Yes, aluminum and steel can be brazed together, but it requires careful consideration of material properties, surface preparation, and the selection of appropriate brazing techniques and filler materials. Brazing these two dissimilar metals is challenging due to their differing melting points, thermal expansion rates, and surface oxide layers. However, with proper techniques, a strong and reliable joint can be achieved.
Key Points Explained:
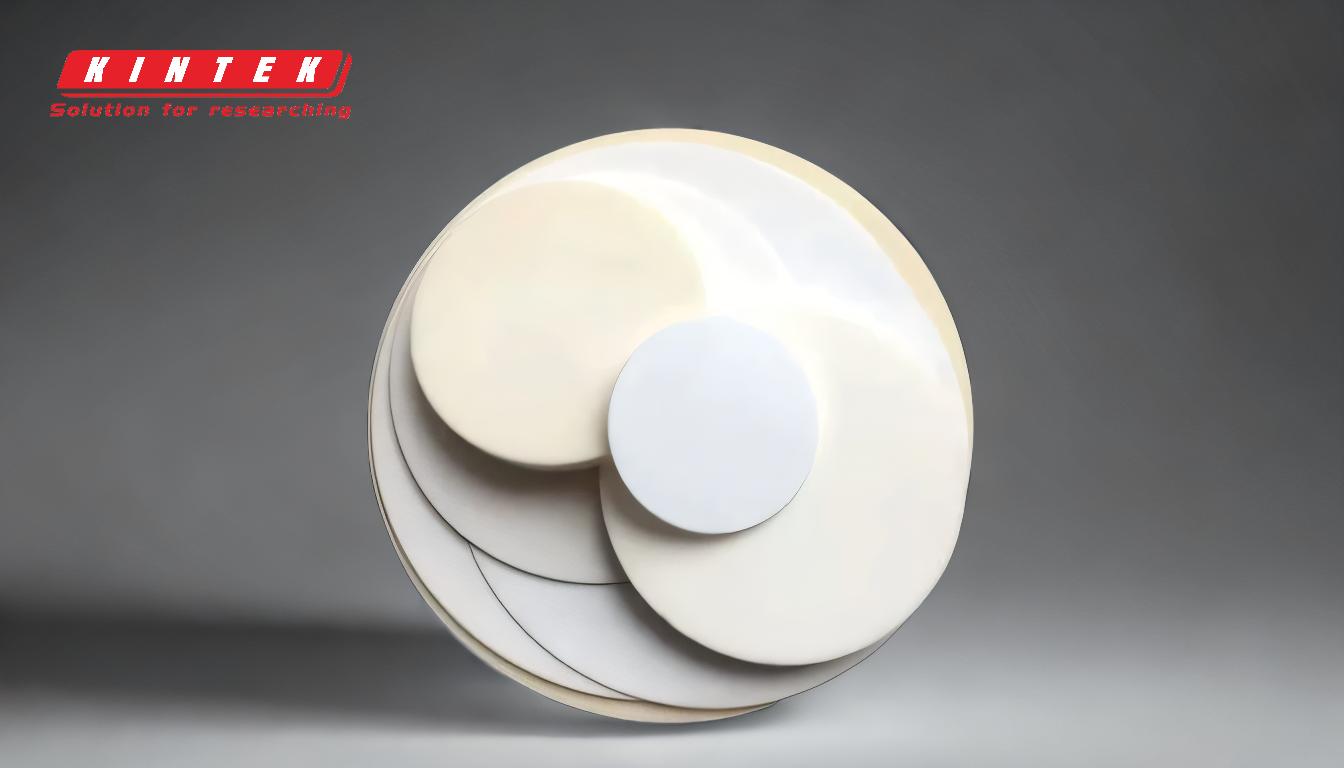
-
Challenges in Brazing Aluminum and Steel:
- Differing Melting Points: Aluminum has a lower melting point (around 660°C) compared to steel (around 1370°C). This requires precise temperature control to avoid melting the aluminum while achieving sufficient heat for the brazing process.
- Thermal Expansion Rates: Aluminum expands more than steel when heated, which can lead to stress and potential cracking in the joint if not managed properly.
- Surface Oxide Layers: Both aluminum and steel form oxide layers that can inhibit bonding. Aluminum oxide, in particular, is highly stable and must be removed or chemically treated before brazing.
-
Surface Preparation:
- Cleaning: Both metals must be thoroughly cleaned to remove oils, dirt, and oxides. This can be done using chemical cleaning agents or mechanical methods like abrasion.
- Surface Treatment: For aluminum, chemical treatments such as flux application or specialized coatings (e.g., nickel plating) can help improve wetting and bonding. Steel may require similar treatments to ensure a clean, oxide-free surface.
-
Filler Material Selection:
- Aluminum-Based Fillers: Common aluminum brazing fillers include aluminum-silicon alloys, which have melting points compatible with aluminum and provide good wetting properties.
- Specialized Fillers: For brazing aluminum to steel, specialized filler materials like zinc-aluminum alloys or silver-based brazing alloys are often used. These fillers bridge the gap between the two metals and provide a strong bond.
-
Brazing Techniques:
- Furnace Brazing: This method is often used for complex assemblies, as it provides uniform heating and precise temperature control. Proper furnace operation is critical to prevent issues like splatter, quench cracking, and distortion.
- Flame Brazing: Suitable for smaller components, flame brazing requires careful control of the heat source to avoid overheating the aluminum.
- Induction Brazing: This technique uses electromagnetic induction to heat the joint locally, minimizing thermal stress and distortion.
-
Common Problems and Solutions:
- Splatter of Braze Alloy: This can be prevented by controlling the cleanliness of the parts and ensuring proper filler material placement.
- Quench Cracking: Gradual cooling or controlled cooling rates can help prevent cracking caused by rapid temperature changes.
- Distortion: Proper fixturing and uniform heating can minimize distortion during the brazing process.
-
Applications:
- Brazed aluminum-steel joints are commonly used in industries such as automotive (e.g., heat exchangers), aerospace, and electronics, where lightweight and strong connections are required.
By addressing these key points, brazing aluminum and steel can be successfully achieved, resulting in durable and reliable joints. Proper preparation, material selection, and technique are essential to overcome the inherent challenges of joining these dissimilar metals.
Summary Table:
Key Aspect | Details |
---|---|
Challenges | Differing melting points, thermal expansion rates, surface oxide layers. |
Surface Preparation | Cleaning, chemical treatments, and coatings for improved bonding. |
Filler Materials | Aluminum-silicon alloys, zinc-aluminum alloys, or silver-based fillers. |
Brazing Techniques | Furnace brazing, flame brazing, or induction brazing for precise results. |
Common Problems | Splatter, quench cracking, distortion—solutions provided. |
Applications | Automotive, aerospace, and electronics industries. |
Need expert advice on brazing aluminum and steel? Contact us today for tailored solutions!