Reactive sputtering is a specialized thin-film deposition technique where a target material is sputtered in the presence of a reactive gas, such as oxygen or nitrogen. This process enables the formation of compound films, such as oxides or nitrides, on a substrate. The reactive gas chemically interacts with the sputtered target atoms, forming new compounds that are then deposited as thin films. The process requires precise control of parameters like gas flow rates, partial pressures, and plasma conditions to achieve the desired film stoichiometry and properties. Reactive sputtering is widely used in applications requiring tailored functional properties, such as optical coatings, barrier layers, and semiconductor devices.
Key Points Explained:
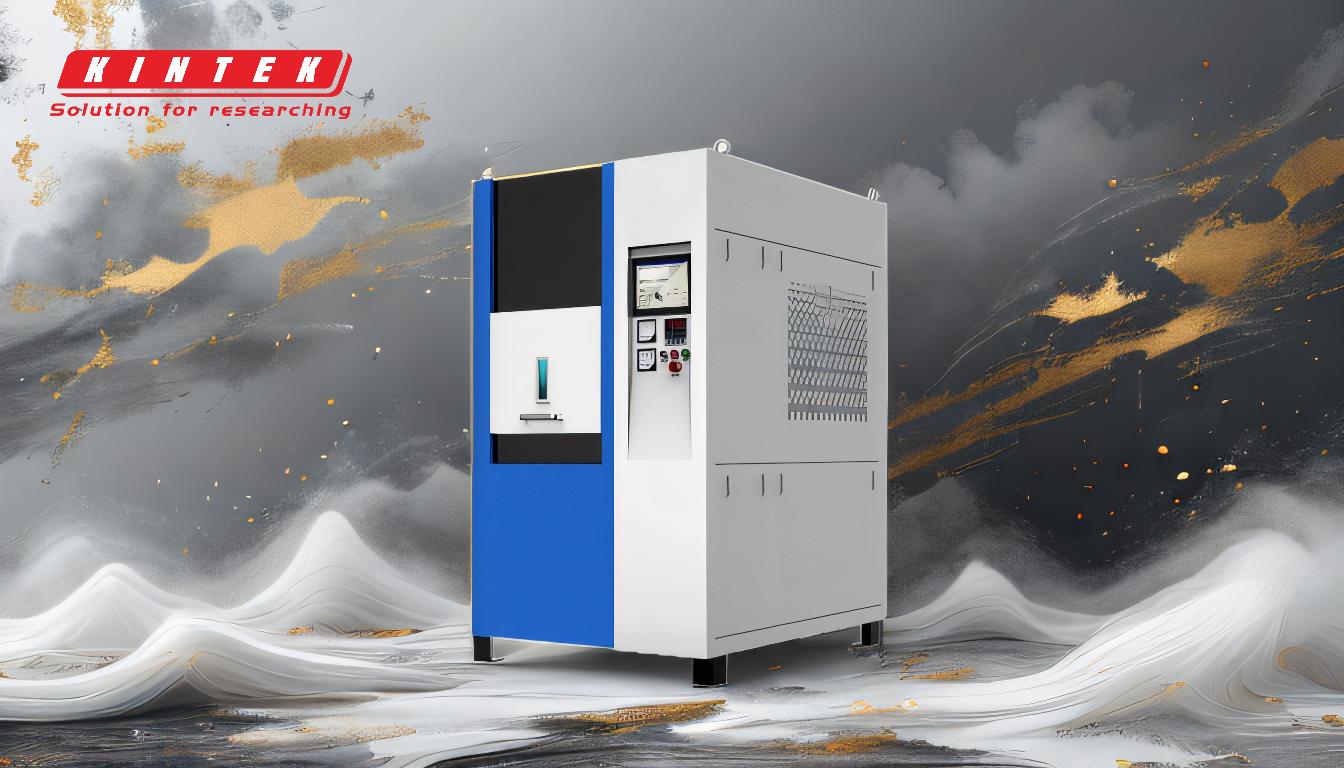
-
Fundamental Process of Reactive Sputtering:
- Reactive sputtering is a variation of the plasma sputtering process where a reactive gas (e.g., oxygen, nitrogen) is introduced into the vacuum chamber alongside an inert gas (e.g., argon).
