Thin film evaporators are specialized devices used for thermal separation processes, particularly in industries requiring precise and efficient distillation or evaporation of volatile components. The theory behind thin film evaporators revolves around creating a thin, highly turbulent liquid film on a heated surface, which facilitates rapid heat transfer and evaporation of volatile components. This process minimizes thermal degradation of heat-sensitive materials due to the short residence time and controlled temperature conditions. The evaporated components are then condensed and collected, while the non-volatile residue is separated. This method is widely used in industries such as pharmaceuticals, chemicals, and food processing for its efficiency and ability to handle delicate materials.
Key Points Explained:
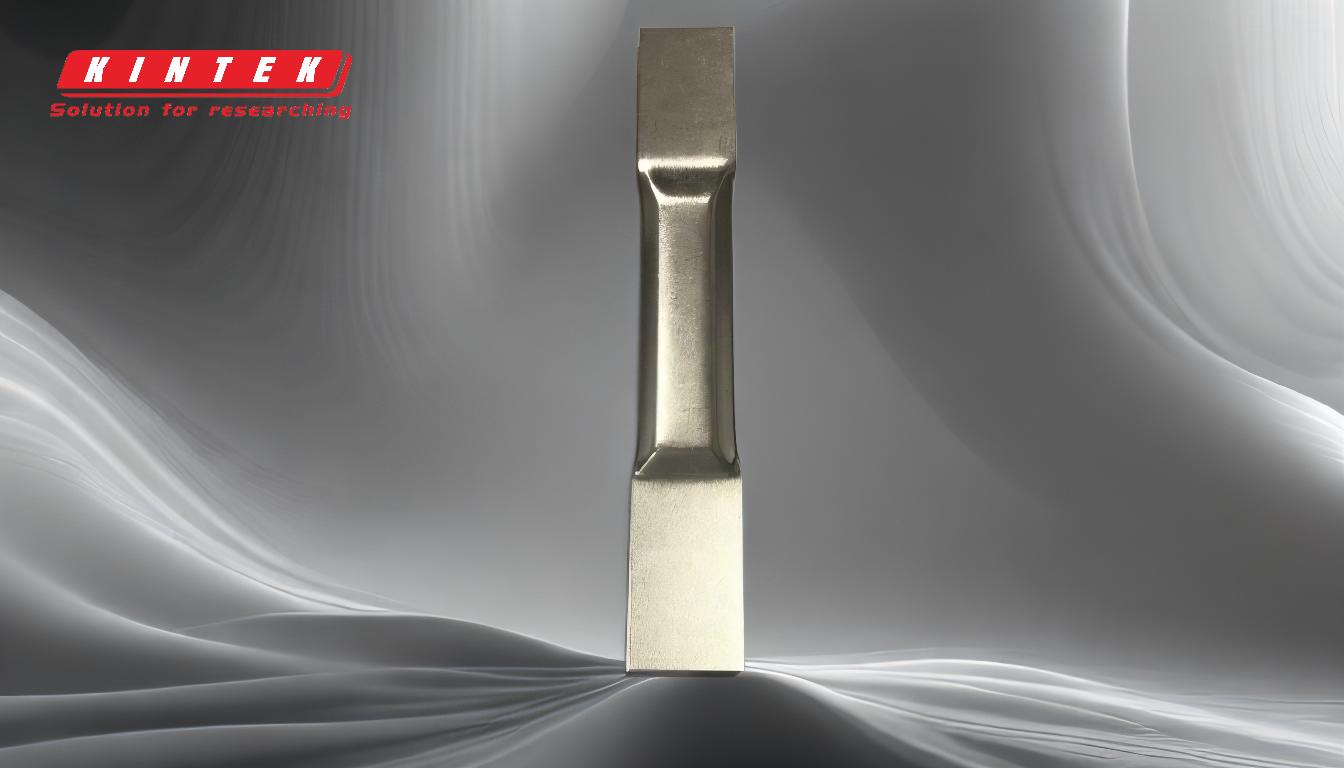
-
Working Principle of Thin Film Evaporation:
- Thin film evaporation relies on the creation of a thin, turbulent liquid film on a heated surface.
- Heat is transferred from the heated surface to the liquid film, causing the volatile components to evaporate.
- The process is highly efficient due to the large surface area-to-volume ratio of the thin film, which enhances heat transfer and minimizes thermal stress on the material.
-
Mechanically Generated Thin Film:
- In wiped film evaporators, mechanical agitation (e.g., rotating wipers or blades) is used to generate and maintain the thin liquid film.
- This agitation ensures uniform distribution of the liquid on the heated surface and enhances turbulence, which improves heat transfer and evaporation rates.
- The mechanical action also prevents fouling or buildup of residue on the heated surface.
-
Thermal Separation Process:
- Thin film evaporation is a thermal separation technique where heat is applied to evaporate volatile components from a mixture.
- The process is designed to minimize the exposure of heat-sensitive materials to high temperatures, reducing the risk of degradation.
- The evaporated components are condensed and collected separately, while the non-volatile residue is removed from the system.
-
Vacuum Operation:
- Thin film evaporators often operate under vacuum conditions to lower the boiling point of the volatile components.
- This reduces the required evaporation temperature, which is particularly beneficial for heat-sensitive materials.
- Vacuum operation also prevents contamination and ensures uniform deposition or condensation of the evaporated components.
-
Applications in Distillation and Evaporation:
- Thin film evaporators are widely used in distillation processes, such as short-path distillation, where high purity and minimal thermal degradation are required.
- They are also used in evaporation processes for concentrating solutions, recovering solvents, and separating mixtures with varying boiling points.
-
Advantages of Thin Film Evaporators:
- High Efficiency: The thin film and turbulent flow enhance heat transfer and evaporation rates.
- Minimal Thermal Degradation: Short residence times and controlled temperatures protect heat-sensitive materials.
- Versatility: Suitable for a wide range of applications, including distillation, concentration, and solvent recovery.
- Compact Design: Thin film evaporators are often more compact than traditional evaporators, making them ideal for laboratory and industrial settings.
-
Comparison to Other Evaporation Techniques:
- Thin film evaporation is similar to short-path distillation but differs in the way the liquid film is generated and maintained.
- Unlike batch distillation, thin film evaporation operates continuously, allowing for higher throughput and efficiency.
- The process is more controlled and efficient than conventional evaporation methods, which often involve longer residence times and higher temperatures.
By understanding these key points, equipment and consumable purchasers can better evaluate the suitability of thin film evaporators for their specific applications, ensuring optimal performance and cost-effectiveness.
Summary Table:
Key Aspect | Details |
---|---|
Working Principle | Thin, turbulent liquid film on a heated surface for rapid heat transfer. |
Mechanical Agitation | Rotating wipers/blades maintain film uniformity and prevent residue buildup. |
Thermal Separation | Controlled heat minimizes degradation of heat-sensitive materials. |
Vacuum Operation | Lowers boiling point, reduces temperature, and prevents contamination. |
Applications | Distillation, solvent recovery, and concentration in various industries. |
Advantages | High efficiency, minimal degradation, versatility, and compact design. |
Comparison to Other Methods | More controlled and efficient than batch or conventional evaporation. |
Discover how thin film evaporators can optimize your processes—contact us today for expert advice!