Blown film extrusion is a versatile manufacturing process used to create a variety of thin plastic films and products. This process is widely employed across industries such as food packaging, construction, agriculture, and medical sectors. The products made through blown film extrusion include bags, liners, wraps, and tubing, which are essential for packaging, protection, and transportation purposes. The process involves extruding molten plastic through a circular die, inflating it into a bubble, and then cooling it to form a continuous film. This method is favored for its ability to produce high-quality, customizable, and cost-effective plastic films.
Key Points Explained:
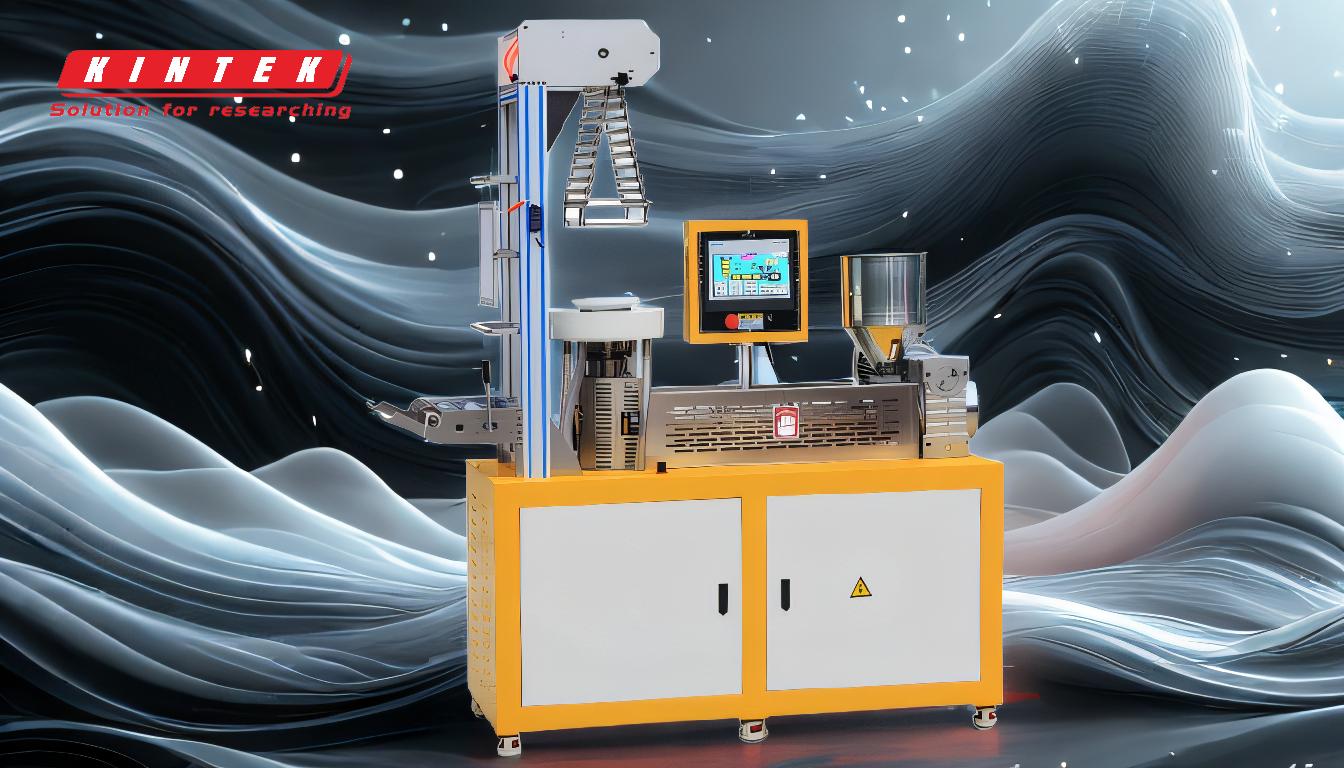
-
What is Blown Film Extrusion?
- Blown film extrusion is a manufacturing process used to produce thin plastic films.
- It involves extruding molten plastic through a circular die, inflating it into a bubble, and then cooling it to form a continuous film.
