Sputtering is a physical vapor deposition (PVD) process based on the transfer of kinetic energy from high-energy ions to the atoms of a solid target material. This energy transfer causes the target atoms to be ejected from the surface and deposited onto a nearby substrate, forming a thin film. The process relies on the bombardment of the target by ions (typically argon) in a vacuum environment, where the ions are accelerated toward the target due to an applied electrical potential. The efficiency of the process, known as the sputtering yield, depends on factors such as the energy of the incident ions, the mass of the ions and target atoms, and the angle of ion incidence. This method is widely used in industries for coating substrates with thin films of various materials.
Key Points Explained:
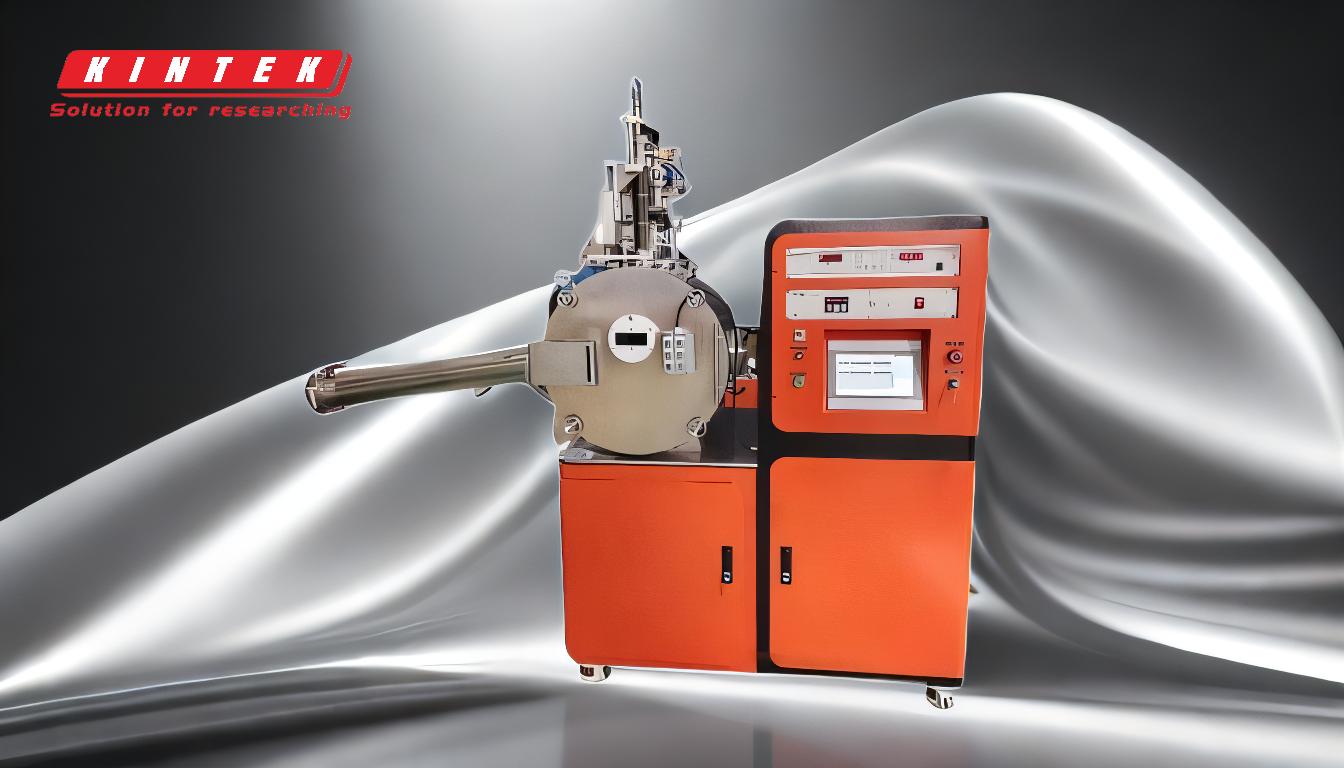
-
Energy Transfer Mechanism:
- Sputtering is fundamentally based on the transfer of kinetic energy from high-energy ions to the atoms of a solid target material. When ions (usually argon) are accelerated toward the target, they collide with the target atoms, transferring their kinetic energy.
- This energy transfer causes a cascade of collisions within the target material, leading to the ejection of target atoms when the energy exceeds the binding energy of the atoms.
-
Role of Incident Ions:
- The incident ions, typically argon, are generated in a plasma within a vacuum chamber. These ions are accelerated toward the target by applying a negative electrical potential to the target.
- The energy of the incident ions is a critical factor in determining the sputtering yield, which is the number of target atoms ejected per incident ion.
-
Sputtering Yield:
- The sputtering yield depends on several factors, including the energy of the incident ions, the mass of the ions and target atoms, and the angle at which the ions strike the target.
- Different target materials and sputtering conditions will result in varying sputtering yields, influencing the efficiency of the process.
-
Vacuum Environment:
- Sputtering takes place in a vacuum chamber to prevent interactions with air or other unwanted gases. This ensures that the sputtered particles travel unimpeded to the substrate.
- The vacuum environment also helps in maintaining the purity of the deposited film and allows for precise control over the deposition process.
-
Deposition of Thin Films:
- The ejected target atoms traverse the vacuum chamber and deposit onto a substrate, forming a thin film. The substrate is typically mounted opposite the target.
- Even heat-sensitive substrates, such as plastics, can be coated using sputtering due to the low temperature of the sputtered particles.
-
Process Gas and Electrical Potential:
- The vacuum chamber is backfilled with a process gas, such as argon, oxygen, or nitrogen, to create the plasma necessary for generating the incident ions.
- A negative electrical potential applied to the target material causes free electrons to accelerate away from the magnetron, leading to the ionization of the process gas and the generation of ions.
-
Factors Influencing Sputtering:
- Chamber pressure, the kinetic energy of emitted particles, and the type of power source (DC or RF) are additional factors that influence the sputtering process.
- These factors affect the deposition rate, material compatibility, and the quality of the deposited film.
-
Applications and Advantages:
- Sputtering is widely used in various industries for coating substrates with thin films of materials such as metals, semiconductors, and insulators.
- The process offers advantages such as the ability to coat heat-sensitive substrates, high purity of the deposited films, and precise control over the film thickness and composition.
By understanding these key points, one can appreciate the complexity and versatility of the sputtering process, which makes it a valuable technique in modern manufacturing and materials science.
Summary Table:
Key Aspect | Description |
---|---|
Energy Transfer Mechanism | Kinetic energy from ions ejects target atoms, forming thin films. |
Incident Ions | Argon ions are accelerated by electrical potential, impacting the target. |
Sputtering Yield | Depends on ion energy, mass, and angle of incidence. |
Vacuum Environment | Ensures purity and precision by preventing gas interactions. |
Thin Film Deposition | Ejected atoms deposit on substrates, including heat-sensitive materials. |
Process Gas & Potential | Argon or other gases ionize under electrical potential to generate ions. |
Influencing Factors | Chamber pressure, particle energy, and power source type affect the process. |
Applications | Used in industries for coating metals, semiconductors, and insulators. |
Discover how sputtering can enhance your manufacturing process—contact us today for expert guidance!