A fluidized bed reactor operates by passing a fluid (gas or liquid) through a solid granular material, typically a catalyst, supported by a porous distributor plate. At low fluid velocities, the solids remain stationary, forming a packed bed. As the fluid velocity increases, the solid particles become suspended, leading to fluidization. This process allows the solid particles to behave like a fluid, enabling efficient heat and mass transfer, uniform temperature distribution, and enhanced chemical reactions. The reactor is widely used in industries such as chemical processing, energy production, and waste treatment due to its high efficiency and scalability.
Key Points Explained:
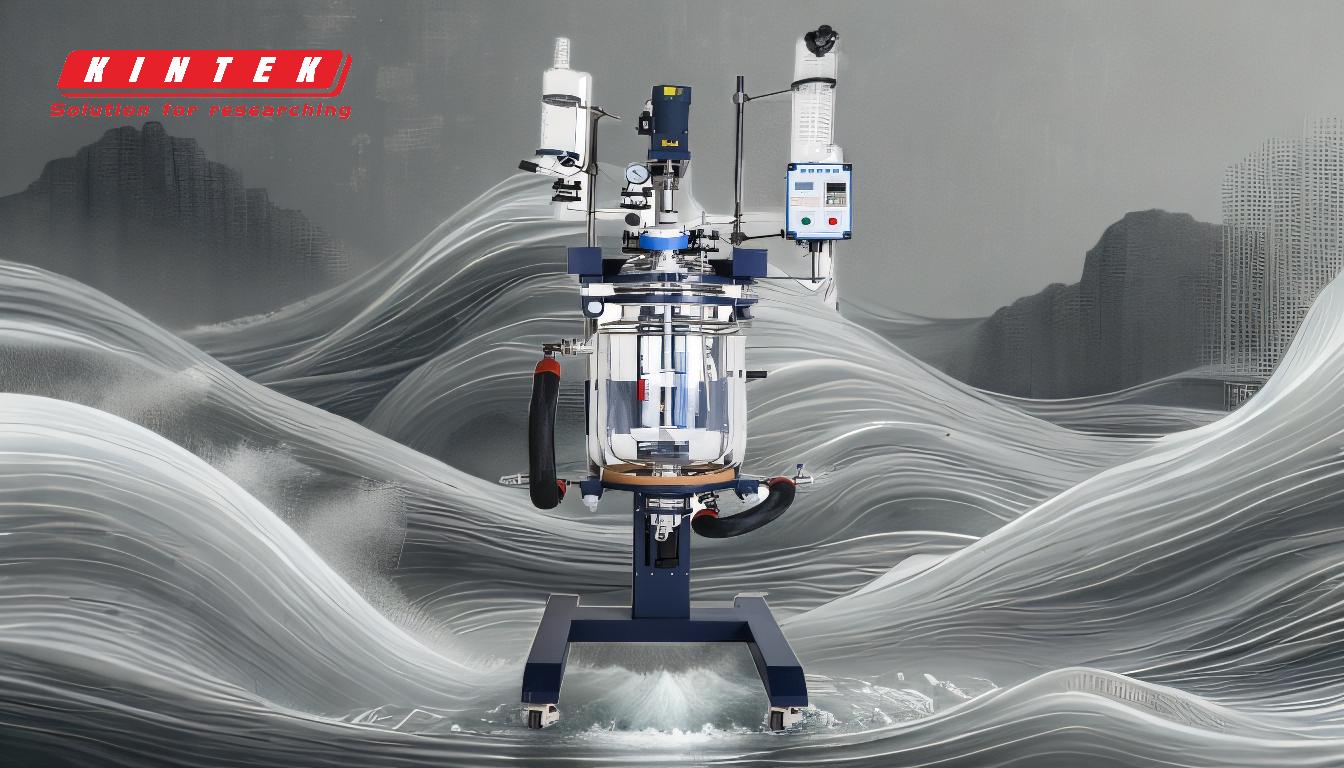
-
Basic Working Principle:
- A fluidized bed reactor involves passing a fluid (gas or liquid) through a solid granular material, such as a catalyst, supported by a porous distributor plate.
- At low fluid velocities, the solid particles remain stationary, forming a packed bed reactor.
- As the fluid velocity increases, the solid particles become suspended and behave like a fluid, a state known as fluidization.
-
Fluidization Process:
- Fluidization begins at the minimum fluidization velocity, where the upward force of the fluid balances the weight of the solid particles.
- Beyond this velocity, the solid particles expand and swirl, creating a fluidized bed.
- The fluidized state allows for efficient mixing, heat transfer, and mass transfer, making it ideal for chemical reactions and thermal processes.
-
Components of a Fluidized Bed Reactor:
- Distributor Plate: A porous plate at the bottom of the reactor that evenly distributes the fluid flow to ensure uniform fluidization.
- Bed Material: Typically consists of solid granular materials like sand or catalyst particles, which facilitate heat transfer and chemical reactions.
- Fluidizing Medium: A gas (e.g., nitrogen) or liquid that flows through the bed material to achieve fluidization and maintain an inert atmosphere if necessary.
-
Flow Regimes:
- The behavior of the fluidized bed depends on the fluid velocity and the properties of the solid phase.
- At low velocities, the bed remains packed.
- At moderate velocities, the bed becomes fluidized, with particles moving freely.
- At very high velocities, the bed may transition to a bubbling or turbulent regime, where gas bubbles form and break, enhancing mixing.
-
Applications and Advantages:
- Chemical Processing: Used for catalytic reactions, such as cracking and reforming, due to the high surface area of the fluidized particles.
- Energy Production: Employed in coal gasification and biomass combustion for efficient heat transfer and reaction control.
- Waste Treatment: Utilized in pyrolysis and gasification of waste materials to recover energy and reduce emissions.
- Advantages: High heat and mass transfer rates, uniform temperature distribution, scalability, and adaptability to various processes.
-
Operational Considerations:
- Heat Transfer: The bed material efficiently transfers heat to the substrate, ensuring uniform temperature distribution.
- Inert Atmosphere: Gases like nitrogen are often used to prevent unwanted chemical reactions, such as oxidation.
- Particle Size and Density: The size and density of the solid particles influence the fluidization behavior and must be carefully selected for optimal performance.
-
Challenges:
- Erosion and Abrasion: The constant movement of particles can cause wear and tear on reactor components.
- Particle Entrainment: Fine particles may be carried out of the reactor by the fluid, requiring separation and recycling.
- Pressure Drop: Maintaining fluidization requires careful control of fluid velocity to avoid excessive pressure drops.
By understanding these principles, a fluidized bed reactor can be effectively designed and operated for a wide range of industrial applications, offering significant advantages in terms of efficiency and process control.
Summary Table:
Aspect | Details |
---|---|
Working Principle | Fluid passes through solid granular material, causing fluidization. |
Fluidization Process | Begins at minimum fluidization velocity; particles behave like a fluid. |
Key Components | Distributor plate, bed material, fluidizing medium. |
Applications | Chemical processing, energy production, waste treatment. |
Advantages | High heat/mass transfer, uniform temperature, scalability. |
Challenges | Erosion, particle entrainment, pressure drop. |
Discover how a fluidized bed reactor can optimize your processes—contact our experts today!