The temperature of regeneration for solid desiccant systems, such as molecular sieves, typically ranges between 65°C and 105°C. Research indicates that the highest coefficient of performance (COP) is often achieved at the lower end of this range, around 65°C. This temperature range is considered optimal for balancing energy efficiency and effective moisture removal in desiccant systems. Below, we will explore the key factors influencing regeneration temperature and its implications for system performance.
Key Points Explained:
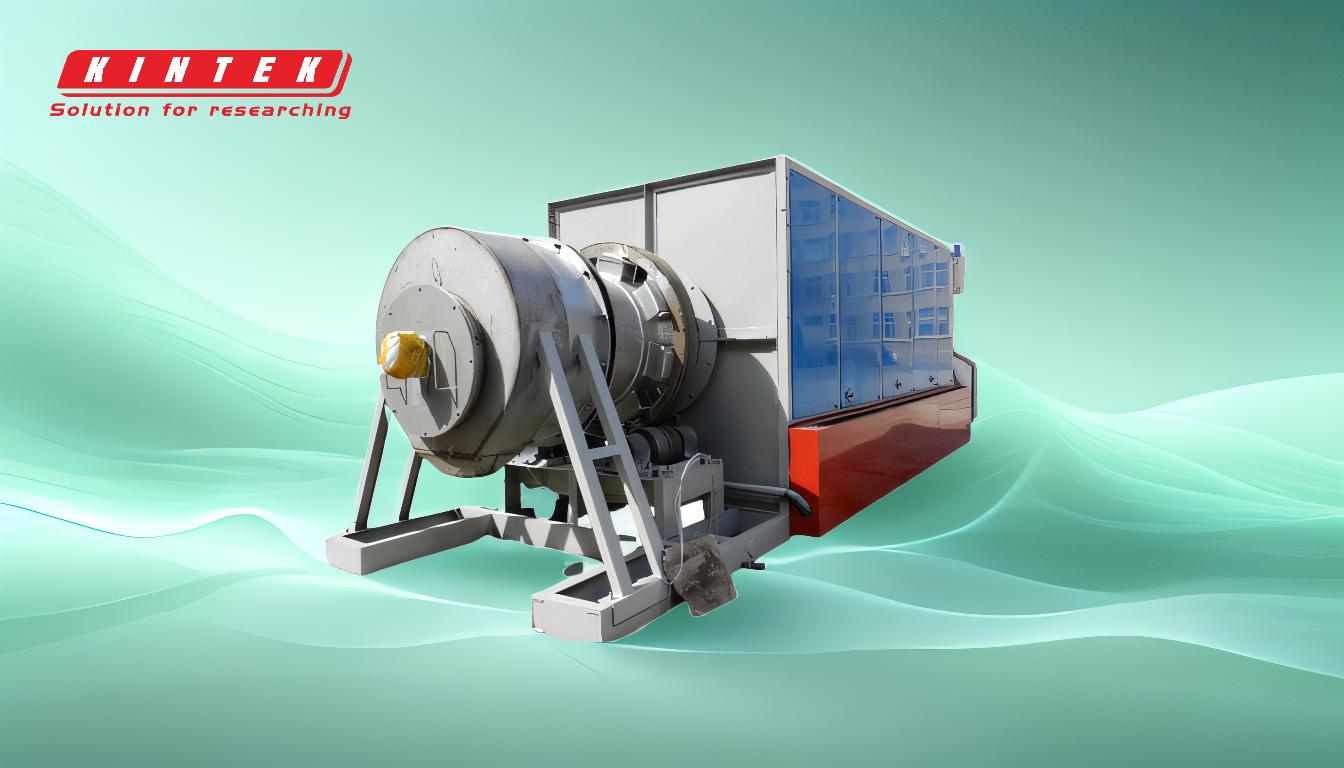
-
Optimal Regeneration Temperature Range:
- The regeneration temperature for solid desiccant systems, such as molecular sieves, typically falls between 65°C and 105°C.
- Research by Jurinak et al. (1984) found that the highest COP was achieved at 65°C, suggesting that lower temperatures within this range can be more energy-efficient.
- Shen and Worek (1996) further supported this, indicating that the optimal regeneration temperature for molecular sieves lies between 65°C and 85°C.
-
Factors Influencing Regeneration Temperature:
- Desiccant Material: The type of desiccant (e.g., molecular sieves, silica gel) influences the required regeneration temperature. Molecular sieves, for instance, perform optimally at lower temperatures compared to some other desiccants.
- Energy Efficiency: Lower regeneration temperatures, such as 65°C, are often preferred because they reduce energy consumption while still effectively removing moisture.
- System Design: The design of the desiccant system, including airflow and heating mechanisms, can impact the ideal regeneration temperature.
-
Implications of Regeneration Temperature:
- Energy Consumption: Higher regeneration temperatures (e.g., 105°C) may increase energy usage, reducing the overall efficiency of the system.
- Desiccant Lifespan: Excessive temperatures can degrade the desiccant material over time, shortening its lifespan and increasing maintenance costs.
- Moisture Removal Efficiency: While higher temperatures can enhance moisture removal, the trade-off with energy efficiency must be carefully considered.
-
Practical Considerations for Purchasers:
- System Compatibility: Ensure that the chosen regeneration temperature aligns with the specifications of the desiccant material and system design.
- Operational Costs: Opt for systems that operate at lower regeneration temperatures to minimize energy consumption and operational costs.
- Long-Term Performance: Evaluate the impact of regeneration temperature on the durability and maintenance requirements of the desiccant material.
By understanding these key points, purchasers can make informed decisions about the regeneration temperature that best suits their needs, balancing performance, energy efficiency, and cost-effectiveness.
Summary Table:
Key Factor | Details |
---|---|
Optimal Temperature Range | 65°C–105°C, with highest COP at 65°C. |
Desiccant Material | Molecular sieves perform best at lower temperatures. |
Energy Efficiency | Lower temperatures (e.g., 65°C) reduce energy consumption. |
System Design | Airflow and heating mechanisms influence ideal temperature. |
Implications | Higher temperatures increase energy use and may degrade desiccant lifespan. |
Practical Considerations | Align temperature with system specs to minimize costs and maximize durability. |
Ready to optimize your desiccant system? Contact our experts today for tailored solutions!