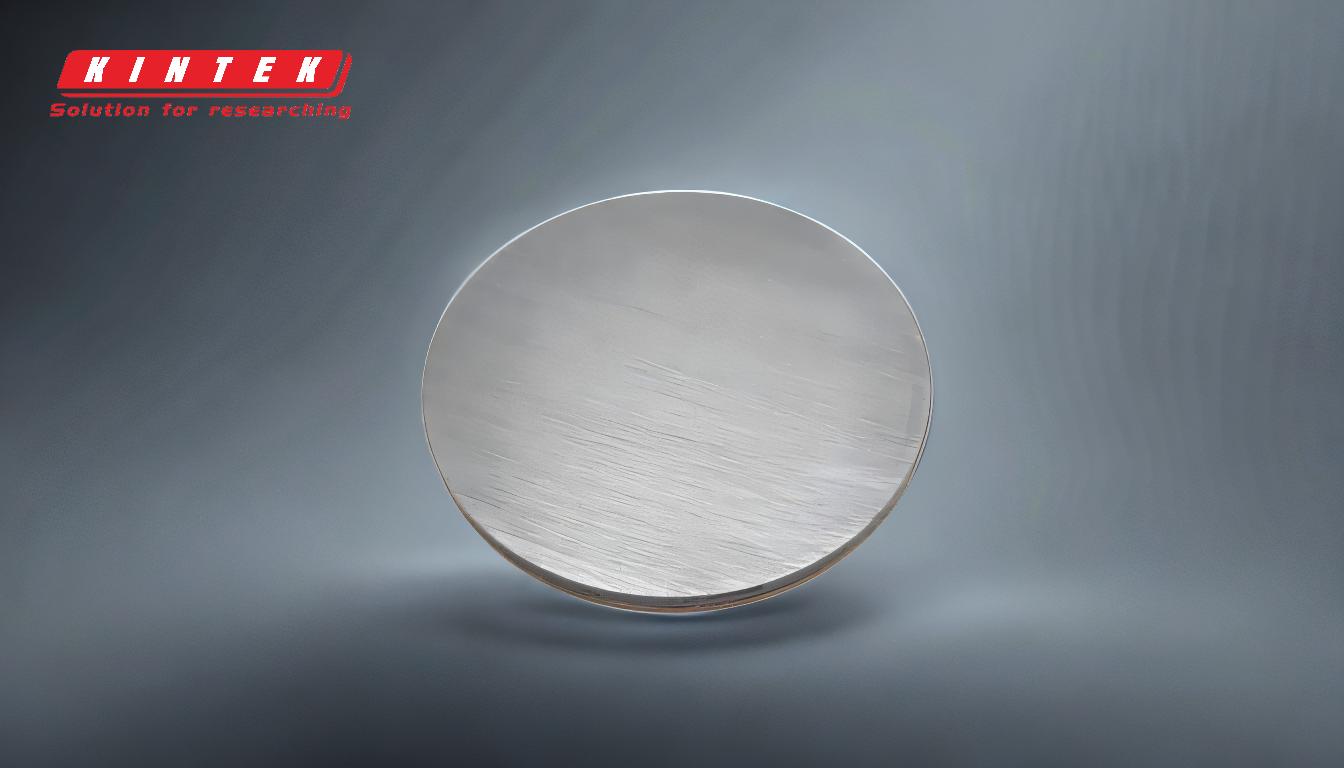
-
Basic Principle of DC Sputtering:
- DC sputtering is a PVD process where a conductive target material is bombarded with ionized gas particles (typically argon) in a vacuum chamber.
- A DC voltage is applied, creating a plasma that ionizes the gas atoms.
- These ions are accelerated toward the target, ejecting atoms from its surface, which then deposit onto a substrate to form a thin film.
-
Vacuum Environment:
- The process occurs in a vacuum chamber to prevent contamination from air or other gases.
- The vacuum ensures uniform deposition and allows precise control over the sputtering process.
-
Inert Gas and Plasma Formation:
- An inert gas, usually argon, is introduced into the chamber at low pressure (1–100 mTorr).
- The applied DC voltage ionizes the gas, creating a plasma composed of positively charged ions and free electrons.
-
Sputtering Mechanism:
- Positively charged argon ions are accelerated toward the negatively charged target.
- Upon collision, energy is transferred to the target atoms, causing them to be ejected (sputtered) from the surface.
- These ejected atoms travel through the chamber and deposit onto the substrate.
-
Deposition of Thin Film:
- The sputtered atoms condense on the substrate, forming a thin film.
- The process is suitable for heat-sensitive substrates, such as plastics, due to the low temperature of the sputtered particles.
-
Advantages of DC Sputtering:
- Simple and cost-effective compared to other PVD techniques.
- High deposition rates for conductive materials like pure metals (e.g., Fe, Cu, Ni).
- Suitable for large-scale production and large substrates.
-
Applications:
- Widely used in industries such as semiconductors, optical coatings, and jewelry.
- Ideal for depositing conductive and metallic thin films.
-
Limitations:
- Primarily effective for conductive target materials.
- Non-conductive materials require alternative techniques like RF sputtering.
By understanding these key points, one can appreciate the efficiency and versatility of DC sputtering in creating high-quality thin films for various industrial applications.
Summary Table:
Aspect | Details |
---|---|
Process | DC sputtering uses a conductive target in a vacuum chamber with inert gas. |
Key Principle | Ionized gas particles bombard the target, ejecting atoms onto a substrate. |
Environment | Low-pressure vacuum chamber with argon gas. |
Advantages | Cost-effective, high deposition rates, suitable for conductive materials. |
Applications | Semiconductors, optical coatings, jewelry. |
Limitations | Only effective for conductive materials; non-conductive require RF sputtering. |
Discover how DC sputtering can enhance your thin film processes—contact our experts today!