The process of evaporation heating involves the transfer of thermal energy to a liquid, which increases the kinetic energy of its molecules. This energy enables more molecules to overcome intermolecular forces and transition from the liquid phase to the gaseous phase. Heat is transferred from a heat source to the liquid, often through the container walls, causing the outer layers of the liquid to warm first. Convection currents then distribute the heat, equalizing temperatures throughout the liquid. Techniques such as stirring or rotary evaporation can enhance heat transfer, ensuring efficient evaporation. The maximum vapor production occurs when the liquid reaches its boiling point.
Key Points Explained:
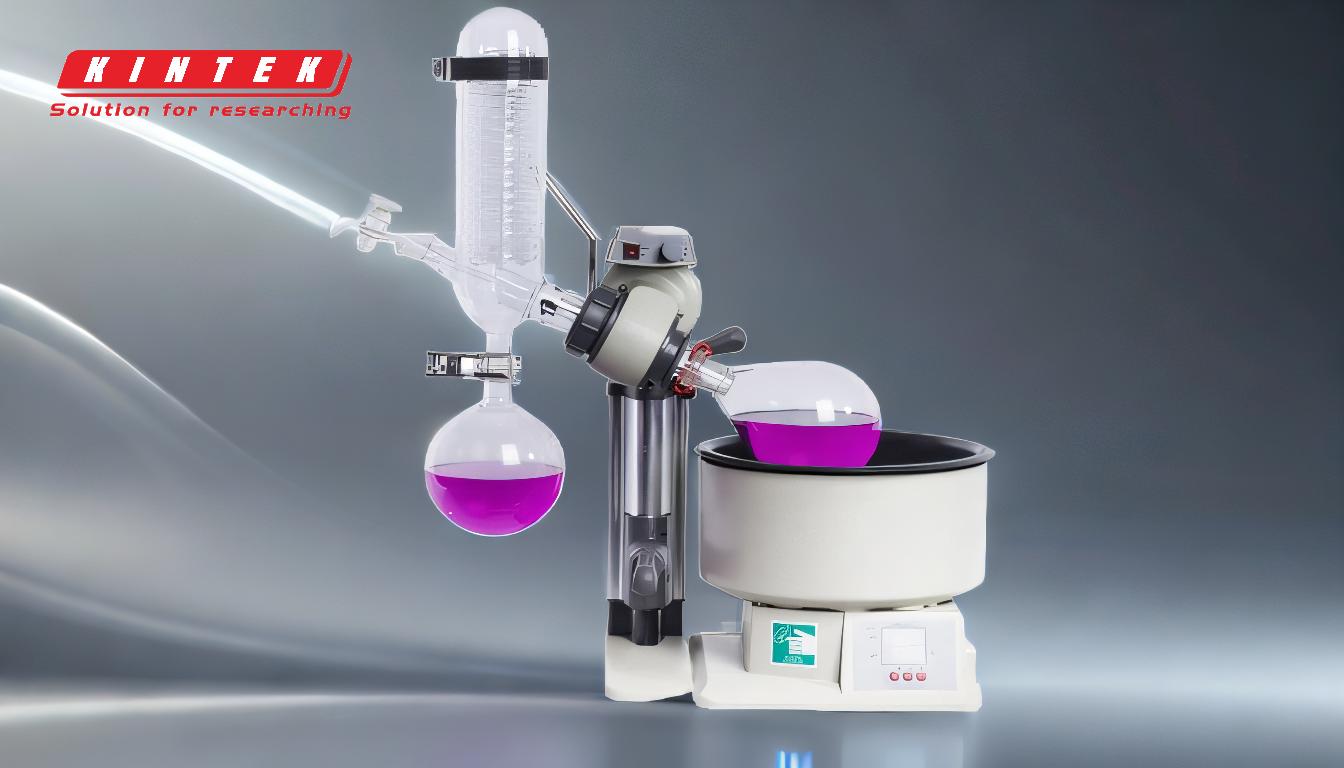
-
Energy Transfer to Liquid Molecules:
- Heat provides energy to the molecules in a liquid, increasing their kinetic energy.
- This energy makes the molecules more agile and increases the frequency of collisions.
- As a result, more molecules gain the necessary energy to transition from the liquid phase to the gaseous phase, accelerating the rate of evaporation.
-
Heat Transfer Mechanism:
- Heat is transferred from the heat source to the liquid, primarily through the walls of the container.
- The outer layers of the liquid warm up first, while the top layers remain cooler.
- Convection currents form as the warm layers rise and the cooler layers take their place, gradually equalizing the temperature throughout the liquid.
-
Role of Nucleate Boiling:
- Nucleate boiling is a process where bubbles form at nucleation sites on the heated surface, improving heat transfer.
- This phenomenon enhances the efficiency of evaporation by ensuring that heat is distributed more evenly throughout the liquid.
-
Enhancing Heat Transfer:
- Techniques such as stirring or using rotary evaporation technology can further improve heat transfer.
- These methods keep the liquid in motion, ensuring that heat is distributed more uniformly and that the evaporation process occurs more quickly and efficiently.
-
Maximum Vapor Production:
- The maximum amount of vapor is produced when the liquid reaches its boiling temperature.
- At this point, the energy provided by the heat source is sufficient to allow a large number of molecules to transition to the gaseous phase simultaneously.
-
Overcoming Intermolecular Forces:
- Evaporation occurs when the molecules of the liquid achieve sufficient energy to overcome the binding forces that hold them in the liquid phase.
- This energy allows the molecules to escape into the gas phase, completing the process of evaporation.
By understanding these key points, one can appreciate the intricate process of evaporation heating and the factors that influence its efficiency. Techniques to enhance heat transfer, such as stirring or rotary evaporation, are crucial for optimizing the evaporation process in various applications.
Summary Table:
Key Aspect | Explanation |
---|---|
Energy Transfer | Heat increases kinetic energy, enabling molecules to transition to the gas phase. |
Heat Transfer Mechanism | Heat flows through container walls, creating convection currents for even heating. |
Nucleate Boiling | Bubbles form at nucleation sites, enhancing heat distribution and evaporation. |
Enhancing Heat Transfer | Stirring or rotary evaporation ensures uniform heat distribution for faster evaporation. |
Maximum Vapor Production | Occurs at boiling point, where molecules transition to gas phase simultaneously. |
Overcoming Intermolecular Forces | Molecules gain energy to escape liquid phase, completing evaporation. |
Optimize your evaporation process with expert guidance—contact us today!