- This process is known for its ability to create films with uniform thickness and excellent mechanical properties.
-
Common Applications of Blown Film Extrusion:
- Food Packaging: Products such as grocery bags, produce bags, and food wraps are commonly made using blown film extrusion. These films provide a barrier against moisture, air, and contaminants, ensuring the freshness and safety of food products.
- Construction: Blown film extrusion is used to produce construction films like vapor barriers, protective wraps, and geomembranes. These films are essential for moisture control, insulation, and protection in building projects.
- Agriculture: Agricultural films, including mulch films, greenhouse films, and silage bags, are produced using this process. These films help in crop protection, soil moisture retention, and temperature regulation.
- Medical Industry: Blown film extrusion is used to create medical tubing, sterile packaging, and other medical-grade films. These products require high levels of cleanliness, precision, and durability.
-
Types of Products Produced:
- Bags: Blown film extrusion is widely used to produce various types of bags, such as shopping bags, garbage bags, and zipper bags. These bags are lightweight, durable, and can be customized in terms of size, thickness, and color.
- Liners: Liners for containers, bins, and tanks are often made using blown film extrusion. These liners provide a protective barrier against leaks, spills, and contamination.
- Wraps: Plastic wraps, including stretch films and shrink films, are produced using this process. These wraps are used for bundling, palletizing, and protecting goods during storage and transportation.
- Tubing: Blown film extrusion is used to create plastic tubing for various applications, such as medical tubing, irrigation tubing, and flexible hoses. These tubes are designed to be flexible, durable, and resistant to chemicals and environmental factors.
-
Advantages of Blown Film Extrusion:
- Versatility: The process can produce films with a wide range of thicknesses, widths, and properties, making it suitable for diverse applications.
- Cost-Effectiveness: Blown film extrusion is a cost-efficient method for producing large volumes of plastic films.
- Customization: The process allows for easy customization in terms of material composition, color, and surface finish.
- Quality: Films produced through blown film extrusion have excellent mechanical properties, including high tensile strength, tear resistance, and puncture resistance.
-
Materials Used in Blown Film Extrusion:
- Polyethylene (PE): The most commonly used material in blown film extrusion, available in various forms such as Low-Density Polyethylene (LDPE), Linear Low-Density Polyethylene (LLDPE), and High-Density Polyethylene (HDPE).
- Polypropylene (PP): Used for films that require higher stiffness, clarity, and heat resistance.
- Polyvinyl Chloride (PVC): Used for films that require flexibility, transparency, and chemical resistance.
- Ethylene Vinyl Acetate (EVA): Used for films that require enhanced flexibility, clarity, and adhesion properties.
-
Considerations for Equipment and Consumables Purchasers:
- Material Selection: Choose the appropriate type of plastic resin based on the desired properties of the final product, such as flexibility, strength, and barrier properties.
- Die Design: Consider the die design and size, as it directly affects the thickness and width of the produced film.
- Cooling System: Ensure the cooling system is efficient to achieve uniform cooling and prevent defects in the film.
- Extrusion Line Configuration: Select the right configuration of the extrusion line, including the extruder, die, air ring, and winding system, to meet production requirements.
- Quality Control: Implement quality control measures to ensure the consistency and quality of the produced films.
In conclusion, blown film extrusion is a highly versatile and efficient process for producing a wide range of plastic films and products. Understanding the key aspects of this process, including its applications, advantages, and material considerations, is essential for equipment and consumables purchasers to make informed decisions and achieve optimal results.
Summary Table:
Aspect | Details |
---|---|
Process | Extrudes molten plastic through a circular die, inflates into a bubble, and cools to form a continuous film. |
Applications | Food packaging, construction, agriculture, and medical industries. |
Products | Bags, liners, wraps, and tubing. |
Advantages | Versatility, cost-effectiveness, customization, and high-quality output. |
Common Materials | Polyethylene (PE), Polypropylene (PP), Polyvinyl Chloride (PVC), EVA. |
Key Considerations | Material selection, die design, cooling system, extrusion line configuration, and quality control. |
Learn how blown film extrusion can meet your production needs—contact us today!