The thermodynamic driving force for sintering is primarily the reduction of surface energy, which occurs as the surface area of particles decreases and solid-solid interfaces replace solid-vapor interfaces. This process is driven by the system's tendency to achieve a lower energy state. The curvature gradients, surface tension, and interfacial energies play critical roles in facilitating atomic motion through thermally activated diffusion mechanisms. Factors such as temperature, particle size, and composition further influence the kinetics and outcomes of sintering. Ultimately, sintering leads to densification and microstructural changes, resulting in a more stable and lower-energy material state.
Key Points Explained:
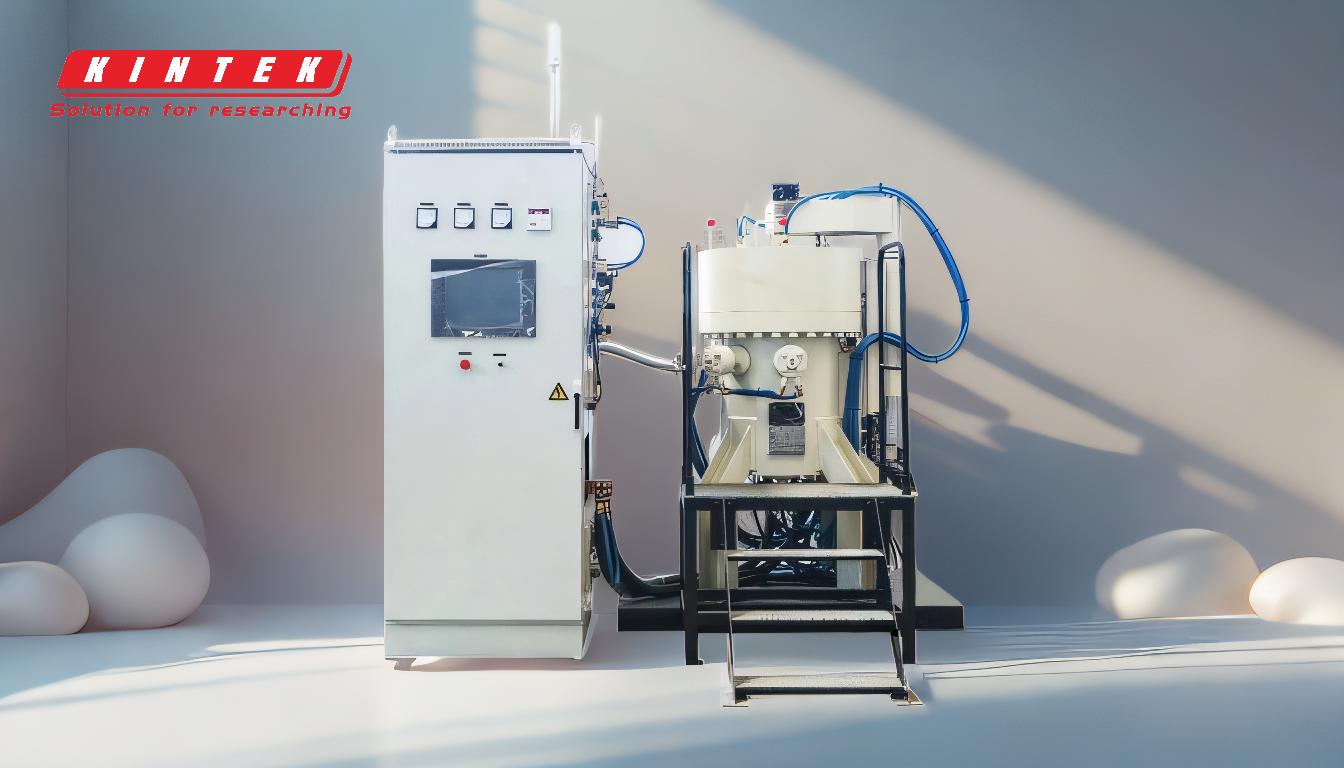
-
Reduction of Surface Energy:
- The primary thermodynamic driving force for sintering is the reduction of surface energy. Particles in a powder system have high surface energy due to their large surface area-to-volume ratio.
- As sintering progresses, the solid-vapor interfaces are replaced by solid-solid interfaces, which have lower energy. This reduction in surface energy drives the system toward a more stable state.
-
Curvature Gradients and Surface Tension:
- Curvature gradients between particles create differences in chemical potential, which drive atomic diffusion from areas of high curvature (high energy) to areas of low curvature (low energy).
- Surface tension acts as a driving force for the movement of metal atoms, facilitating the redistribution of material and the formation of necks between particles.
-
Interfacial Energies:
- The replacement of high-energy solid-vapor interfaces with lower-energy solid-solid interfaces reduces the total free energy of the system.
- This energy reduction is a key factor in the densification and microstructural evolution during sintering.
-
Thermally Activated Diffusion Mechanisms:
- Sintering is controlled by solid-state diffusion mechanisms, which are thermally activated. Higher temperatures increase atomic mobility, accelerating the sintering process.
- Tools like Linseis push rod dilatometers are used to quantify these mechanisms and model sintering behavior.
-
Factors Influencing Sintering:
- Temperature: Determines the kinetics of sintering and the final material properties. Higher temperatures generally enhance diffusion and densification.
- Heating Rate: Affects the rate of densification and the development of the microstructure.
- Pressure: Applied pressure can enhance particle rearrangement and eliminate porosity, leading to faster densification.
- Particle Size: Smaller particles have higher surface energy and sinter more readily due to their increased surface area.
- Composition: Homogeneous compositions promote better densification and more uniform microstructures.
-
Microstructural Changes:
- During sintering, the microstructure evolves as particles bond and pores shrink or close. This leads to increased density and improved mechanical properties.
- The final microstructure is influenced by the sintering conditions and the initial characteristics of the powder.
By understanding these key points, one can better control the sintering process to achieve desired material properties and optimize the performance of sintered components.
Summary Table:
Key Aspect | Description |
---|---|
Reduction of Surface Energy | Primary driving force; replaces high-energy solid-vapor interfaces with solid-solid interfaces. |
Curvature Gradients | Drives atomic diffusion from high-energy to low-energy areas. |
Interfacial Energies | Lower-energy solid-solid interfaces reduce total free energy. |
Diffusion Mechanisms | Thermally activated; higher temperatures enhance atomic mobility. |
Influencing Factors | Temperature, heating rate, pressure, particle size, and composition. |
Microstructural Changes | Leads to densification, pore shrinkage, and improved mechanical properties. |
Optimize your sintering process with expert insights—contact us today!