The process of double extrusion, also known as dual durometer extrusion, involves combining two materials with different properties into a single part through a co-extrusion process. This method allows manufacturers to create products that benefit from the unique characteristics of both materials, such as combining a soft, flexible material with a hard, durable one. The process is achieved by extruding both materials simultaneously through the same die, ensuring they fuse together seamlessly. This technique is particularly useful in applications where a product requires both flexibility and durability, such as in seals, gaskets, or medical devices.
Key Points Explained:
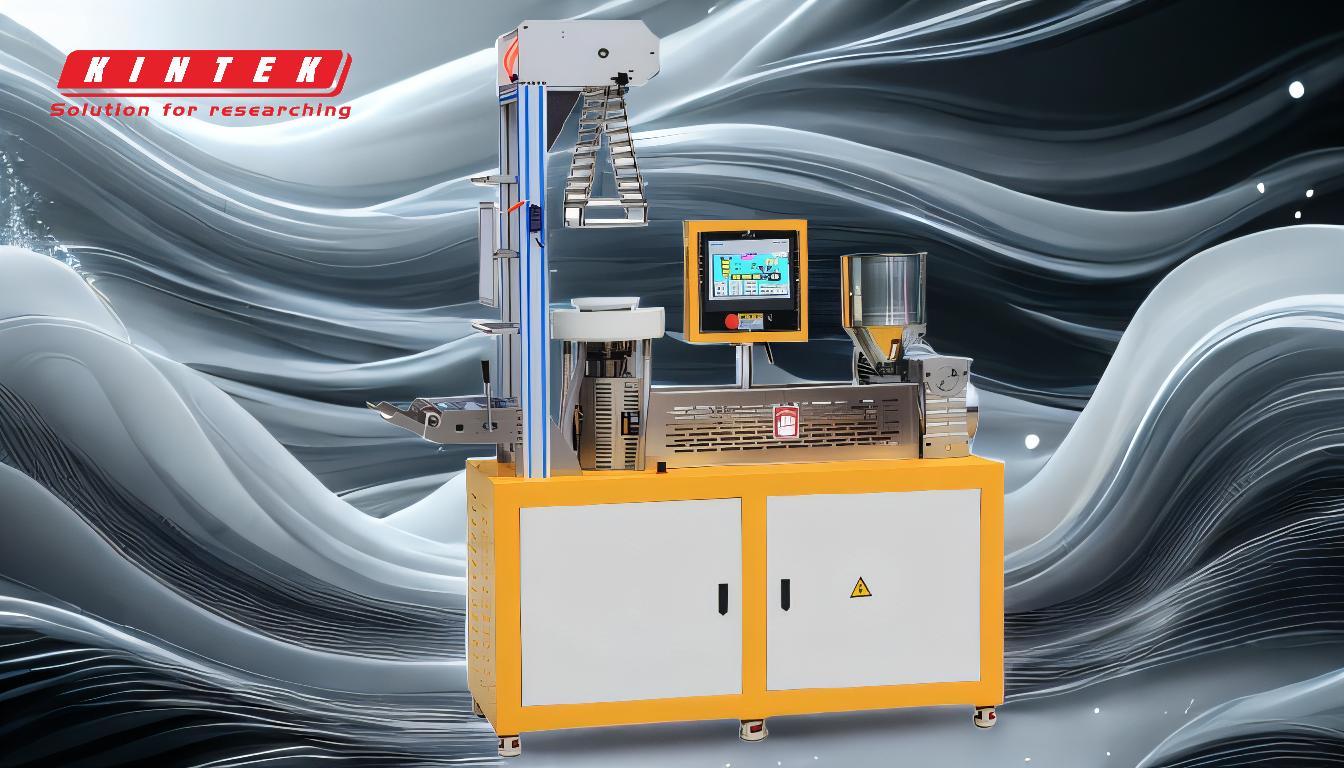
-
Definition of Double Extrusion:
- Double extrusion, or dual durometer extrusion, is a manufacturing process where two different materials are extruded simultaneously through the same die to create a single, unified part.
- This process allows for the combination of materials with different properties, such as hardness and flexibility, into one product.
-
Materials Used:
- The materials used in double extrusion are typically chosen based on the desired properties of the final product. For example, one material might be soft and flexible, while the other is hard and durable.
- Common materials include thermoplastic elastomers (TPE), silicon windows , and various types of rubber calender or plastic.
-
The Co-Extrusion Process:
- In the co-extrusion process, both materials are fed into separate extruders, which then push the materials through a shared die.
- The die is designed to ensure that the two materials fuse together as they exit, creating a single, cohesive part.
- The process requires precise control over temperature, pressure, and material flow to ensure proper bonding and uniformity.
-
Advantages of Double Extrusion:
- Combination of Properties: Double extrusion allows manufacturers to combine the benefits of two different materials, such as flexibility and durability, in a single product.
- Cost Efficiency: By combining materials, manufacturers can reduce the need for additional components or assembly steps, potentially lowering production costs.
- Enhanced Performance: Products made through double extrusion can offer improved performance characteristics, such as better sealing, increased comfort, or greater resistance to wear and tear.
-
Applications of Double Extrusion:
- Seals and Gaskets: Double extrusion is commonly used in the production of seals and gaskets, where a combination of soft and hard materials can provide both a tight seal and durability.
- Medical Devices: In the medical industry, double extrusion is used to create devices that require both flexibility and strength, such as catheters or tubing.
- Automotive Components: The automotive industry utilizes double extrusion for parts like weather stripping, where a soft material provides a seal while a harder material offers structural support.
-
Challenges and Considerations:
- Material Compatibility: Ensuring that the two materials bond properly is crucial. Incompatible materials may not adhere well, leading to product failure.
- Process Control: The co-extrusion process requires precise control over various parameters, such as temperature and extrusion speed, to achieve consistent results.
- Tooling Design: The design of the die is critical in ensuring that the materials fuse correctly and that the final product meets the desired specifications.
-
Future Trends:
- Advanced Materials: As new materials are developed, the possibilities for double extrusion expand, allowing for even more specialized and high-performance products.
- Automation and Precision: Advances in extrusion technology are leading to greater automation and precision in the co-extrusion process, improving consistency and reducing waste.
- Sustainability: There is a growing focus on using recyclable or biodegradable materials in double extrusion processes, aligning with broader industry trends toward sustainability.
In summary, double extrusion is a versatile and efficient manufacturing process that allows for the creation of products with combined material properties. By understanding the key aspects of this process, manufacturers can leverage it to produce innovative and high-performance products across various industries.
Summary Table:
Aspect | Details |
---|---|
Definition | Combines two materials (e.g., soft + hard) into a single part via co-extrusion. |
Materials Used | Thermoplastic elastomers (TPE), silicon windows , rubber calender , and plastic. |
Process | Materials extruded simultaneously through a shared die for seamless fusion. |
Advantages | Combines properties, cost efficiency, enhanced performance. |
Applications | Seals, gaskets, medical devices, automotive components. |
Challenges | Material compatibility, process control, tooling design. |
Future Trends | Advanced materials, automation, sustainability. |
Ready to explore how double extrusion can enhance your product designs? Contact us today to learn more!