Heating elements are critical components in various household appliances like irons, grills, and ovens. They are typically manufactured using resistance wires embedded in insulating ceramic materials, which are then housed within a metal casing. This design ensures efficient heat generation and distribution. However, such heating elements often suffer from thermal inertia, meaning they take time to heat up and cool down, which can affect their efficiency and responsiveness. The manufacturing process involves selecting appropriate materials, shaping the resistance wire, embedding it in ceramic insulation, and encasing it in metal to ensure durability and safety.
Key Points Explained:
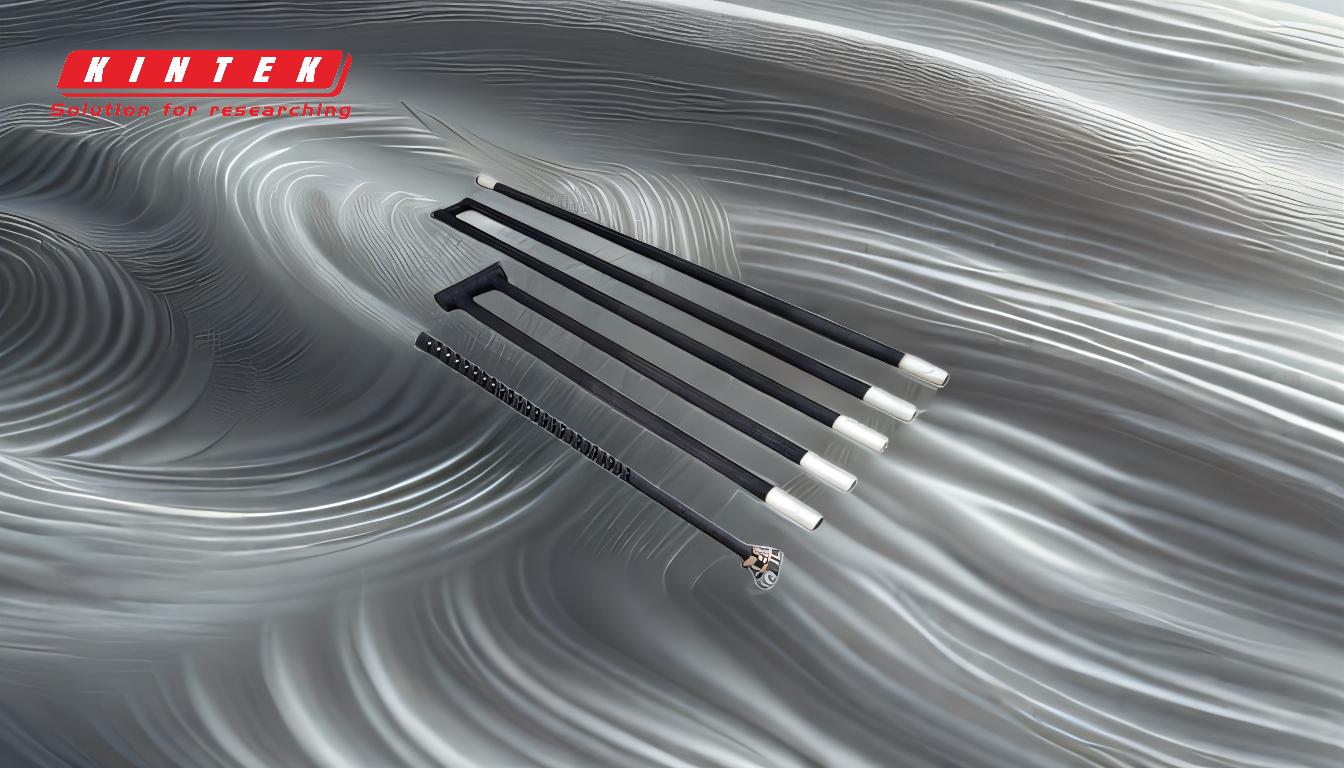
-
Material Selection:
- Resistance Wires: Typically made from alloys like nichrome (nickel-chromium), which have high electrical resistance and can withstand high temperatures without oxidizing.
- Insulating Ceramic: Materials like magnesium oxide (MgO) are used for their excellent thermal insulation and electrical resistance properties.
- Metal Casing: Usually made from stainless steel or other heat-resistant metals to protect the internal components and ensure durability.
-
Resistance Wire Shaping:
- The resistance wire is coiled or shaped into specific configurations to maximize surface area and ensure even heat distribution.
- The shape and size of the wire are crucial for determining the heating element's power rating and efficiency.
-
Embedding in Ceramic Insulation:
- The shaped resistance wire is embedded in a ceramic insulating material, which is chosen for its ability to withstand high temperatures and provide electrical insulation.
- This step ensures that the heat generated by the wire is effectively transferred to the outer casing while preventing electrical shorts.
-
Encasing in Metal:
- The ceramic-embedded wire is then placed inside a metal casing, which serves as the outer shell of the heating element.
- The metal casing provides mechanical protection, ensures even heat distribution, and enhances the overall durability of the heating element.
-
Thermal Inertia:
- The combination of resistance wire, ceramic insulation, and metal casing results in a heating element with significant thermal mass.
- This thermal mass leads to thermal inertia, causing the element to take time to heat up and cool down, which can be a drawback in applications requiring quick temperature changes.
-
Quality Control and Testing:
- After manufacturing, heating elements undergo rigorous testing to ensure they meet safety and performance standards.
- Tests include checking for electrical resistance, insulation integrity, and thermal performance.
-
Applications:
- These heating elements are used in a variety of household appliances, including irons, grills, ovens, and space heaters.
- The design and materials used are tailored to the specific requirements of each application to ensure optimal performance and safety.
By understanding these key points, a purchaser of heating elements can make informed decisions based on the specific needs of their application, considering factors like thermal efficiency, responsiveness, and durability.
Summary Table:
Key Aspect | Details |
---|---|
Material Selection | - Resistance Wires: Nichrome alloys for high resistance and heat tolerance. |
- Insulating Ceramic: Magnesium oxide for thermal and electrical insulation.
- Metal Casing: Stainless steel for durability and heat resistance. | | Resistance Wire Shaping | Coiled or shaped to maximize surface area and ensure even heat distribution. | | Embedding in Ceramic | Ceramic insulation prevents electrical shorts and transfers heat effectively.| | Encasing in Metal | Metal casing provides mechanical protection and even heat distribution. | | Thermal Inertia | High thermal mass causes slower heating and cooling, affecting responsiveness.| | Quality Control | Rigorous testing for electrical resistance, insulation, and thermal performance.| | Applications | Used in irons, grills, ovens, and space heaters for efficient heat generation.|
Looking for durable and efficient heating elements? Contact us today to find the perfect solution for your needs!