- The target material is bombarded by ions from the plasma, causing atoms to be ejected from the target surface.
- These ejected atoms react chemically with the reactive gas in the chamber, forming compounds such as oxides or nitrides.
- The resulting compound is then deposited as a thin film on the substrate.
-
Role of Reactive Gases:
- Reactive gases, such as oxygen or nitrogen, are critical in forming compound films. For example:
- Sputtering silicon with oxygen produces silicon oxide (SiO₂).
- Sputtering titanium with nitrogen produces titanium nitride (TiN).
- The reactive gas becomes ionized in the plasma environment, enabling it to react with the sputtered target atoms.
- Reactive gases, such as oxygen or nitrogen, are critical in forming compound films. For example:
-
Control of Film Stoichiometry:
- The stoichiometry (chemical composition) of the deposited film is controlled by adjusting the relative pressures of the inert and reactive gases.
- Precise control of gas flow rates and partial pressures ensures the formation of films with the desired composition and functional properties, such as stress, refractive index, or electrical conductivity.
-
Hysteresis-Like Behavior:
- The introduction of a reactive gas complicates the process, often leading to hysteresis-like behavior. This means that the process parameters (e.g., gas flow, pressure) do not have a linear relationship with the film properties.
- Careful monitoring and control are required to avoid instability and ensure consistent film quality.
-
Berg Model for Process Optimization:
- The Berg Model is a theoretical framework used to estimate the impact of the reactive gas on target erosion and film deposition rates.
- It helps predict how changes in reactive gas flow or pressure will affect the film composition and deposition rate, enabling optimization of the process.
-
Applications of Reactive Sputtering:
- Reactive sputtering is widely used to produce thin films with tailored properties for various applications:
- Optical coatings: Films with specific refractive indices for lenses and mirrors.
- Barrier layers: Thin films like titanium nitride (TiN) used in semiconductor devices to prevent diffusion.
- Functional coatings: Films with specific mechanical, electrical, or optical properties for sensors, displays, and solar cells.
- Reactive sputtering is widely used to produce thin films with tailored properties for various applications:
-
Process Variants:
- Reactive sputtering can be performed using different power sources:
- DC reactive sputtering: Suitable for conductive target materials.
- HF (high-frequency) reactive sputtering: Used for insulating or semi-conducting target materials.
- The choice of power source depends on the target material and the desired film properties.
- Reactive sputtering can be performed using different power sources:
-
Challenges and Considerations:
- Target poisoning: Excessive reaction of the target surface with the reactive gas can reduce sputtering efficiency. This is mitigated by controlling gas flow and plasma conditions.
- Process stability: Maintaining consistent film properties requires careful management of process parameters to avoid hysteresis effects.
- Equipment requirements: Reactive sputtering systems must be designed to handle reactive gases safely and maintain precise control over gas flow and pressure.
-
Advantages of Reactive Sputtering:
- Enables the deposition of compound films with precise control over composition and properties.
- Versatile process suitable for a wide range of materials and applications.
- Can produce high-quality, uniform films with excellent adhesion to the substrate.
-
Practical Example:
- Silicon Oxide Films: Sputtering silicon in the presence of oxygen produces silicon oxide (SiO₂) films, which are widely used in optical and electronic applications due to their excellent insulating properties and transparency.
By understanding and controlling the key parameters of reactive sputtering, manufacturers can produce thin films with tailored properties for a wide range of advanced applications.
Summary Table:
Aspect | Details |
---|---|
Process | Sputtering target material in the presence of reactive gases (e.g., O₂, N₂) |
Key Applications | Optical coatings, barrier layers, semiconductor devices |
Control Parameters | Gas flow rates, partial pressures, plasma conditions |
Advantages | Precise film composition, high-quality films, versatile applications |
Challenges | Target poisoning, process stability, equipment requirements |
Discover how reactive sputtering can enhance your thin-film processes—contact our experts today!