Additive manufacturing, commonly known as 3D printing, has revolutionized the way we create objects by enabling the layer-by-layer construction of complex geometries. The materials used in additive manufacturing are diverse and tailored to specific applications, ranging from polymers and metals to ceramics and composites. Each material category offers unique properties, such as strength, flexibility, thermal resistance, or biocompatibility, making them suitable for industries like aerospace, healthcare, automotive, and consumer goods. The choice of material depends on the desired functionality, manufacturing process, and end-use requirements. This answer explores the primary material types used in additive manufacturing, their characteristics, and their applications.
Key Points Explained:
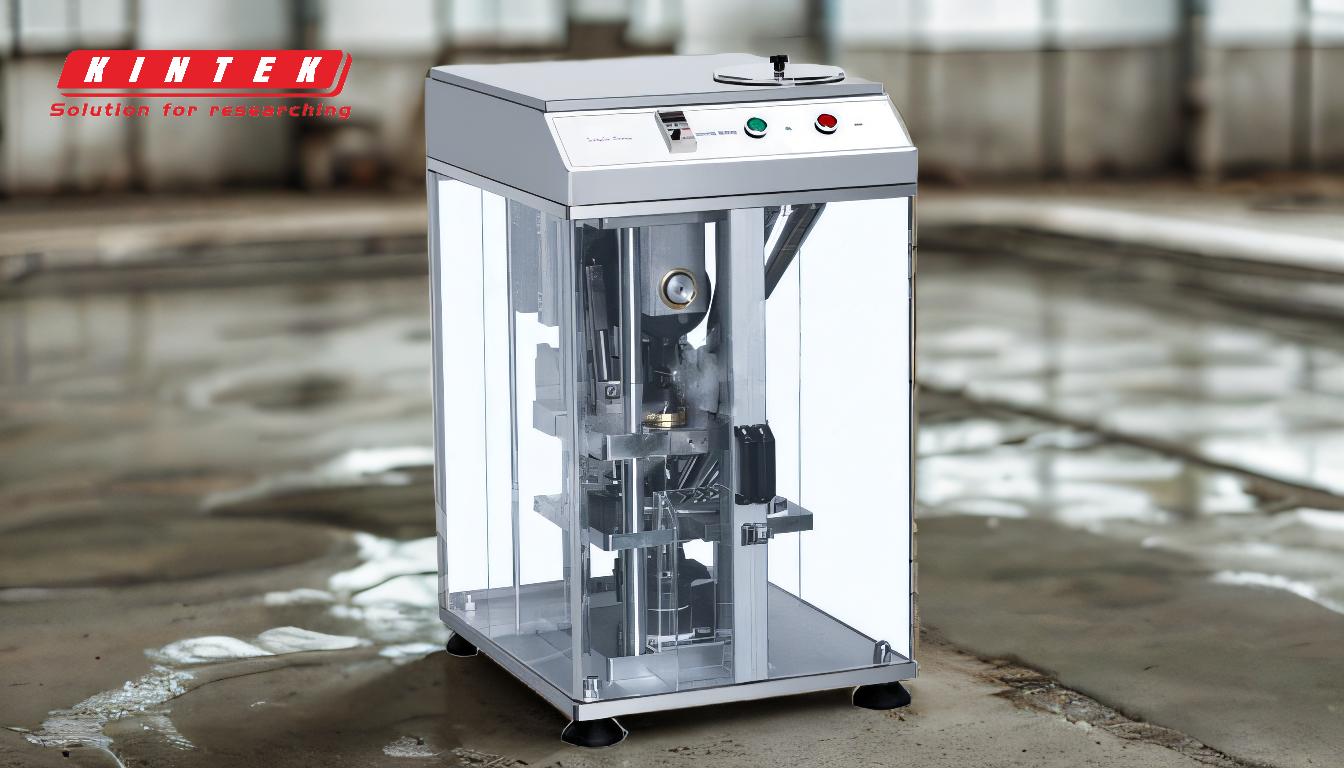
-
Polymers:
- Polymers are the most widely used materials in additive manufacturing due to their versatility, ease of processing, and cost-effectiveness.
- Common polymer types include:
- Thermoplastics: Materials like PLA (Polylactic Acid), ABS (Acrylonitrile Butadiene Styrene), and PETG (Polyethylene Terephthalate Glycol) are popular for their ease of use, durability, and recyclability. They are often used in prototyping, consumer products, and educational applications.
- Photopolymers: These are liquid resins that solidify when exposed to UV light, commonly used in Stereolithography (SLA) and Digital Light Processing (DLP) technologies. They are ideal for high-detail models, dental applications, and jewelry.
