Sputtering is a widely used technique in thin film deposition, and it is indeed possible to sputter silicon. This process involves using a silicon target and following the standard sputtering steps to deposit a thin layer of silicon onto a substrate. The process leverages the principles of ion bombardment and energy transfer to eject silicon atoms from the target, which then deposit onto the substrate to form a thin film. Below, we’ll break down the key aspects of sputtering silicon, including the process steps, considerations, and applications.
Key Points Explained:
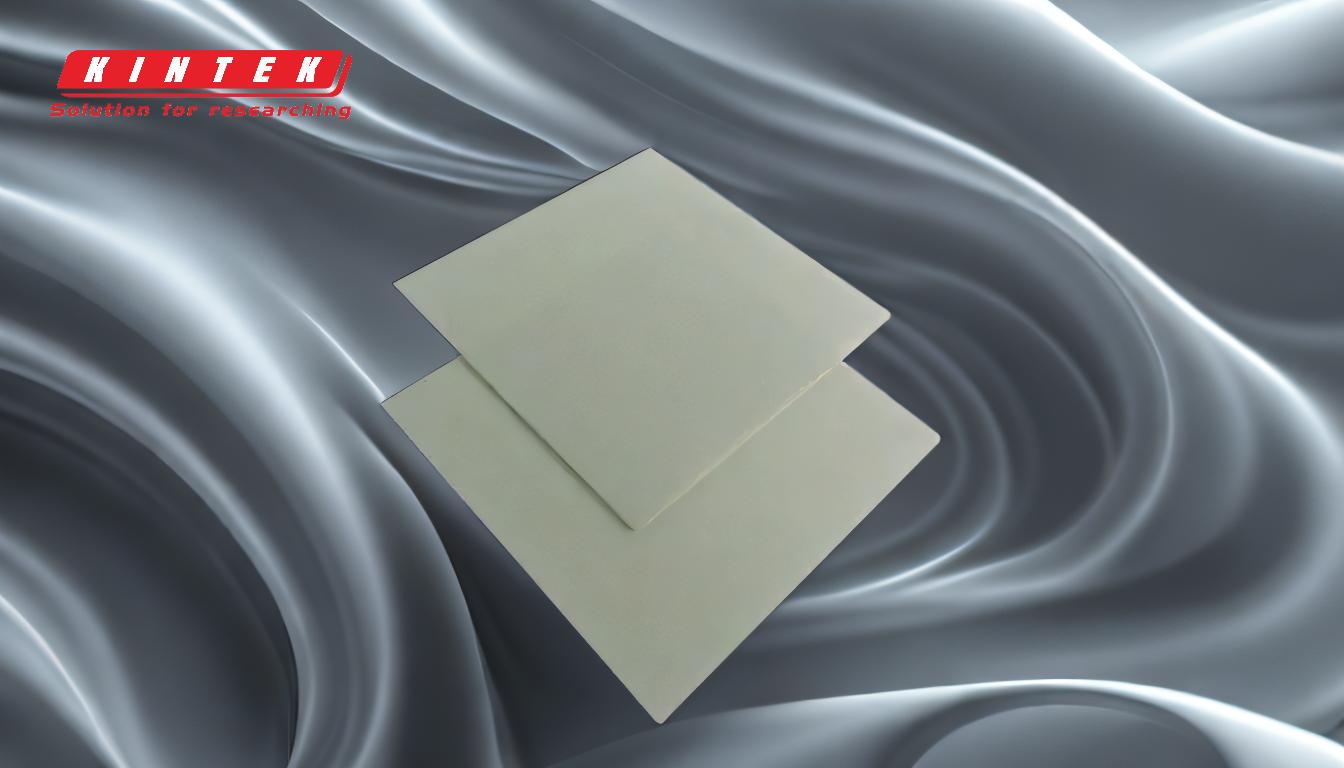
-
Sputtering Process Overview:
- Sputtering is a physical vapor deposition (PVD) technique where a target material (in this case, silicon) is bombarded with high-energy ions of an inert gas, typically argon.
- The collision between the argon ions and the silicon target ejects neutral silicon atoms, which then travel through the vacuum and deposit onto a substrate to form a thin film.
-
Steps to Sputter Silicon:
- Vacuum Creation: The reaction chamber is evacuated to a pressure of around 1 Pa to remove moisture and impurities, ensuring a clean environment for deposition.
- Inert Gas Introduction: Argon gas is introduced into the chamber to create a low-pressure atmosphere, which is essential for ionizing the gas.
- Heating: The chamber is heated to temperatures between 150°C and 750°C, depending on the desired properties of the silicon film.
- Magnetic Field Creation: Tools are placed between the silicon target and an electromagnet to generate a magnetic field, which enhances the ionization of argon gas.
- Ionization and Bombardment: A high voltage is applied to ionize the argon atoms, creating positively charged argon ions. The silicon target is negatively charged, attracting the argon ions. These ions collide with the silicon target, ejecting silicon atoms.
- Film Deposition: The ejected silicon atoms travel through the vacuum and deposit onto the substrate, forming a thin silicon film.
-
Considerations for Sputtering Silicon:
- Target Purity: The quality of the silicon target is critical. High-purity silicon targets are necessary to ensure the deposited film has the desired electrical and structural properties.
- Substrate Preparation: The substrate must be clean and properly prepared to ensure good adhesion and uniformity of the silicon film.
- Process Parameters: Parameters such as gas pressure, temperature, and voltage must be carefully controlled to achieve the desired film properties.
-
Applications of Sputtered Silicon:
- Semiconductor Manufacturing: Sputtered silicon films are used in the production of integrated circuits and other semiconductor devices.
- Optical Coatings: Silicon films are used in optical applications, such as anti-reflective coatings and mirrors.
- Solar Cells: Sputtered silicon is used in the fabrication of thin-film solar cells.
In summary, sputtering silicon is a well-established process that involves several carefully controlled steps to deposit a thin film of silicon onto a substrate. This technique is widely used in industries such as semiconductor manufacturing, optics, and solar energy. By understanding the key steps and considerations, one can effectively utilize sputtering to produce high-quality silicon films for various applications.
Summary Table:
Aspect | Details |
---|---|
Process Overview | Physical vapor deposition (PVD) using argon ions to eject silicon atoms. |
Steps | Vacuum creation, inert gas introduction, heating, magnetic field creation. |
Key Considerations | Target purity, substrate preparation, controlled process parameters. |
Applications | Semiconductor manufacturing, optical coatings, thin-film solar cells. |
Discover how sputtering silicon can elevate your projects—contact our experts today!