The vacuum evaporation method is a Physical Vapor Deposition (PVD) technique used to deposit thin films of material onto a substrate. In this process, the target material is heated to its evaporation point in a vacuum environment, causing it to transition into a gaseous phase. The vaporized molecules then travel through the vacuum and condense on the substrate, forming a thin, uniform film. This method is widely used in industries such as electronics, optics, and coatings due to its ability to produce high-purity and precise thin films. A common variation of this method is thermal evaporation, where the material is heated using resistive heating elements like boats, coils, or baskets.
Key Points Explained:
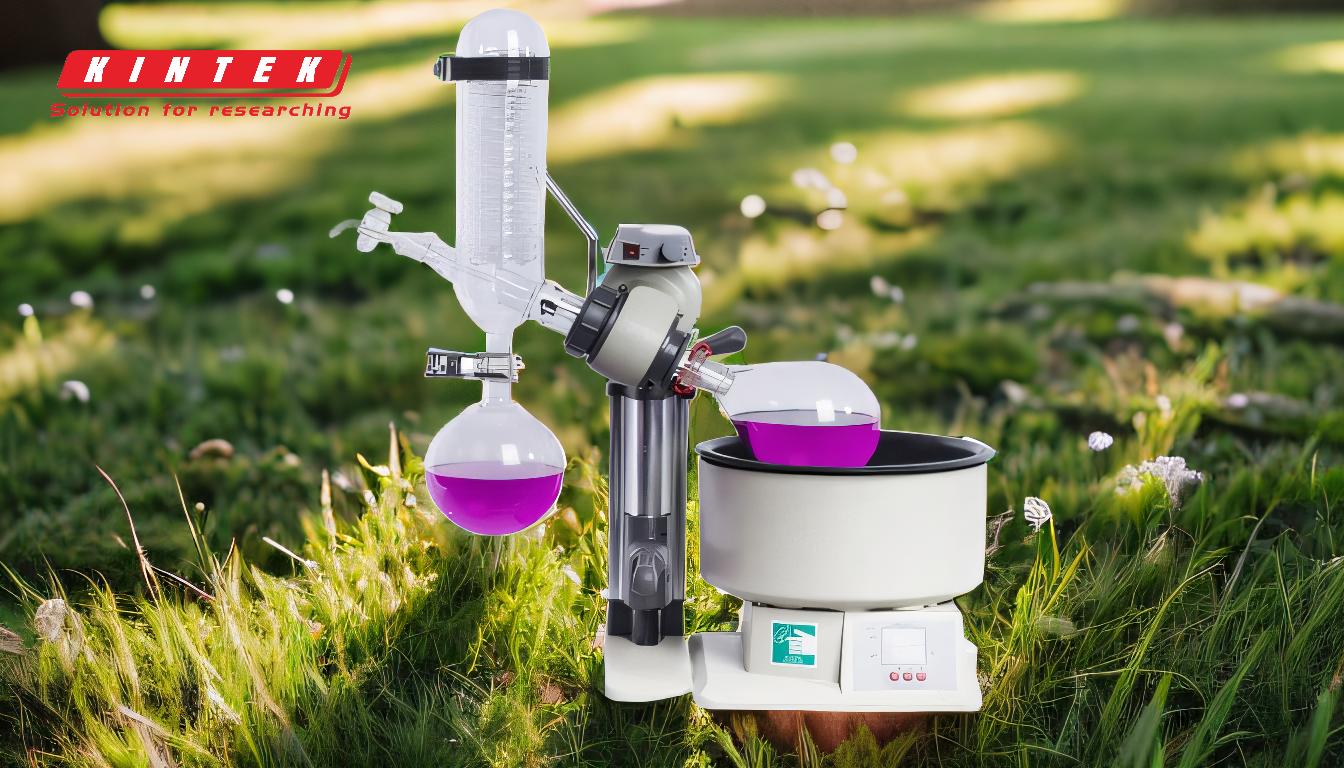
-
Overview of Vacuum Evaporation:
- Vacuum evaporation is a PVD technique that involves heating a material until it evaporates in a vacuum environment.
- The evaporated material travels through the vacuum and deposits onto a substrate, forming a thin film.
- This method is widely used in applications requiring high-purity and precise thin films, such as semiconductor manufacturing, optical coatings, and decorative finishes.
-
Thermal Evaporation Process:
- In thermal evaporation, the target material is placed in an evaporation source, such as a boat, coil, or basket.
- The material is heated using an electric current, which generates heat through electrical resistance, hence the term "resistive evaporation."
- Once the material reaches its evaporation point, it transitions into a gaseous phase and diffuses through the vacuum to the substrate.
-
Advantages of Vacuum Evaporation:
- High Purity: The vacuum environment minimizes contamination, resulting in high-purity thin films.
- Precision: The process allows for precise control over film thickness and uniformity.
- Versatility: A wide range of materials, including metals, alloys, and compounds, can be deposited using this method.
-
Applications of Vacuum Evaporation:
- Electronics: Used to deposit thin films in the production of semiconductors, solar cells, and displays.
- Optics: Applied in the creation of anti-reflective coatings, mirrors, and optical filters.
- Decorative Coatings: Utilized for applying metallic finishes on consumer products like jewelry and automotive parts.
-
Challenges and Considerations:
- Material Limitations: Not all materials are suitable for thermal evaporation due to differences in evaporation temperatures and vapor pressures.
- Equipment Costs: The vacuum chamber and heating elements can be expensive, making the process less economical for some applications.
- Uniformity Control: Achieving uniform film thickness across large substrates can be challenging and may require advanced techniques like planetary substrate rotation.
By understanding these key points, equipment and consumable purchasers can make informed decisions about the suitability of vacuum evaporation for their specific applications and ensure they select the right tools and materials for the process.
Summary Table:
Aspect | Details |
---|---|
Overview | PVD technique for depositing thin films in a vacuum environment. |
Process | Material is heated to evaporation point, vaporizes, and condenses on substrate. |
Advantages | High purity, precise control, versatile material compatibility. |
Applications | Electronics (semiconductors, solar cells), optics (mirrors, filters), decorative coatings. |
Challenges | Material limitations, high equipment costs, uniformity control. |
Interested in vacuum evaporation for your applications? Contact us today to learn more!