- Elastomers: Flexible materials like TPU (Thermoplastic Polyurethane) are used for creating soft, rubber-like parts, such as gaskets, seals, and wearable devices.
- Applications: Prototyping, medical devices, consumer goods, and custom parts.
-
Metals:
- Metal additive manufacturing is critical for high-performance applications requiring strength, durability, and thermal resistance.
- Common metals include:
- Titanium Alloys: Known for their high strength-to-weight ratio and biocompatibility, titanium alloys are widely used in aerospace and medical implants.
- Aluminum Alloys: Lightweight and corrosion-resistant, aluminum is used in automotive and aerospace components.
- Stainless Steel: Offers excellent mechanical properties and is used in industrial tools, automotive parts, and medical instruments.
- Nickel Alloys: These are used in high-temperature applications, such as turbine blades and heat exchangers, due to their thermal and corrosion resistance.
- Processes: Common metal additive manufacturing techniques include Direct Metal Laser Sintering (DMLS), Selective Laser Melting (SLM), and Electron Beam Melting (EBM).
- Applications: Aerospace, automotive, healthcare, and industrial manufacturing.
-
Ceramics:
- Ceramics are used in additive manufacturing for applications requiring high thermal stability, hardness, and biocompatibility.
- Common ceramic materials include:
- Alumina (Aluminum Oxide): Known for its high strength and thermal resistance, used in electronics and industrial components.
- Zirconia (Zirconium Dioxide): Offers excellent mechanical properties and is used in dental crowns, implants, and cutting tools.
- Silicon Carbide: Used in high-temperature and wear-resistant applications, such as aerospace and energy sectors.
- Processes: Ceramic additive manufacturing often involves binder jetting or stereolithography, followed by sintering to achieve final properties.
- Applications: Medical implants, electronics, aerospace, and energy.
-
Composites:
- Composite materials combine two or more materials to achieve superior properties, such as enhanced strength, stiffness, or thermal resistance.
- Common composites include:
- Carbon Fiber Reinforced Polymers (CFRP): These materials are lightweight and strong, making them ideal for aerospace, automotive, and sports equipment.
- Glass Fiber Reinforced Polymers (GFRP): Used in applications requiring durability and corrosion resistance, such as marine and construction industries.
- Metal Matrix Composites (MMC): Combine metals with ceramics or other reinforcements to improve strength and wear resistance.
- Applications: Aerospace, automotive, sports, and industrial components.
-
Biomaterials:
- Biomaterials are used in additive manufacturing for medical and healthcare applications, often requiring biocompatibility and bioresorbability.
- Common biomaterials include:
- Bioresorbable Polymers: Materials like PCL (Polycaprolactone) and PLA are used for temporary implants and tissue engineering scaffolds.
- Hydrogels: Used in bioprinting for creating soft tissues and drug delivery systems.
- Titanium and Cobalt-Chromium Alloys: Used for permanent implants, such as hip and knee replacements.
- Applications: Medical implants, tissue engineering, and drug delivery systems.
-
Specialty Materials:
- Specialty materials are designed for niche applications, offering unique properties such as conductivity, transparency, or magnetic properties.
- Examples include:
- Conductive Polymers: Used in printed electronics and sensors.
- Transparent Polymers: Used in optical components and lenses.
- Magnetic Materials: Used in actuators and sensors.
- Applications: Electronics, optics, and advanced sensors.
In conclusion, the materials used in additive manufacturing are vast and tailored to meet specific functional and performance requirements. From polymers and metals to ceramics and composites, each material category offers unique advantages, enabling the production of innovative and high-performance parts across various industries. Understanding the properties and applications of these materials is essential for selecting the right material for a given additive manufacturing project.
Summary Table:
Material Type | Examples | Key Properties | Applications |
---|---|---|---|
Polymers | PLA, ABS, TPU, Photopolymers | Versatile, cost-effective, flexible | Prototyping, consumer goods, medical devices |
Metals | Titanium, Aluminum, Stainless Steel | High strength, thermal resistance | Aerospace, automotive, healthcare |
Ceramics | Alumina, Zirconia, Silicon Carbide | Thermal stability, hardness, biocompatibility | Medical implants, electronics, aerospace |
Composites | CFRP, GFRP, Metal Matrix Composites | Enhanced strength, stiffness, lightweight | Aerospace, automotive, sports equipment |
Biomaterials | PCL, Hydrogels, Titanium Alloys | Biocompatibility, bioresorbability | Medical implants, tissue engineering |
Specialty Materials | Conductive Polymers, Transparent Polymers | Conductivity, transparency, magnetic properties | Electronics, optics, sensors |
Need help selecting the right material for your additive manufacturing project? Contact our experts today!